Citation: Van Eester C, “Building a Better Prefilled Syringe for Covid-19 Vaccine Packaging”. ONdrugDelivery, Issue 117 (Mar 2021), pp 53–58.
Carina Van Eester shares key learnings since the launch of the company’s NeoFlex plungers at the start of the covid-19 pandemic.
This article first appeared in ONdrugDelivery, Issue 117 (Mar 2021), pp 53–58.
At the onset of the covid-19 pandemic, Datwyler launched its NeoFlex plungers onto the market. A year later, more is known about the virus, the vaccines being developed to fight it and how NeoFlex plungers can be an effective tool in distributing the vaccines to the global population.
“With more filling lines being developed to process ready-to-fill
vials, cartridges and PFSs, the demand for ready-to-use stoppers and plungers is growing every year.”
As is standard for most new drugs entering the market, vials are the preferred option for packaging the drug product. For covid-19 vaccines, this is especially true since vials hold more doses of the vaccine, allowing for more vaccinations, and vial components and filling lines are more widely available to drug developers. Even though vials are the preferred initial packaging for covid-19 vaccines, syringes are the ideal packaging application due to ease of administration, reduced risk of contamination, minimised risk of injuries during use and improved accuracy. With these clear benefits to packaging the covid-19 vaccine in a syringe application, Datwyler’s NeoFlex plungers are well-equipped for packaging this life-saving drug product.
NEOFLEX PLUNGERS FOR SENSITIVE DRUG PRODUCTS
NeoFlex plungers for prefilled syringe (PFS) and cartridge applications are part of Datwyler’s platform of coated products, which also includes OmniFlex stoppers for vial applications. Both OmniFlex stoppers and NeoFlex plungers are made with the same high-quality compound formulation, FM457, and proprietary fluoropolymer spray-coating technology. By using the same compound and technology for the various components, customers can easily transition from an OmniFlex stopper for a vial to a NeoFlex plunger for a syringe or cartridge, with minimal risk to compatibility.
COMPATIBILITY WITH VARIOUS STERILISATION METHODS
One of the biggest differences between OmniFlex stoppers and NeoFlex plungers is the preferred method of sterilisation. In general, stoppers are typically steam sterilised by the manufacturer, whereas plungers are supplied to the customer ready to use (in combination with ready-to-fill syringes packaged in tubs). With more filling lines being developed to process ready-to-fill vials, cartridges and PFSs, the demand for ready-to-use stoppers and plungers is growing every year, and with more demand comes more variety in how these components are processed and sterilised by pharmaceutical companies. To meet the various requirements from customers all over the world, NeoFlex plungers were designed to be compatible with a variety of sterilisation methods. Studies have been conducted to assess the influence of different sterilisation methods on the chemical and functional properties of Datwyler’s fully coated components and the results were positive.
Chemical Properties
“One of the main advantages of NeoFlex plungers is that the compression in the barrel is rather high compared with other coated plungers on the market.”
To determine the chemical properties of FM457 and NeoFlex, the components were tested according to ISO 8871-1, which encompasses the most stringent requirements of the applicable compendial chapters on rubber closures – namely US Pharmacopeia (USP) General Chapter <381>, and European Pharmacopoeia (EP) Chapter 3.2.9. After irradiation up to 40 kGy and storage times of two years, FM457 and NeoFlex continue to adhere to ISO 8871-1 and thus, also adhere to USP <381> and EP 3.2.9. No significant difference is observed between steam sterilisation and gamma irradiation in the standard chemical testing of NeoFlex, and the same is true for extractables.
Functional Properties
The functional properties of NeoFlex plungers, specifically container closure integrity, gliding properties and plunger movement, have been investigated in worst-case conditions.
Container Closure Integrity
Helium (He) leak testing of the plungers treated with steam sterilisation, as well as plungers irradiated with 25 kGy gamma irradiation, show safe He-leak rates for all NeoFlex designs. This test is conducted with nominal plungers and with plungers that are 0.2 mm smaller than the nominal in order to simulate the worst-case conditions for container closure integrity (simulating the plunger at minimum specification and the barrel at maximum specification). Also, as a result of this study, it can be concluded that even the plunger/barrel with the lowest interference shows excellent He-leak rates regardless of whether they were gamma irradiated or steam sterilised (Figure 1).
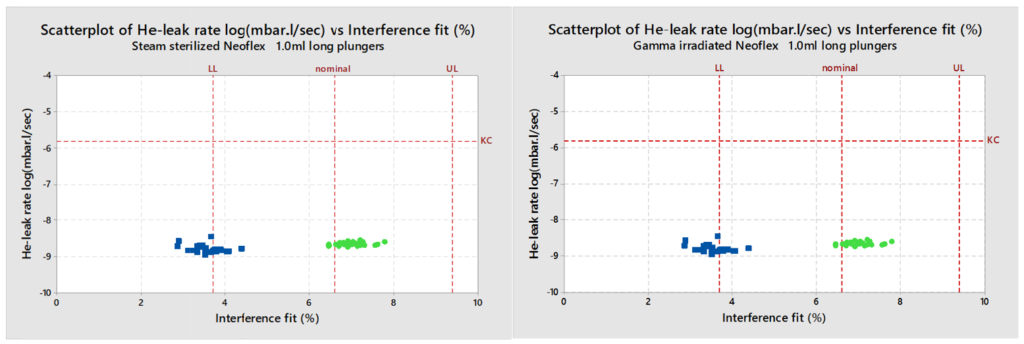
Figure 1: He-leak rates of gamma irradiated 1 mL long NeoFlex plungers with different interference fits. All cases easily meet the Kirsch Criterion (1.6×10–6 mbar.L/sec). Even with the worst-case scenario of a low interference fit, the seal integrity is still maintained.
Gliding Properties
The break-loose force of NeoFlex plungers slightly increases over time and is higher at room temperature and 40°C, but the impact of gamma irradiation versus steam sterilisation is minimal and still within an acceptable range with regard to usability and end-user acceptance criteria. The data that were created with plungers 0.2 mm larger than the nominal (which should represent the worst-case conditions when the barrel is small and plunger is big), show that no significant difference is detected between steam sterilisation and gamma irradiation for break-loose and gliding forces. The same is true for the gliding force. As a result, no difference is detected between steam sterilisation and gamma irradiation (Figure 2).
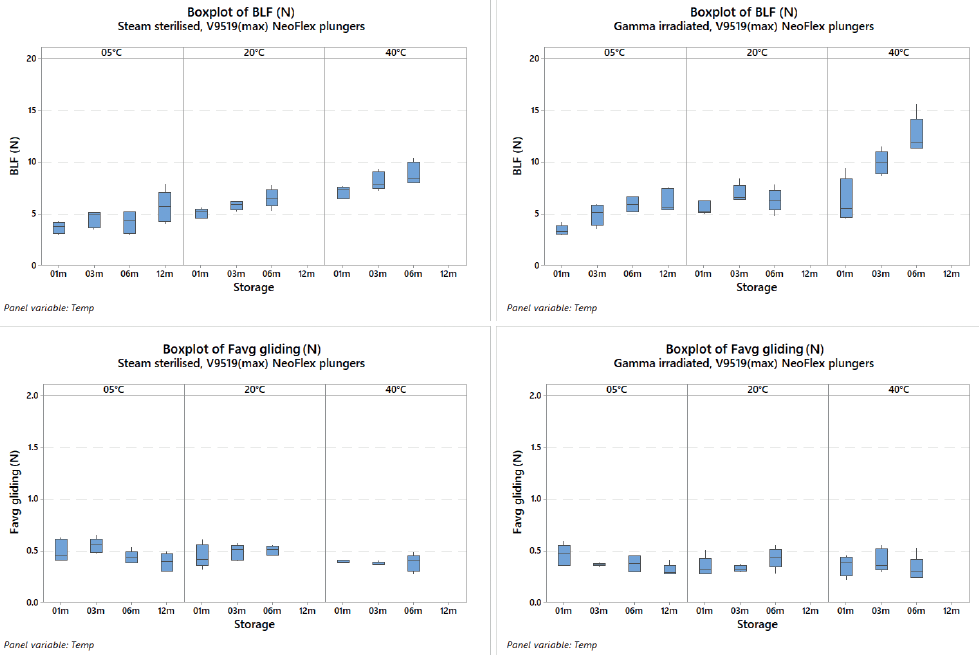
Figure 2: The above graphs show the consistency in break-loose force and gliding forces for both steam and gamma irradiated NeoFlex 1 mL long plungers.
Plunger Movement
This test simulates the conditions of an aeroplane using a pressurised cabin corresponding to an altitude of 8,000 ft, non-pressurised. The test is also performed in worst-case conditions where the plunger is 0.2 mm smaller than nominal to simulate the scenario in which the smallest plunger is positioned in the largest barrel. The plunger impact is the same for both steam-sterilised and gamma-irradiated plungers. In both cases, it can be concluded that syringes filled with a head space below 7 mm will show plunger movement that is lower than the distance between the third and the second rib, and likely can count on two ribs to secure the container closure integrity (Figure 3).
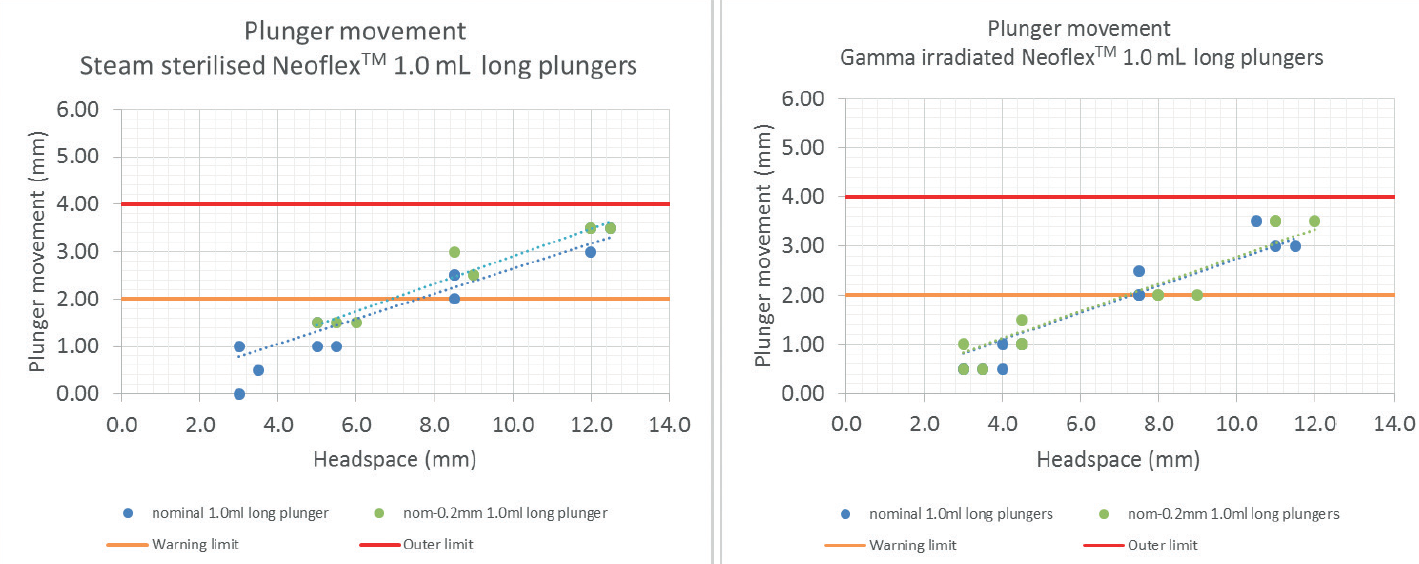
Figure 3: The above graphs show that, for plungers in a highly pressurised setting, plunger movement is minimal and well below the outer limit, regardless of whether the plungers were steam sterilised or gamma irradiated.
A ROBUST DESIGN FOR COLD STORAGE CONDITIONS
“The processability of a coated plunger helps to determine the success of a packaged drug.”
During the functionality testing of NeoFlex plungers, testing was done at 5°C, room temperature and 40°C. In the context of covid-19 vaccines, extremely low temperature storage is required, e.g. -20°C and -80°C. From a theoretical perspective, it can be concluded that storage at -80°C may pose a challenge but storage at -20°C is possible.
When temperatures drop, elastomers harden and become less flexible, and when the temperature reaches the glass transition temperature, elastomers lose their rubber-like properties entirely. At extremely low temperatures, i.e. the brittle point, elastomers may crack. Changes in elastomer properties due to low temperatures are typically physical and fully reversible. For halobutyl rubber – the most common type of rubber used for plungers – the glass transition temperature is around -60°C. For styrene-butadiene rubber – the rubber used for needle shields and tip caps, such as Datwyler’s FM30 – the glass transition temperature is only around -40°C. Thus, the best-case scenario for sealing at low temperatures can only be guaranteed at a minimum temperature of -40°C for syringe applications.
One of the main advantages of NeoFlex plungers is that the compression in the barrel is rather high compared with other coated plungers on the market. NeoFlex has a nominal compression between 6% and 6.6% while other coated plungers have a nominal compression between 2.8% and 3.8%. In addition, the fluoropolymer coating is thin and flexible, which prevents it affecting the sealing properties (Table 1).
1 mL | 1–3 mL | |||||
Compression % | min | nominal | max | min | nominal | max |
NeoFlex™ | 3.73 | 6.62 | 9.42 | 3.85 | 5.98 | 8.06 |
Partially coated plunger 1 | 0.77 | 3.79 | 6.72 | 0.57 | 2.81 | 5.00 |
Partially coated plunger 2 | 2.27 | 5.22 | 8.09 | 2.23 | 4.42 | 6.56 |
Table 1: Comparison of compression percentages between different coated plungers on the market. NeoFlex has a higher compression than other coated plungers on the market, which should have a positive effect on container closure integrity during storage in extreme cold conditions.
In addition to container closure integrity of the plunger and barrel, other functional aspects of the syringe need to be investigated in these extreme cold conditions before a system can be provided and deemed successful at these low temperatures.
NEOFLEX PLUNGERS COMPATIBLE WITH MULTIPLE PLUNGER POSITIONING TECHNOLOGIES
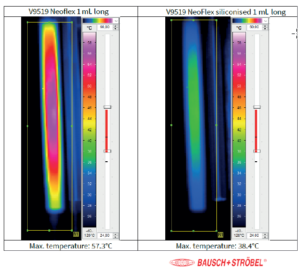
Figure 4: Temperature of vent tube in combination with NeoFlex 1 mL long and NeoFlex siliconised 1 mL long. Data provided by Bausch & Stroebel pharma services.
The processability of a coated plunger helps to determine the success of a packaged drug. In general, it is known that most existing syringe fill-finish lines are equipped with vent tube stoppering for stopper positioning. It is also known that this technology poses challenges for coated plungers. During vent tube placement, the plunger is compressed to a high extent in the vent tube, then a plunger rod pushes it through the vent tube and finally into the syringe where the plunger is deflated and seals the syringe. When the plunger passes through the vent tube, high forces are required and temperature increases. The high forces can be improved by applying a bit of silicone (10–25 μg silicone/cm²) on top of the coating. Figure 4 shows that, during plunger positioning, the temperature increase goes down from 57 °C to 38 °C and the force required for stoppering goes down from 40 N to 25 N. Of course, this is only a viable solution if the drug is not sensitive to silicone.
Another option for plunger positioning is to use a short insertion tube with vacuum assistance. In this scenario, the vent tube can have a larger diameter, which means less compression of the plunger and less friction. Ultimately, the ideal positioning option for coated plungers is using vacuum placement. With the understanding that each technology has specific requirements that impact the final syringe product, NeoFlex plungers were designed to work with each positioning technology and the successful placement of the plungers has been proven with testing at different machine manufacturers.
COMPATIBILITY WITH A VARIETY F SILICONISED BARREL MATERIALS
While glass is still the most widely used material for syringes, plastic barrels in cyclic olefin copolymer (COC) and cyclo olefin polymer (COP) are also emerging as viable options for syringe manufacturing. With regard to the covid-19 vaccines, glass, COC and COP barrels are all being considered to package certain vaccine products due to worldwide shortages of raw materials.
Guaranteeing proper gliding in a syringe with a traditional halobutyl rubber plunger requires that the barrel, regardless of composition, is uniformly siliconised. Depending on the sensitivity of the drug product to silicone, standard siliconised barrels, low siliconised barrels and baked-on or plasma-treated siliconised barrels can be used.
For each of these iterations, NeoFlex plungers perform without concern. Due to the 100% coating of the NeoFlex plunger, the halobutyl rubber never comes into contact with COC or COP barrels, causing the break-loose and gliding forces to be identical to the results obtained in glass barrels. This is not the case with partially coated plungers (Figure 5). NeoFlex plungers were also tested in combination with barrels from different suppliers and only small differences were detected.
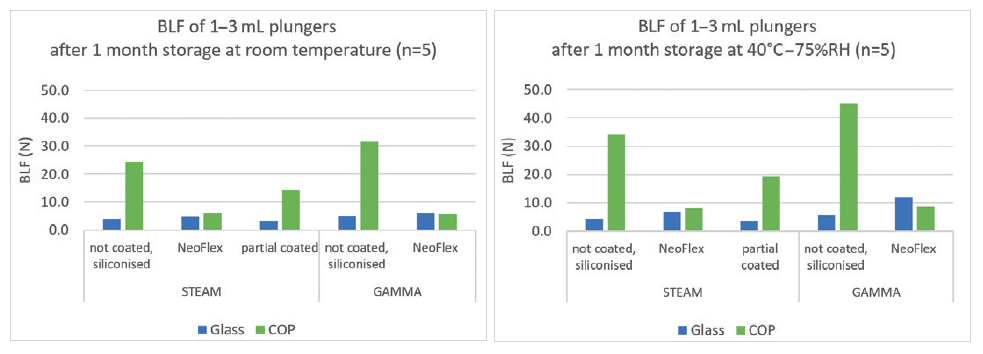
Figure 5: The above graphs show that uncoated and partially coated plungers give much higher break-loose forces then NeoFlex in COP barrels.
CONCLUSION
With an accelerated timeline for manufacturing and distributing the various covid-19 vaccines, it is important that pharmaceutical companies have the necessary packaging available to them as the vaccine transitions from vial applications to PFSs. Datwyler’s NeoFlex plungers are not only ready to be used for these vaccine products but represent an important piece of the puzzle in building a better vaccine packaging solution for drug manufacturers combatting a global pandemic.