Citation: Neveu A, Crowley M, McGorisk T, “Characterisation of Lactose Powders for DPI Applications”. ONdrugDelivery, Issue 119 (Apr-May 2021), pp 46–50.
Aurélien Neveu, Michael Crowley and Tony McGorisk discuss the characterisation of lactose powders for use as excipients in DPI formulations. The authors go on to discuss an analysis of six Kerry lactose powders using GranuTools technology.
INTRODUCTION
Lactose clearly meets the criteria for an ideal carrier for inhalation applications; it is chemically and physically inert to other excipients and APIs, widely available worldwide, well characterised, easy to store, cost-effective and typically has low lot-to-lot variability. Dry powder inhaler (DPI) products are designed to deliver a dry powder formulation to a patient’s lungs, typically consisting of a homogenous blend of the API and an excipient (most often lactose) and contained within a reservoir, capsule or blister prior to inhalation. Such formulations are produced by physically mixing micronised drug particles with the larger excipient “carrier” particles.
“When considering excipients for DPI development, the key considerations are producing a uniform blend for accurate dosing and then proper drug separation during inhalation. Beyond that, reducing batch-to-batch variability is also extremely challenging in these types of formulations.”
Unlike in many conventional tableting formulations, the excipient is an important functional ingredient in a DPI formulation, playing at least two roles in the formulation. Since the API is used in very small quantities, blending with the excipient is necessary to enable its delivery to the desired location within the lung. Second, the excipient must separate from the drug during inhalation so that the drug can be inhaled into the patient’s lungs.
The excipient’s physical properties and interfacial forces affect the blend uniformity and drug release characteristics of the DPI formulation. Some of these properties include the particle size distribution, flowability, surface chemistry, morphology and electrostatic properties of the excipient. It is critical that these characteristics are controlled during manufacture and storage of the excipient. When considering excipients for DPI development, the key considerations are producing a uniform blend for accurate dosing and then proper drug separation during inhalation. Beyond that, reducing batch-to-batch variability is also extremely challenging in these types of formulations.
Development of a robust DPI product depends on understanding the aforementioned characteristics of the inhalation carrier and the effects that variations in these characteristics have on the performance of the DPI product. However, the analytical methods used to measure these characteristics vary between suppliers of inhalation lactose, users and academics interested in dry powder inhalation. Additionally, many simple, traditional excipient tests, such as sieve particle size testing, are not adequate for producing a robust DPI formulation. Formulation variability can be reduced if better methods are employed to reduce batch-to-batch variability of the excipient.
During the last decade, GranuTools has updated these techniques to meet the present requirements of R&D laboratories and production departments. In particular, measurement processes have been automated and rigorous initialisation methods have been developed to obtain reproducible and interpretable results. This article details an investigation into the packing dynamics, flowability and tribocharging properties of six lactose powders. The authors show how these methods can help to gather important information on powder behaviour, which in turn can help with the design of new products with improved performance.
EXPERIMENTAL METHOD
“During the last decade, GranuTools has updated these techniques to meet the present requirements of R&D laboratories and production departments. In particular, measurement processes have been automated and rigorous initialisation methods have been developed to obtain reproducible and interpretable results.”
Dynamic Cohesive Index (GranuDrum)
GranuDrum is a tool for investigating the rheology of powders, using an automated powder flowability measurement method based on the rotating drum principle. A small amount of powder (50 mL in this study) is placed in a horizontal drum with transparent sidewalls. The drum rotates around its axis at an angular velocity of 2–60 rpm. Snapshots (40 images at one-second intervals) are taken by a charge-coupled device (CCD) camera for each angular velocity. The air/powder interface is detected on each picture using an edge detection algorithm.
Afterwards, the average interface position and the fluctuations around this average position are computed. For each angular velocity, the dynamic cohesive index is measured from the temporal interface fluctuations, which are caused solely by the cohesive forces acting between the grains.1 Therefore, the dynamic cohesive index is close to zero for non-cohesive powders and increases as the cohesive forces intensify. Furthermore, by varying the rotation rate, complex rheological properties of powders (shear thinning, shear thickening and thixotropic behaviour) can be investigated.
Tapped Density Analysis
The “tap-tap” test, which measures the bulk density, tapped density and Hausner ratio, is a popular method for powder characterisation because it is both simple and fast. The packing dynamics of a powder give useful information about its cohesive behaviour; a more cohesive powder is able to sustain a looser packing at rest, extending its packing range compared with a less cohesive one. The Hausner ratio, defined as the ratio of the tapped to the apparent (untapped) bulk density, is thus a measure of the cohesiveness of powders – the higher the Hausner ratio, the higher the cohesiveness.
In this study, the packing properties of powders were investigated with the GranuPack instrument (GranuTools), which uses an automated and improved tapped density measurement method.2 The powder is placed in a metallic tube with a rigorous automated initialisation process. The height (h) of the powder bed is measured automatically after each tap using an inductive sensor. From h, the volume (V) of the pile is computed. As the powder sample mass (m) is known, the bulk density (ρ) is evaluated and plotted after each tap.
The bulk density is the ratio between m and V. With the GranuPack method, the results are reproducible with a small quantity of powder (typically 35 mL). The Hausner ratio (Hr) is related to the compaction ratio and is calculated by the equation Hr = ρ(500) / ρ(0), where ρ(0) is the initial bulk density and ρ(500) the tapped density obtained after 500 taps. In this study, three independent tests were performed on fresh powder.
Tribocharging Sensitivity
Electrostatic charges of the excipient and API particles can affect the performance of DPI drug formulations. Electrostatic forces on the excipient could cause the API particle to adhere to the surface of the excipient and prevent release. Furthermore, electrostatic forces in the final blend could affect the release of the powder from the DPI device. Therefore, variability in charge profiles could cause variability in the final drug fine particle fraction (the API that is released to the patient).
Characterisation of these charges can prove to be an important tool for achieving a higher percentage of the API being released from the excipient/device. Managing or controlling these charges could also be an important factor for reducing the variability of API release. Lastly, measurement of charge could be an important tool for the excipient manufacturer and drug formulator in determining if there is a build-up or variation of charge during manufacturing.
The tribocharging properties of the selected excipients were investigated with the GranuCharge (Granutools).3 First, the initial charge density (q0) is measured by pouring 55 mL of powder into a Faraday cup. The powder then flows through a V-shape stainless steel (SS316L) pipe and the final charge density (qf) is measured. Finally, the charge density variation (Δq) is calculated as Δq = (q0-qf).
MATERIALS
Kerry is a leading pharmaceutical-grade lactose supplier and offers a full line of lactose for inhalation under its Aero Flo® brand name. For this study, six of these grades of lactose powders specifically designed for DPI applications were selected.
Powder | Type | D10 (μm) | D50 (μm) | D90 (μm) |
Aero Flo® 25, NF Anhydrous |
Milled | 1-6 | 18-26 | 60-85 |
Aero Flo® 35, NF Monohydrate |
Milled | 3-12 | 28-42 | 70-95 |
Aero Flo® 55, NF Monohydrate |
Milled | 6-16 | 48-62 | 115-135 |
Aero Flo® 60S, NF Monohydrate |
Milled/Sieved | 19-43 | 53-66 | 75-106 |
Aero Flo® 65, NF Monohydrate |
Milled | 9-18 | 55-70 | 135-160 |
Aero Flo® 85S, NF Anhydrous |
Milled/Sieved | 15-50 | 70-105 | 170-220 |
Table 1: Type and size distribution of the particles composing the five powders.
Particle size distribution is summarised in Table 1. The Aero Flo® 25 has the smallest particle size and the most fines (smallest D10). Powders Aero Flo® 60S and Aero Flo® 85S are sieved and thus have the fewest fines. All samples are monohydrate powders, except Aero Flo® 25 and Aero Flo® 85S which are anhydrous. The milling production method of the powders produces particles with a “shard” shape as seen in the single electron microscope (SEM) images presented in Figure 1.
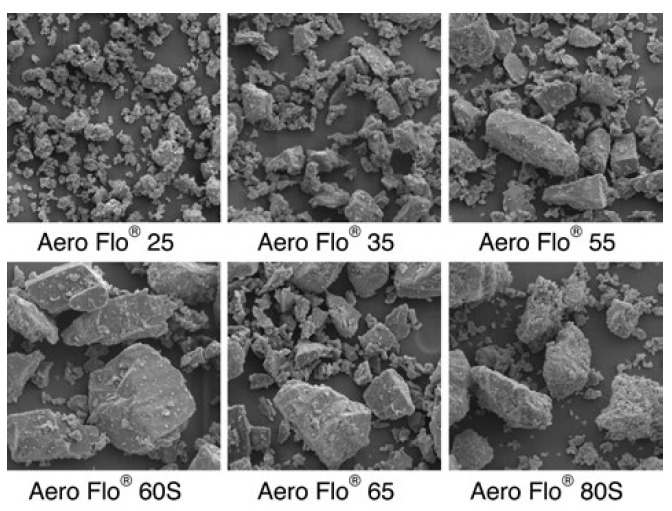
Figure 1: SEM images of the powders at a magnification x300.
RESULTS AND DISCUSSION
Packing Dynamics
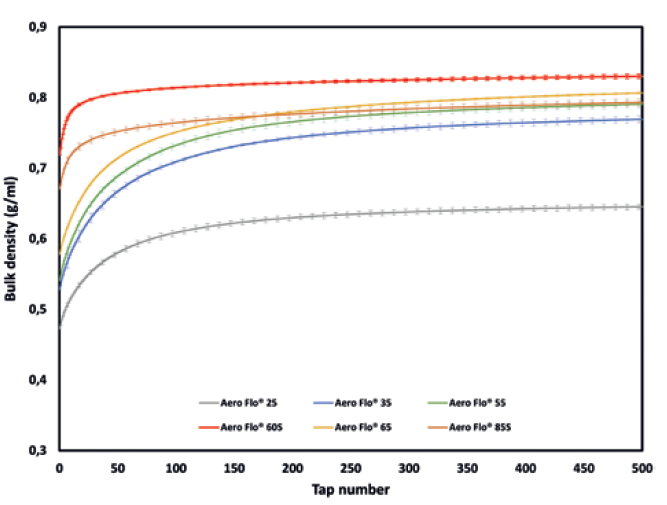
Figure 2: Bulk density versus the number of taps obtained with the GranuPack.
Packing curves obtained with the GranuPack are presented in Figure 2 and summarised in Table 2. From these results, the tested powders can be clearly differentiated by their packing behaviour. Indeed, Aero Flo® 60S and Aero Flo® 85S exhibit a Hausner ratio below 1.20, which is commonly associated with good flowability. Aero Flo® 25 and Aero Flo® 65 have an intermediate-to-high Hausner ratio. Finally, Aero Flo® 35 and Aero Flo® 55 demonstrate a higher Hausner ratio, and thus have the higher cohesiveness among the tested powders.
The global cohesiveness of a powder usually decreases with increasing particle size, and so the good flowability of Aero Flo® 85S can be attributed to its larger particle size (D50 = 70-105 μm). Aero Flo® 60S and Aero Flo® 65 have a similar D50 but the higher D10 of Aero Flo® 60S, indicating fewer fines, is probably why this powder exhibits the best flowability characteristic.
An exception is found for Aero Flo® 25. Judging by it having the lowest D50 and D10 compared with the other powders, we could expect it to demonstrate the lowest flowability. However, it exhibits a lower Hausner ratio than Aero Flo® 65, Aero Flo® 35 and Aero Flo® 55, which from the classical interpretation of the Hausner ratio should denote higher flowability. One explanation could be the anhydrous nature of Aero Flo® 25. Indeed, moisture inside powder leads to the setting of capillary bridges that contribute to the cohesiveness. The anhydrous properties of Aero Flo® 25, and thus its lower moisture content, seem to result in a lower cohesiveness despite the smaller particle sizes of this powder.
Sample Name | ρ(0) (g/ml) | ρ(n) (g/ml) | n½ | Hr |
Aero Flo® 60S | 0.719 | 0.830 | 8.1 | 1.15 |
Aero Flo® 85S | 0.670 | 0.793 | 18.1 | 1.18 |
Aero Flo® 25 | 0.472 | 0.645 | 31.1 | 1.35 |
Aero Flo® 65 | 0.578 | 0.807 | 34.3 | 1.40 |
Aero Flo® 35 | 0.528 | 0.769 | 37.2 | 1.46 |
Aero Flo® 55 | 0.541 | 0.790 | 34.9 | 1.46 |
Table 2: Packing properties of the six lactose powders obtained with the GranuPack.
Flowability Results
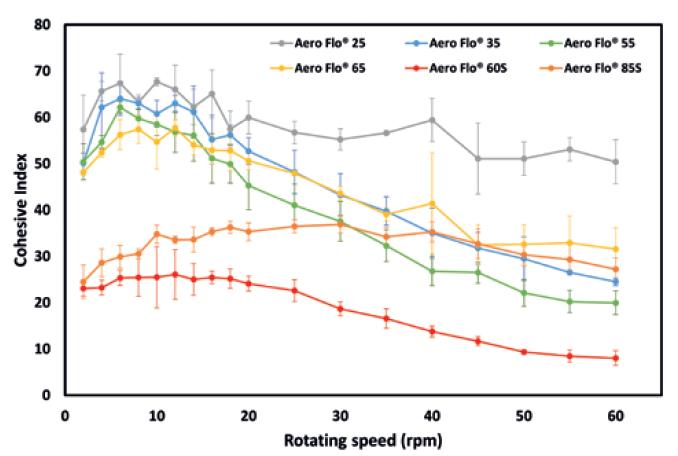
Figure 3: Dynamic cohesive index measured for angular velocities between 2rpm and 60rpm.
Figure 3 presents the cohesive index versus the drum angular velocity. At low angular velocities, the observations on powder cohesiveness made during the analysis of the packing dynamics hold true. Indeed, Aero Flo® 60S and Aero Flo® 85S clearly exhibit the lowest cohesive indices, corresponding to having the best flowability.
However, upon increasing the angular velocity, powders Aero Flo® 35, Aero Flo®55 and Aero Flo® 65 exhibit a strong shear-thinning effect, i.e. an increase of flowability with increasing applied stress. This behaviour is very interesting; it means that an increase in the processing speed will lead to an increase of flowability. In a high stress state, the flowability even becomes similar to that of Aero Flo® 85S, especially for Aero Flo® 55, which reaches a cohesive index of around 20, denoting a major drop in cohesiveness. However, Powder Aero Flo® 60S remains the least cohesive across the full range of angular velocities tested.
Contrary to the observation made with the GranuPack, powder Aero Flo® 25 exhibits higher cohesiveness and did not benefit from the shear-thinning observed with the other powders. The smaller particle sizes, especially the large number of fines, are probably the source of this cohesive behaviour.
Triboelectric Behaviour
Figure 4 presents the charge density before (q0) and after (qf) flowing through the SS316L pipes, as measured with the GranuCharge. The flow through the pipes resulted in all the powders tested building up a charge due to triboelectric effect, increasing the powder charge density. The Aero Flo® 35 exhibits the lowest charge build-up, below 1 nC/g, and thus is the least sensitive to tribocharging. Powders Aero Flo® 65, Aero Flo® 60S and Aero Flo® 25 demonstrated a moderate charge build-up and cannot be clearly differentiated from each other by their electrostatic behaviour. Finally, the Aero Flo® 85S and Aero Flo® 55 are the most sensitive to tribocharging, with a charge build-up above 2nC/g.
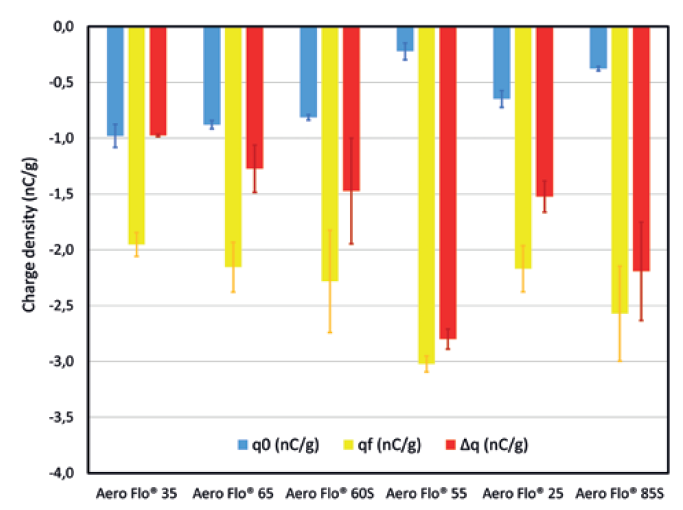
Figure 4: Charge density before and after flowing through SS316L pipes.
These results suggest that the lower the d50, the lower the sensitivity to tribocharging. This is probably due to a lower contact surface area available for tribocharging for a powder with smaller particle sizes. Higher moisture content is also expected to influence electrostatics, with the setting of a high conductivity contact network allowing efficient dissipation of charges in the material. Despite its small particle sizes, Aero Flo® 25 doesn’t exhibit the lowest charge density, which might be due to its anhydrous nature.
Moreover, the Aero Flo® 55, which exhibited the highest charge build-up, showed the lowest initial charge density. This trend is seen for the other powders and may indicate that higher chargeability is associated with a more efficient dissipation inside the material.
CONCLUSION
Six lactose powders designed for DPI applications were characterised according to their flowability, packing dynamics and tribocharging behaviour. It was observed that the powder flowability is directly linked to the particle size distribution, powders with larger particles and fewer fines exhibited a higher flowability. Moreover, a strong shear-thinning behaviour was observed, denoting a decrease of cohesiveness when the powders were in a high stress state.
Furthermore, electrostatic investigation provides useful knowledge of the tribocharging ability of the different powders. These results are of particular interest for DPI applications, in particular with respect to drug release from the lactose carrier. Based on these results, further studies should give insights into improving post-manufacturing conditioning of the excipient and/or drug formulation to help reduce the charge build-up and variability.
REFERFENCES
- Lumay G et al, “Effect of relative air humidity on the flowability of lactose powders”. J Drug Deliv Sci Technol, 2016, Vol 35, pp 207–212.
- Boschini F et al, “Linking flowability and granulometry of lactose powders”. Int J Pharm, 2015, Vol 494(1), pp 312–320.
- Lumay G et al, “Influence of mesoporous silica on powder flow and electrostatic properties on short and long term”. J Drug Deliv Sci Technol, 2019, Vol 53, Article 01192.