To Issue 136
Citation: Pedreso T, “Continuous Improvement: From Abstraction to Reality”. ONdrugDelivery, Issue 136 (Aug 2022), pp 44–48.
Tracy Pedreso discusses SHL Medical’s strategy for making continuous improvement a reality.
In various highly competitive industries where the quality of products and services is critical, the practice of using marketing ploys to double as a mask for imperfection is rampant. While something being built to perfection may seem too good to be true, much less is done to challenge such claims. As demands from consumers and regulators increase over time, challenging the notion of a company’s constant state of perfection becomes increasingly important.
For example, when a developing company undergoes an expansion journey, it may see an upgrade in its infrastructure and operational capacity, but also an increase in required manpower and operational processes. In the foreground, we think that these are all attributable to growth, but a critical analysis may prove otherwise. Over time, continuous improvement (CI) has been an emerging driver for businesses to achieve a lean manufacturing process, thereby creating value for their customers and the best-in-class products in their respective industries. Still, for many, “to improve continuously” is more commonly said than done; the pursuit of perfection or “continuous improvement” is an abstract vision that is given top-down by business leaders.
“Sustainable positive change over time is the true essence of timeless operational or business excellence.”
QUALITY INNOVATION IN A HIGHLY REGULATED INDUSTRY
In many ways, the need for constant innovation in the pharma and medtech industries is also a reflection of the need for CI in these sectors. As the demand for safe, effective and high-quality treatment modalities continues to rise, the regulatory framework that serves as the healthcare industry’s checks and balances becomes more stringent, too. Nonetheless, in the age of 21st-century medicine, it is inarguable that pharma and medtech must continue to innovate life-saving technologies and products. However, given the present regulatory underpinnings, innovation is a risky process in itself. A seemingly obvious paradox exists between the need to innovate and the responsibility to ensure quality but derisked products and services not only for the patients but throughout the value chain. How do you meet the global regulatory requirements for innovation in a highly regulated, risk-averse business such as pharma/medtech? This is where continuous improvement takes centre stage at SHL Medical.
A DEFINITION OF CI
CI is a cultural mindset of constantly looking for opportunities to improve product quality, services, processes and workplace safety. In a management context, CI means a never-ending effort to uncover and eliminate the root causes of problems or to reduce lean waste in all operational processes. Usually, it involves gradual or small-step improvements rather than a single inordinate change. For the Japanese, CI is a business culture. It involves people across all levels of an organisation, with the goal of finding and eliminating waste in materials, machineries and operational processes, as well as improving workplace organisation methods and safety.
Notably, the Japanese word “kaizen” is contextually treated as synonymous with the term CI. Kaizen comes from the Japanese characters kai, meaning “change”, and zen, meaning “good”. Taken literally, kaizen means improvement or “change for the better”. Outside Japan, kaizen has been adopted by various industries in the West and has since branched out into other distinct yet similar principles, such as just in time (JIT), the Toyota Way, Six Sigma and lean manufacturing. Although the names of these disciplines seem disparate, this article refers to CI as the archaic term encompassing the foundational concepts, methods and frameworks to constantly improve products, services or processes over time.1
CI IN THE PHARMA AND MEDTECH INDUSTRIES
In 2002, the US FDA launched the Pharmaceutical Quality for the 21st Century initiative to “encourage adoption of innovative technologies that would lead to an agile and flexible pharmaceutical manufacturing industry”. From there, the pharmaceutical sector witnessed progressions in this initiative, with a couple of guidelines being published back to back just two years later. Alongside its published guidance and reports on cGMP and process analytical technology (PAT), the FDA also released an exploratory paper on its “proposed next steps towards the desired state of pharmaceutical manufacturing”.
It could be said that such a move by the FDA in 2004 heralded the formalisation of a drive towards CI in the industry. However, this is not to say that pharma was keen to embrace the concept of CI – in practice, the rate of uptake was slow. In fact, 19 years on, although CI has already proven advantageous and exhibited prime importance in manufacturing operations across various industries, much is yet to be achieved on the medtech industry’s CI journey.2,3,4
“A successfully functioning CI programme requires leadership commitment, with lean champions to guide and empower their peers.”
AN EMERGING NEED TO COMMUNICATE CI INITIATIVES
Conducting an unfiltered Google search using the keywords “continuous improvement + autoinjector OR medical device OR drug delivery systems” would yield extremely few relevant results. Being aware that CI is also referred to as “operational excellence,” the same internet search was conducted, with similarly few results.
SHL Medical sees a need for the medtech industry to actively communicate its cognisance of practising continuous improvement. With the rise of combination products, a mutual subscription to CI by pharma and medtech would go a long way to enabling the independence of patients who rely on the treatments these industries co-develop.
Globally, regulatory bodies and the standards that they institute exist to ensure the safety and efficacy of the medicines and treatment modalities that reach the hands of patients. Utmost compliance to such is the norm but does not reflect a business organisation’s full subscription to CI in any significant way. “Operational excellence” is a common buzzword in many other manufacturing sectors but, in truth, the industry standards, knowledge and principles carried over from the past may no longer be representative of the superlatives of the present. For example, a modularised platform strategy for autoinjector development offers optimisation unseen in traditional platform strategies. SHL Medical understands that the pursuit of excellence and perfection is a never-ending journey and that sustainable positive change over time is the true essence of timeless operational or business excellence.
GLOBAL CI STRATEGY AT SHL MEDICAL
A transformative CI journey requires a transformative vision. SHL Medical’s CI strategy (Figure 1) is anchored within the following philosophies, which are aligned to its core values:
- Focus on customer: create value for customers and patients
- Drive simplicity: create lean processes
- Learn and improve: create a lean culture mindset and drive continuous improvement
- Deliver together: collaborate and work as one team to achieve a common goal with the utmost quality.
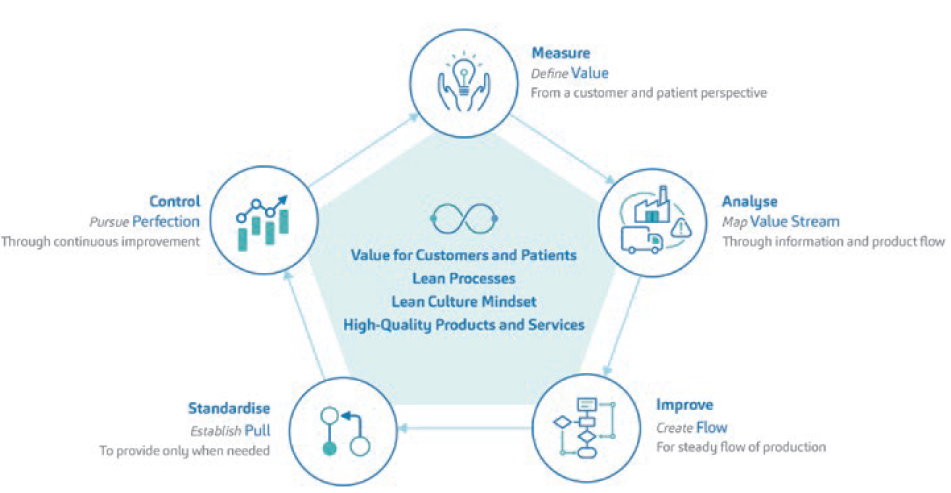
Figure 1: The CI-lean transformation approach strategy at SHL Medical.
The key to systematised CI work is moving from the idea of abstract to tangible objectives. SHL’s vision of value creation for patients and customers is entwined with values that are qualifiable and quantifiable at the same time.
When it came to creating a sustainable CI function at SHL Medical, the first step was building a foundation of lean culture across the entire organisation. The CI team was formed based on globally accepted lean principles that were tailored to SHL’s vision as a leading medtech company. The team, composed of CI engineers and lean champions representing various departments and functions, advocates for a systematised and organised approach to shape lean culture and sustain CI-building initiatives across the organisation. After all, just like the scientific method, CI programmes require empirical evidence as a basis for decision making.
A TOP-DOWN AND BOTTOM-UP APPROACH
SHL understands that CI is not a one-way street. A successfully functioning CI programme requires leadership commitment, with lean champions to guide and empower their peers. However, in spite of a firm vision from leadership, colleagues might find CI to be esoteric, acting as an adversary to their work or its principles. Given that buy-in from colleagues is a key cornerstone to making CI sustainable across an organisation, SHL has been proactive in establishing a lean mindset across its workforce instead of overloading employees with jargon. In fact, SHL’s CI team solicits ideas from manufacturing line operators, who are considered a critical source of insight into the demands of real-time production. As with maintaining equilibrium, providing the right tools and resources is key, and the active participation of colleagues in knowledge building is incentivised.
Figure 2 shows a comparison of the number of CI suggestions submitted for the first half of 2021 versus 2022, including the percentage change between the time periods. A sustainably healthy CI programme should show variance in time-based trends. That is, successful CI-building initiatives are not forced. A key factor in maintaining a healthy CI programme is the alignment of CI initiatives and programmes with departmental key performance indicators (KPIs). Embedding CI initiatives into departmental KPIs helps accelerate the cultural transformation towards having a lean mindset across an organisation. Consequently, it should be remembered that such CI activities are always bound to the idea of surpassing whatever is best in class today. This way, value for customers and their patients is constantly maximised while a positive change is created for operations, processes and the people involved. After a constant flux of CI suggestions, the time will come when it reaches a plateau – a normal phenomenon as CI programmes mature.
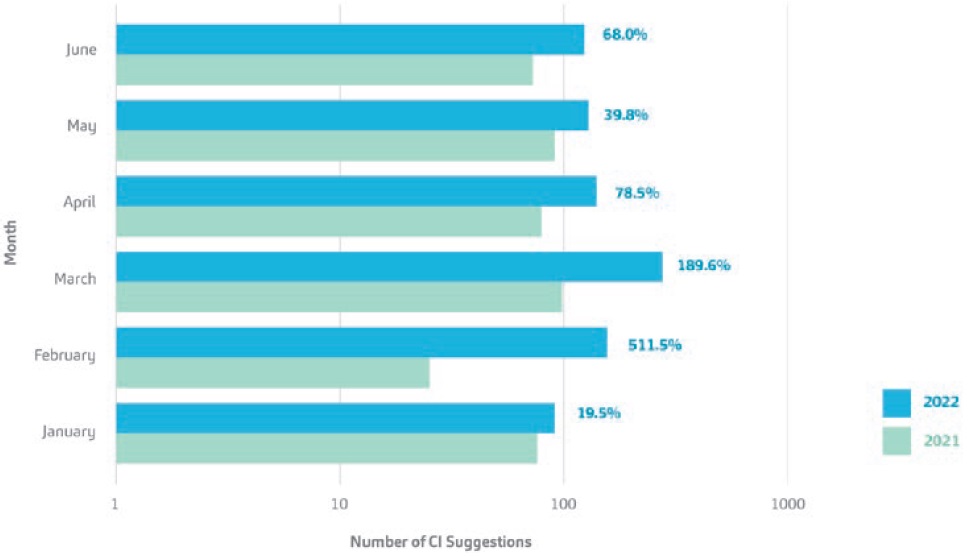
Figure 2: A comparison of the number of CI suggestions made at SHL Medical for the first half-year of 2021 and 2022.
The graph uses a logarithmic scale with the percentage change from 2021 to 2022 displayed.
“Value can be created in a way that both supports the workforce involved and maximises benefits for customers.”
CI ACROSS ALL OPERATIONS
While some may believe that CI programmes are not universally beneficial for all customer autoinjector development projects, SHL embeds CI in its operations differently. SHL’s more than two decades of infrastructure development allow the company to use platform modularity as its contemporary industrialisation approach. Platform modularisation allows the company to leverage both historical data and its communal moulding, testing and assembly machines. As such, SHL is able to implement CI programmes that continuously optimise the root processes it uses across multiple customer projects. A closer look at the focus areas for CI ideas that were submitted and implemented (Figure 3) points to the ultimate pursuit of operational excellence, encompassing both process development and manufacturing excellence.
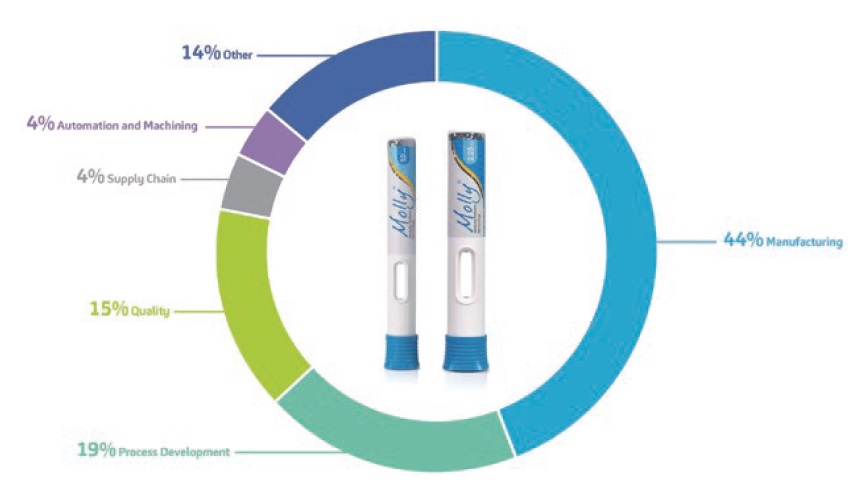
Figure 3: Percentage graph showing the top five focus areas where CI has been implemented across SHL’s operations. The goal of operational excellence is to exceed the customer’s expectations by creating lasting value and embedding top quality for all the products and services being offered.
CI IN ACTION
Value-stream mapping (VSM) is a fundamental CI-lean manufacturing method for analysing the state of the stream of events that transforms raw materials into the products that reach the customer and their patients, as well as considering how that state may be improved in future. Here, value creation should not be misconstrued as meeting the bare minimum nor the fulfilling of norms – exceeding cGMP regulations and industry standards is always a first priority for SHL.
For example, from 2020 onwards, SHL’s manual assembly machine (MAM) operations underwent a transformative journey that has not only benefited its staff but also maximised value creation for customer projects. SHL had a clear vision for redefining its manual assembly line conventions of productivity, efficiency, quality and resource maximisation, all of which are supported by real data. Clinical to commercial readiness in autoinjector development starts with a robust manual assembly process, so SHL fortified its already robust MAM operations framework to support an even shorter manufacturing lead time. To make this happen, shopfloor processes were further optimised and lean documentation procedures were practised, resulting in a continuous-flow process, as well as enabling a paperless assembly operation. During the process of lean transformation, most non-value-added activities were reduced by more than a third, further maximising SHL’s assembly line productivity and capacity. To increase organisational confidence in adherence to schedules, e-dashboards were made available across the assembly lines. These are evident of SHL’s commitment to redefining what is best in class in terms of autoinjector manufacturing.
AUTOMATION AND DIGITALISATION AS A SUBSET OF OPERATIONAL EXCELLENCE
For SHL, the fourth industrial revolution (Industry 4.0) did not mean joining the bandwagon of simply digitising and automating anything and everything. Rather, it was an opportunity to look at the bigger picture and see where the company could generate most value from creating a lean manufacturing process as the foundation for implementing digitalisation and automation in its operations. As such, in pursuit of CI and lean manufacturing, SHL also found its way into a digital transformation journey, during which it developed an end-to-end digital framework that spans all its data, products and processes. SHL’s digital transformation features an architecture where a data management and analytics system automatically creates feedback loops based on data from all product and process levels (Figure 4).
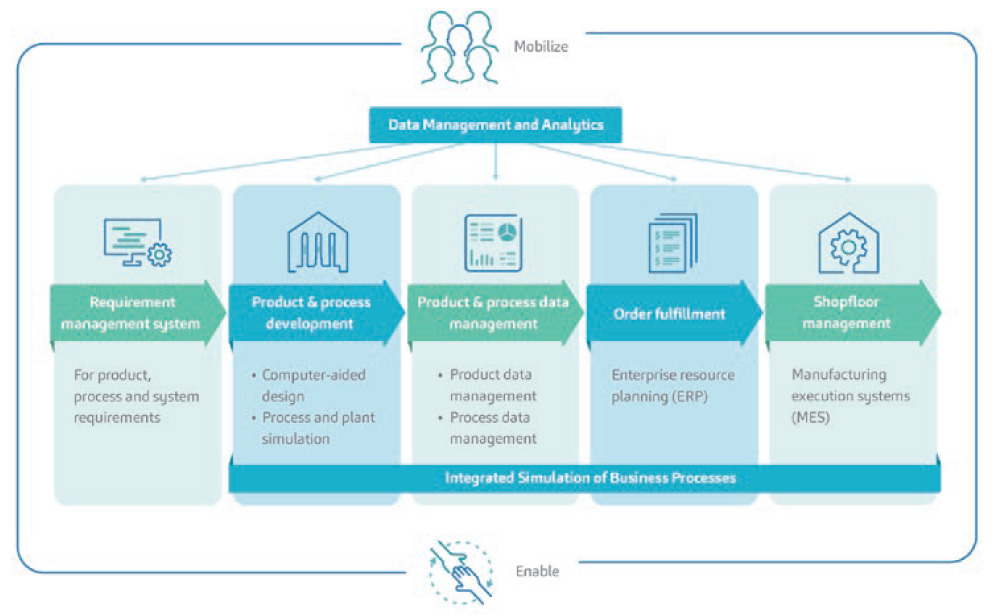
Figure 4: A condensed overview of SHL’s digitalisation programme. SHL found a way to tailor its digital transformation in a direction that pursues operational excellence.
CI HERALDS SUSTAINABLY POSITIVE CHANGE
SHL understands that sustainability and positive change across operations can be attained through the consistent, committed and systematic participation of people across the value chain. It has shown that CI is more than an abstraction, and that value can be created in a way that both supports the workforce and maximises benefits for customers. In an industry where the safe and effective delivery of drugs and treatment modalities to patients is of prime importance, SHL believes in a future built upon present action towards CI.
REFERENCES
- “Continuous Improvement”. Encyclopedia.com web page, accessed Jul 2022.
- Yu L et al, “FDA’s new pharmaceutical quality initiative: Knowledge-aided assessment & structured applications”. Int J Pharm X, 2019, Vol 1, Article 100010.
- “Pharmaceutical cGMPs for the 21st century – a risk-based approach”. US FDA Report, Sep 2004.
- “Guidance for Industry: PAT — A Framework for Innovative Pharmaceutical Development, Manufacturing, and Quality Assurance”. US FDA, Oct 2004.