Citation: Keinicke Hansen L, “Delivering Intelligent Autoinjector Assembly Solutions for Complex Customer-Specific Requirements”. ONdrugDelivery, Issue 163 (Jul 2024), pp 54–57.
Lars Keinicke Hansen discusses the potential of technology to enhance the efficiency and productivity of manufacturing processes for both pharmaceutical companies and CDMOs, as well as the skills and expertise required to maximise the potential gains technology can offer.
While many have come to take them for granted, mobile phones still serve as a remarkable reminder of the pace of change that technology can make possible. The success of the mobile phone in the modern world can be attributed to many things, but one of the most crucial factors has been its flexibility. By downloading an app or software update, it is possible to add entirely new functionality without any major investment or alteration to the underlying hardware. Tasks that previously would have required a separate computer, camera, scanner or satellite navigation device can now all be achieved by a single palm-sized device.
Parallels can be drawn with pharmaceutical production environments, which are also becoming increasingly defined by convergence, integration and adaptability to match the accelerated pace of change. Previously, assembly lines were comparatively fixed, with adjustment or amendment requiring a major investment in time, equipment or skills.
“A top-line measure of parts per minute is only part of an equation that must also prioritise increased production efficiency and uptime, lower reject rates and the ability for systems to accommodate changes with minimal requirement for ongoing re-engineering.”
However, times have changed. Today, there is an increased requirement to adapt and adjust production capability at speed to meet changing demands, whether that takes the form of scaling up from benchtop volumes to full commercial production, recalibrating lines according to different device types or satisfying the call for shorter-run production of devices for personalised medicines. A top-line measure of parts per minute is only part of an equation that must also prioritise increased production efficiency and uptime, lower reject rates and the ability for systems to accommodate changes with minimal requirement for ongoing re-engineering.
Furthermore, this must all be achieved in light of potentially destabilising macroeconomic influences. In such a competitive landscape, this means innovating to answer shifting patient expectations and needs; managing supply-chain resilience in the face of geopolitical unrest; and fulfilling environmental responsibilities through more sustainable use of materials and energy.
UNDERSTANDING CUSTOMER-SPECIFIC REQUIREMENTS
From an equipment specification point of view, this market context eliminates a one-size-fits-all, plug-and-play model in favour of a fully customised approach to ensure that products, processes and supporting services are all aligned towards maximising production efficiency for the given application. However, bespoke, customised solutions are dependent on suppliers having a clear and deep understanding of the customer and their specific requirements.
This is especially the case with assembly lines for autoinjector devices. Here, there is a universal focus on meeting tight tolerances, challenging geometries and rigorous in-process quality controls. For example, force and distance are critical attributes when handling plunger rods that might need to be positioned precisely in conjunction with a spring-loaded support pin. However, the journey to the point of production is likely to look different for contract development and manufacturing organisations (CDMOs) compared with pharmaceutical original equipment manufacturers (OEMs).
The CDMO Perspective
For CDMOs, there is an obvious competitive advantage in being able to support a range of pharmaceutical clients in the assembly of multiple different types of generic autoinjector platforms from various suppliers. Commercial success depends on creating flexible foundations that achieve this objective without significant, continuous capital expenditure on multiple assembly lines, while maintaining operational productivity at consistently high levels and ensuring that products meet critical quality thresholds reliably.
“Stevanato Group’s assembly lines meet this goal through modular design, with their overall functionality delivered via integrated units that are configured to handle various aspects, ranging from in-feed and orientation to laser engraving, labelling and in-line inspection.”
In cases where the same lines manage the assembly of different generic devices, maximising uptime and limiting the time lost to format and batch changeovers become critical objectives for increasing overall productivity and efficiency, getting the most possible out of available resources and saving cost. Stevanato Group’s assembly lines meet this goal through modular design (Figure 1), with their overall functionality delivered via integrated units that are configured to handle various aspects, ranging from in-feed and orientation to laser engraving, labelling and in-line inspection.
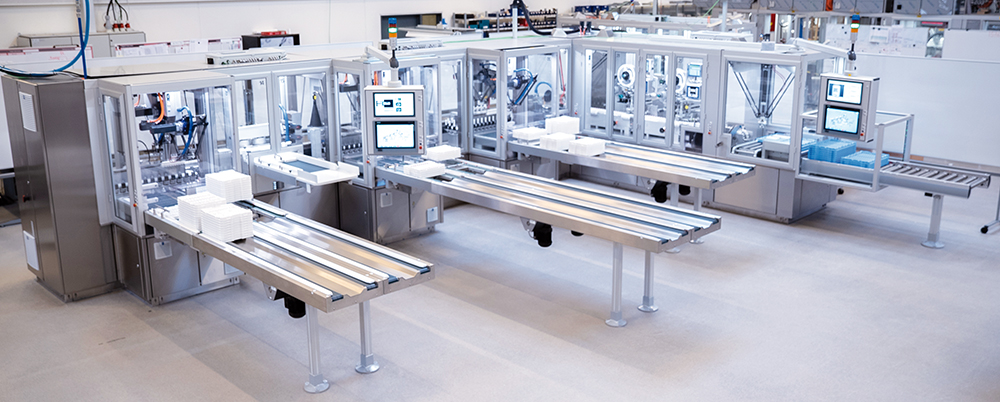
Figure 1: Modular assembly equipment for flexible and scalable solutions.
Within this structure, process modules can be pre-configured for different autoinjector platforms, while preconfigured recipes containing the relevant production parameters can be stored in the assembly line’s control systems in advance. Then, at the point of changeover, the new recipe is selected and the system automatically adjusts to the incoming autoinjector format. With speed in mind, the changeover process is also tool-free. Quick-release and snap-on mechanisms make it simple for key parts, such as grippers and movers, to be exchanged easily. The changeover process is further augmented by the integration of radio-frequency identification (RFID) and sensor systems to verify the accuracy of part placement and ensure that the set-up adheres to the criteria for the specific device being assembled.
The advanced nature of the technology employed in such a system underlines how it is incumbent on suppliers of assembly equipment to deliver not just hardware or software in isolation, but also to contribute value-added tailored wrap-around support. Doing so can ensure that efficient, high-volume manufacture can be deployed to the maximum possible effect. As such, equipment manufacturers should actively and closely support their CDMO customers to help them capitalise on the potential of assembling multiple types of autoinjector on a single, flexible line – a task that is made easier if those manufacturers, such as Stevanato Group, also have extensive knowledge of the end-to-end device production cycle.
The Pharmaceutical Perspective
On the other hand, in the case of pharmaceutical OEMs, although no less support is required, the relationship dynamic is notably different from that with CDMOs, as the focus is not typically on the assembly of multiple types of autoinjectors on the same line. Instead, the challenge is more likely to relate to the optimisation of producing a particular device at high volume and high quality.
To meet this challenge, Stevanato Group adopts design for manufacture principles when establishing assembly and packaging lines for pharmaceutical OEMs. This well-recognised approach means that processes are optimised in a way that allows products to be developed and assembled at volume in the most cost-effective way. Flexibility remains a key feature, of course, with consideration given to the likely future evolution of the device and its assembly requirements. This potential is embedded in the customer journey, with transparent technology transfer from prototyping and benchtop assembly through to a GMP-compliant pilot line and fully automated commercial production.
DIGITAL TWIN TECHNOLOGY
A valuable way of bringing design and manufacture closer together throughout this journey is the use of digital twin technology (Figure 2). A digital twin is a virtual 3D copy of a physical assembly line, with algorithms and artificial intelligence employed to simulate the reality of production as closely as possible. By providing such an accurate replica of the real-world set-up, a digital twin can provide many cost- and time-effective advantages to the design, development and ongoing optimisation of assembly lines.
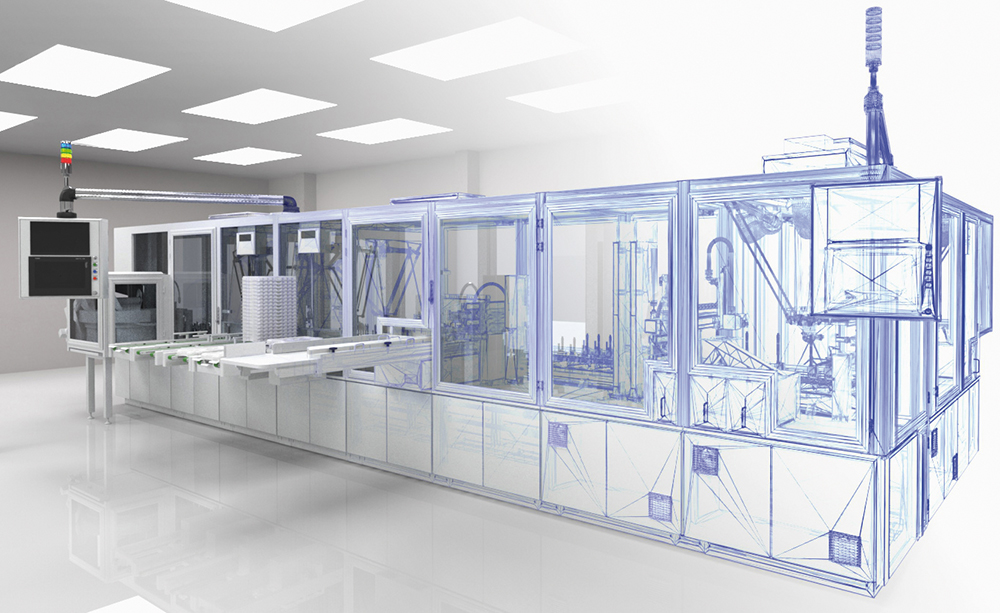
Figure 2: Stevanato Group’s digital twin is a digital replica of a physical entity. Applied to assembly equipment, it allows process optimisation in the design phase.
From a skills perspective, operators and technicians can engage with a digital twin to familiarise themselves with the equipment prior to it being fully commissioned. In addition, any proposed alterations and updates to the system can be simulated on the digital twin to verify their benefit to performance or to highlight any issues or potential friction points, such as the interface between hardware and software. If an issue is detected, the ability to debug and problem-solve in a virtual environment can smooth and accelerate the process of running-in new system elements, helping avoid the bottlenecks and time losses this often creates in live production environments.
“By creating a powerful visualisation of the assembly line, the digital twin can be a valuable tool for change-management.”
At a broader level, by providing a powerful visualisation of the assembly line, the digital twin can be a valuable tool for change-management. It gives a company – whether a CDMO or pharmaceutical OEM – a unique view of the assembly line as it will be, allowing for virtual adjustments to be made and tested before they are replicated in real life. This capability reduces the likelihood of more significant and costly re-engineering being needed at a later point.
DIAGNOSTIC AND PERFORMANCE DATA
When the physical assembly and packaging line is fully operational in the real world, the use of data continues to be a key focus. By capturing and analysing operational data on the fly, a live picture of the line’s performance can be painted in real time. Historically, this capture and analysis process would have to be undertaken after the machinery has been stopped, which can result in delays while also increasing the risk that important issues are not even flagged until they have escalated into disruptive problems. However, by collecting data in real time, operatives can furnish data analysts with rich information that allows them to spot issues as they arise, opening the door to potential remedial interventions or pre-emptive measures that are designed to tackle the issue before it becomes too problematic.
In this situation, data are intended to augment rather than replace the expertise of operational and technical staff. The data provide otherwise invisible intelligence that can inform judgements, challenge assumptions and avert the need to rely on instinct alone. This underlines the critical importance of balancing technical capability with human insight in any production environment.
Stevanato Group acknowledges that, while the equipment within its assembly and packaging line portfolio delivers all the required functionality for flexible, scalable manufacture of autoinjector devices, arguably, the most valuable aspect of its offering is the intelligence of its team. The company’s experts offer both extensive technical knowledge and the emotional intelligence to understand the unique demands of each customer, enabling the team to support them with customised assembly solutions and value added services that meet their particular evolving needs.
CONCLUSION
In a world that is only becoming more complex, technology plays a vital role in enabling people to do so much more than they could before – just look at how mobile phones now allow people to do everything from making payments to managing their money and monitoring their health. Likewise, in pharmaceutical manufacturing, technology now enables companies to manage the assembly of incredibly complex devices with more efficiency and flexibility than ever before. However, it is only by having the skills to harness and apply that technology that companies will be able to effectively answer the demands of a continually changing market in the years to come.