To Issue 132
Citation: Moulinié P, Platte I, Zetts L, “Designing Drug Delivery Devices to Meet Emerging Needs and Sustainability Goals”. ONdrugDelivery, Issue 132 (Apr-May 2022), pp 24–28.
Pierre Moulinié, Isaac Platte and Lauren Zetts discuss how polycarbonate-based materials deliver value to emerging drug delivery devices.
“Future drug delivery devices will not only be the target of innovation for increased technology and functionality but also for easier recovery and reuse of their materials.”
Innovation in autoinjector and pen injector platforms is increasingly oriented towards meeting sustainability-related requirements. The growing demand for materials with lower carbon footprints and the reduction of healthcare waste are among the drivers prompting designers to re-open the material choices for medical devices.
Polycarbonate, which offers an outstanding combination of engineering properties and high versatility for drug delivery devices, is available in various formulations that can help simplify designs for disassembly and sorting of reclaimed waste. With medical-grade polycarbonate availability in climate-neutral versions, drug delivery devices based on components made from polycarbonate can not only help with certain waste-related challenges but can also help the industry meet lower carbon dioxide footprint targets.
INNOVATIVE MATERIALS FOR NEXT-GENERATION DRUG DELIVERY DEVICES
The Trends
Drug delivery devices, such as inhalers, pens or autoinjectors, have seen strong growth over recent years. This growth is expected to continue, as they provide excellent solutions for both patients and healthcare providers for a variety of health issues. However, increased attention to end-of-life device disposal has opened up a debate on the materials selected. Where previously materials were chosen on the basis of the components’ function and productivity, there is now a strong focus on eliminating waste within the next decade, which has caused companies in all industries, including healthcare, to reconsider design and material choices to facilitate recovery, reuse and lower the carbon footprint.
As a result of this new emphasis on lifecycle, materials that were once simply “good enough” now require better durability to withstand the added demands of a material’s next application, while still providing functionality to lifesaving devices. Increased recycled content is well established in packaging and, in the past few years, emphasis has turned to drug delivery devices and their recovery, with a view to avoiding landfill or incineration through the reuse of the materials. Healthcare and pharmaceutical companies are among many that have mandated targets, such as zero-waste or climate-neutral operations, as part of their environmental, societal and governance goals. Hence, future drug delivery devices will not only be the target of innovation for increased technology and functionality but also for easier recovery and reuse of their materials.
With these emerging requirements in mind, and to make the designing of future devices easier, Covestro has expanded its portfolio of medical-grade polycarbonate materials. Like medical-grade Makrolon polycarbonate, these newly introduced products satisfy many elements for ISO 10993 biocompatibility and are available globally in customisable colours. In some cases, additional requirements (such as USP <661.1> or USP Class VI) are also met.
How Polycarbonate Materials Meet Technical Requirements
Polycarbonate is already well known as a material of choice for medical devices because of its outstanding combination of physical properties and amenability to high productivity with complex designs. To illustrate material innovations and benefits, Covestro developed a prototype (Figure 1) to demonstrate how newly developed, innovative materials function together and, ultimately, how a polycarbonate-based device can become more sustainable.
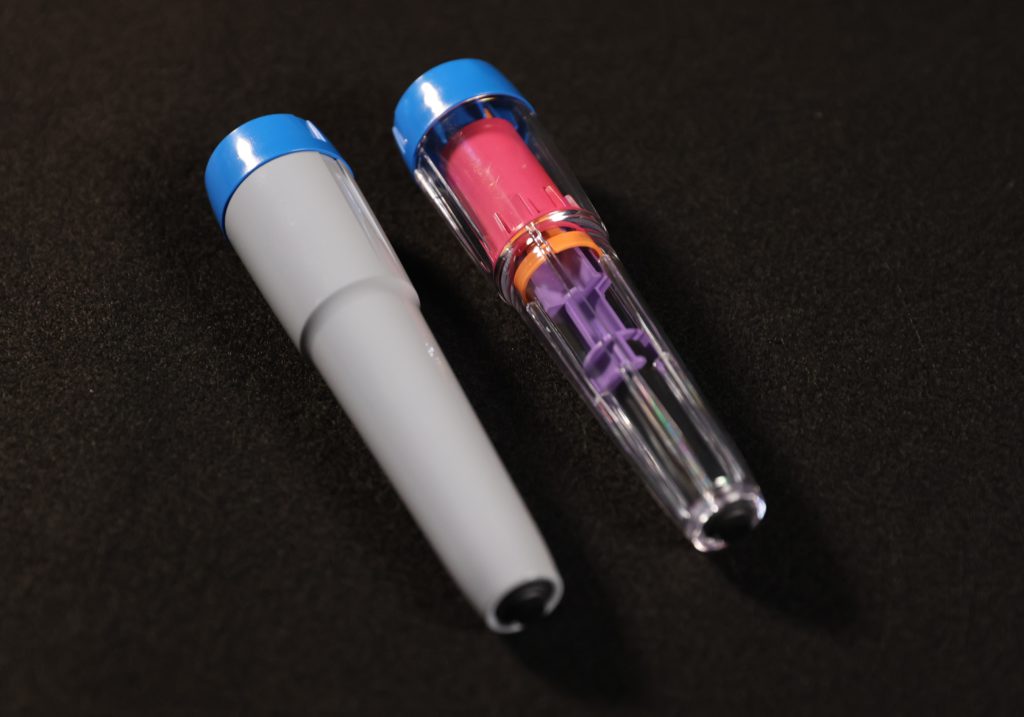
Figure 1: Drug delivery device prototypes with all-polycarbonate components.
“Plastics under long-term stress undergo creep, which is a permanent deformation related to their viscoelastic response to pressures.”
In many cases, these new polycarbonate-based materials have higher performance than more commonly used incumbent materials and can increase the capabilities of autoinjectors or pens. For example, parts that are under constant stress often require higher rigidity, creep-resistant materials, as provided by glass-reinforced plastics. Polycarbonate-based materials with superior mechanical performance are well suited for devices that deliver more viscous drugs, which may need higher forces and more creep resistance. Moreover, internal mechanisms with parts that slide together are made with low-friction materials to ensure consistent and smooth function. These materials are amenable to sterilisation methods not possible with many fluorinated plastics. In addition to illustrating the technical benefits of polycarbonate-based materials, the prototype in Figure 1 will also be discussed to highlight sustainability-related advantages.
Medical-Grade Polycarbonate-Improved Creep Resistance
Plastics under long-term stress undergo creep, which is a permanent deformation related to their viscoelastic response to pressures. This is particularly relevant for autoinjectors that contain spring-loaded mechanisms that remain ready to use for several years during the device’s shelf life. In this case, a plastic remains under pressure and is subject to a slow deformation over this period. Creep resistance of glass-reinforced materials is known to be superior to unreinforced plastics, and such materials are often chosen for applications experiencing higher mechanical loads. Figure 2 compares the creep behaviour of several materials, including newly introduced medical-grade glass-reinforced Makrolon polycarbonates, ranging from 10% to 30% reinforcement.
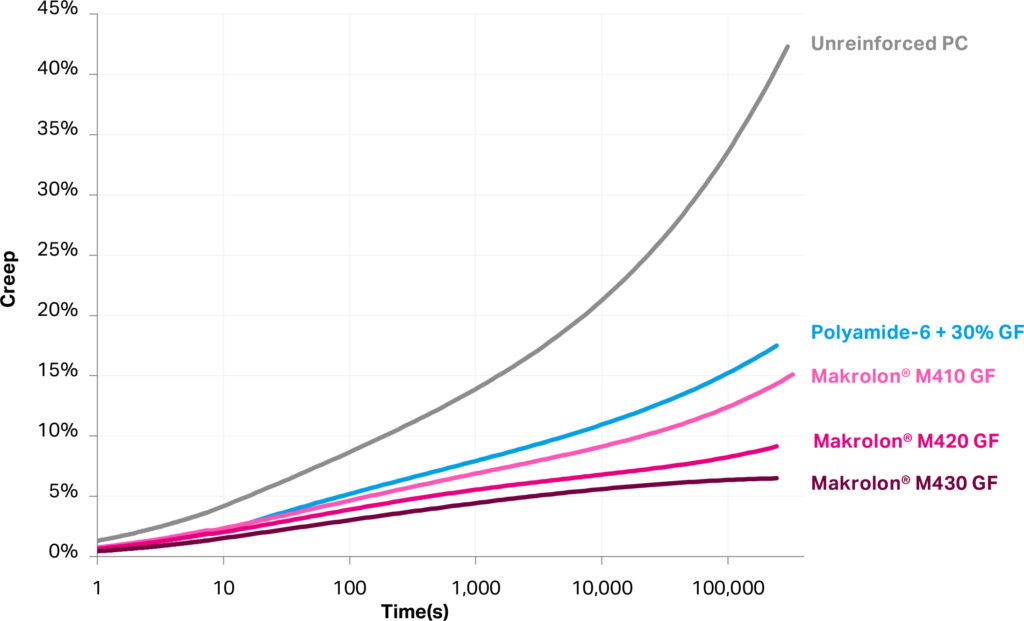
Figure 2: Tensile creep at 30 MPa stress shows low-creep medical-grade glass-filled Makrolon.
Higher glass reinforcement generally improves creep resistance and, in all cases, reinforced resins offer superior performance to unreinforced plastics. Glass-filled (GF) polyamide, a commonly chosen material for reinforced plastics, may offer high rigidity but suffers from more significant creep compared with polycarbonate. Furthermore, polyamides are also well known for high absorbance of ambient moisture and for properties that change with humidity (e.g. modulus and dimensions). As with low-friction polycarbonate, GF polycarbonate is part of innovative designs that are oriented to easier recovery and reuse of materials.
“Low-friction polycarbonate can be an excellent choice in autoinjectors to improve the consistency of deployment forces.”
Medical-Grade Low-Friction Polycarbonate
Achieving low-friction surfaces has traditionally been achieved with materials such as polytetrafluoroethylene or polyoxymethylene. Recent innovations in materials and processing have enabled the introduction of medical-grade low-friction Makrolon, where a coefficient of friction (COF) that is competitive with traditional low-friction materials has been observed.1 Furthermore, low-COF polycarbonate materials have also shown significantly decreased mould-ejection forces to help increase manufacturing productivity.2
Low-friction polycarbonate can be an excellent choice in autoinjectors to improve the consistency of deployment forces. Figure 3 illustrates the button-release force measured on the Covestro prototype devices (Figure 1) with polycarbonate-based components. Low-friction Makrolon in Figure 3 shows reduced force in activation of the prototype, as well as improved consistency in the force required. Makrolon polycarbonate-based solutions for low friction in medical applications offer higher versatility in terms of sterilisability (e.g. by radiation) and overall stability. Low-friction Makrolon also offers a solution for new designs oriented to recovery and reuse of materials and reduced waste.
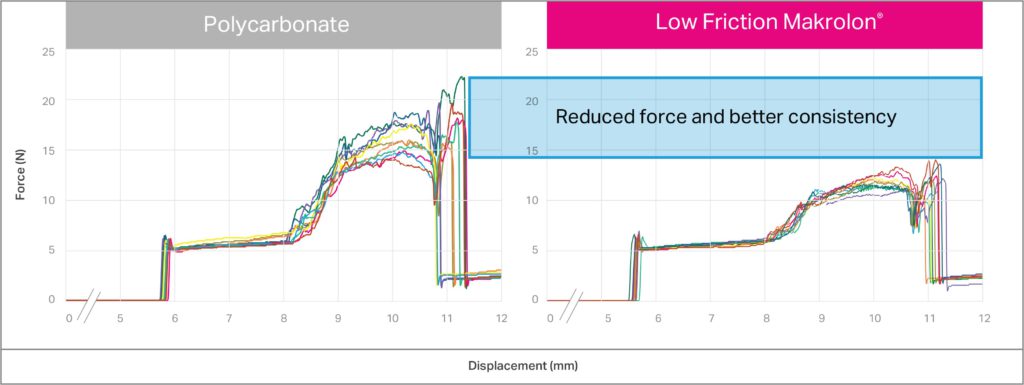
Figure 3: Forces versus displacement for button fire with polycarbonate (left) and medical-grade low-friction Makrolon (right).
PC/ABS and PC+ Polyesters for Medical Applications
Polycarbonate blends – for example, polycarbonate/acrylonitrile butadiene styrene (PC/ABS) – have been materials of choice for electrical and electronic equipment for decades, as they provide the right balance of performance and productivity. As such, medical-grade Bayblend PC/ABS has also been an important solution for drug delivery devices. As these devices become connected and require power sources, medical grades with various Underwriters Laboratories certifications for flame retardancy are expected to become popular choices. Higher-performance medical-grade Makroblend PC+ polyesters have also been solutions for applications with higher requirements, such as wearables that need better resistance to skin lotions.
The portfolio of blends for housings continues to be expanded with new flame-retardant polycarbonates designed for superior resistance to disinfectants or sterilisation methods, as new cleaners or sterilisation methods (such as UVC) are introduced.3,4
MAKING DRUG DELIVERY DEVICES MORE SUSTAINABLE
Climate-Neutral Materials
Previous work has shown that polycarbonates’ combination of properties, especially rigidity and high heat resistance, can be leveraged to increase productivity and even lower electricity consumption during the injection-moulding process.5,6 In addition to this important value proposition, recent developments in the processes used to make basic chemical building blocks have facilitated the replacement of traditional petrochemical feedstocks with renewably sourced raw materials. Production of engineering thermoplastics via non-petrochemical raw materials has paved the way to the manufacture of resins, like polycarbonate, with a lower carbon dioxide footprint.
The concept of mass-balance allocation further recognises the benefits of substituting fossil-based chemicals over a specified period of time and has become an established method to account for decreased carbon dioxide emissions during the production of polymers.7 Covestro’s recent introduction of climate-neutral polycarbonate, an industry first announced in 2021, relies on combining the benefits of mass balance with further advantages offered by operations relying on electric power from renewable sources.8
Enabling Unsorted Mixtures and Closed Loops
Drug delivery devices today are made of a variety of plastics. With plastics’ widely differing chemistries, recycling and recovery of materials becomes challenging through the lens of today’s sustainability goals, particularly in cases where incompatible materials may very likely become mixed together and, therefore, not recyclable. With the device prototype shown in Figure 1, various functional materials are brought together into a device capable of delivering consistent performance in an attractive design using materials that avoid complicated choices when planning for recycling.9 While there are alternative plastics to polycarbonate that may offer similar functionality, the value proposition of using polycarbonate-based materials for all components is not just limited to expanded possibilities offered by the elimination of constraints (e.g. GF polyamide and humidity effects described previously).
In this section, we discuss how using all-polycarbonate components can significantly simplify material sorting after disassembly by offering a solution for “unsorted” scenarios. In the more realistic unsorted scenario, all plastic materials from a drug delivery device are mechanically mixed and remoulded. Regardless of whether manufacturers consider so-called closed-loop recycling (i.e. recovering one’s own products and using them to make new ones) or open-loop recycling (i.e. recovering one’s own products and using them to make something else), a significant challenge is to avoid inadvertent mixing of incompatible plastics. Figure 4 illustrates the replacement of traditional plastics with polycarbonate-based materials that can serve the same functionality.
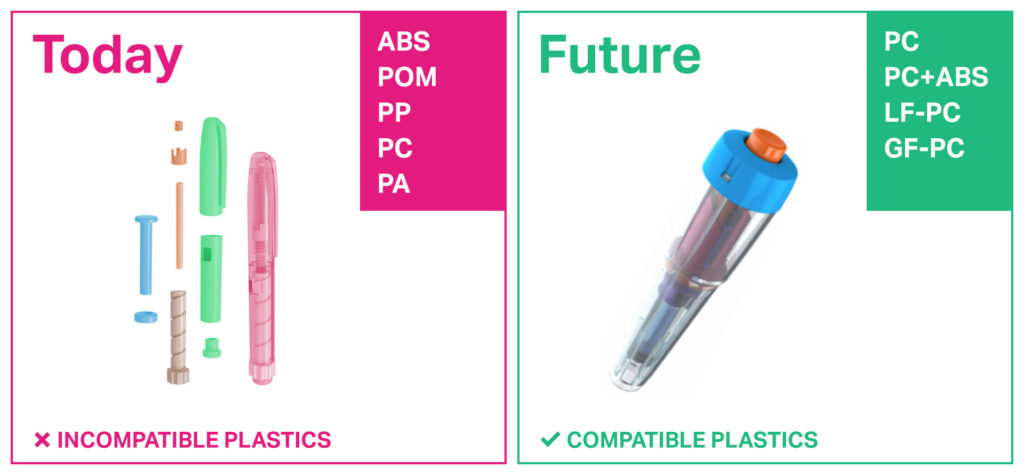
Figure 4: Simplified sorting with all-polycarbonate components in drug delivery devices.
Covestro set out to investigate the effect of cross mixing the materials from the different components in the prototype. Through simple experiments, the company studied the physical properties obtained when polycarbonate (50%), low-friction polycarbonate (20%), GF polycarbonate (10%) and PC/ABS (20%) were mixed to simulate an instance where unsorted plastics from the prototype in Figure 1 are recycled. To further simulate closed-loop manufacturing, a 100% regrind study was carried out, where the mixed material was subsequently reground, remoulded into standard test specimens (i.e. American Society for Testing and Materials D638 tensile bars and D256 impact bars) and then tested. A total of nine test/regrind/remould loops were completed.
An important advantage offered by designing a device with a uniform material suite (in this case all-polycarbonate materials) is the inherent compatibility of each material from a chemistry perspective. This can offer significantly easier paths to the reuse of the plastics after recovery and disassembly of the device. Many other materials require significant measures and efforts to avoid cross-contamination to avoid auto-catalytic – hazard generating – degradation reactions.10 Figure 5 summarises important physical properties from the unsorted/mixed material. As shown, the all-polycarbonate mixture provided consistent properties, owing to the inherent compatibility of all the materials.
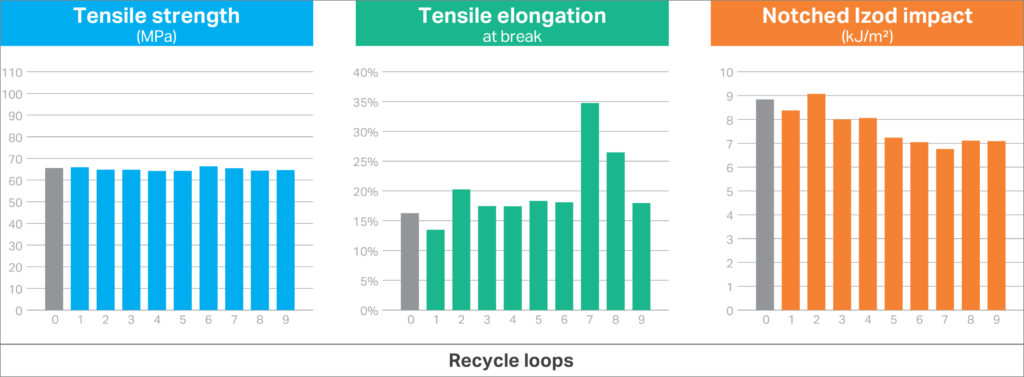
Figure 5: Physical properties of unsorted polycarbonate-based materials after multiple 100% regrind recycle loops.
For many designs, tensile properties and impact strength are the principal choice drivers to ensure the plastic can perform for the intended application. The tensile properties and impact strength for the mixed materials showed excellent consistency across the regrind cycles and were better than those typically observed for polycarbonate blends with 10% glass-fibre reinforcement. This simple experiment suggests that simply mixing all-polycarbonate components from a recovered drug delivery device could still deliver consistent properties for other applications.
CONCLUSION
Innovative polycarbonate-based materials can replace traditional materials in drug delivery devices. Working together in a drug delivery device, Makrolon, Bayblend and Makroblend products can not only help to solve certain waste-related challenges but also help the industry meet lower carbon dioxide footprint targets, all while providing functionality to lifesaving medical devices.
REFERENCES
- “Introducing a new portfolio of low friction polycarbonates”. Covestro Website, Accessed Mar 2022.
- Unpublished work, Covestro; results available upon request.
- “Covestro Polycarbonates Compatibility with Disinfectants Used Against SARS-CoV-2”. Covestro, Jun 2020.
- “Influence of UVC LED disinfection on polycarbonate materials”. Covestro, Feb 2021.
- Vink D, “LSR shows great versatility at K 2019 show”. Plastics News, Nov 20, 2019.
- Menego I, Yeager M, Moulinie P, “Material Properties and Their Influence on Moulding Productivity and Efficiency of Medical Resins”. Proc Ann Technic Conf Soc Plastics Engineers (ANTEC 2013), April 21–25, 2013, Cincinnati, OH, US.
- “ISCC for the Circular Economy and Bioeconomy”. ISCC, Accessed Mar 2022.
- “Covestro Debuts Climate-Neutral Polycarbonate at Chinaplas”. Plastics Today, Apr 14, 2021.
- “Environmental Design Considerations for ICT & CE Products”. ECMA-341, 2010, pp 31–32.
- Giles HF et al, “Extrusion, The Definitive Processing Guide and Handbook”. Elsevier, 2014, pp 124–125.
Previous article
HOW CAN THE PHARMA INDUSTRY PREPARE FOR NEW pMDI PROPELLANTS?Next article
SMART SOLUTIONS TO REDUCE CARBON FOOTPRINT