To Issue 156
Citation: “Interview with Alexandre Fontayne, Unither Pharmaceuticals”. ONdrugDelivery, Issue 156 (Jan 2024), pp 30–32.
“We see EuroJect® as a potential replacement for traditional multidose glass vials – it’s ready to use with minimal preparation, reducing the risk of errors during delivery and cross-contamination.”
Q To begin with, can you explain how the EuroJect® device leverages blow-fill-seal technology and what makes it an innovative solution for single-dose injection of therapeutics?
A Unither has extensive experience in blow-fill-seal (BFS) technology. In fact, as a world leader in this aseptic and fully automatic technology, we celebrated our 30th anniversary in 2023, so we were ideally positioned to apply BFS to EuroJect’s design. The device combines a BFS ampoule with a connector and needle, and can be adapted for various injection types, including intramuscular, subcutaneous and intradermal, by attaching different cannulas. It’s a single-use system, where you detach the dose, open it, screw on the connector and it’s ready for injection (Figure 1).
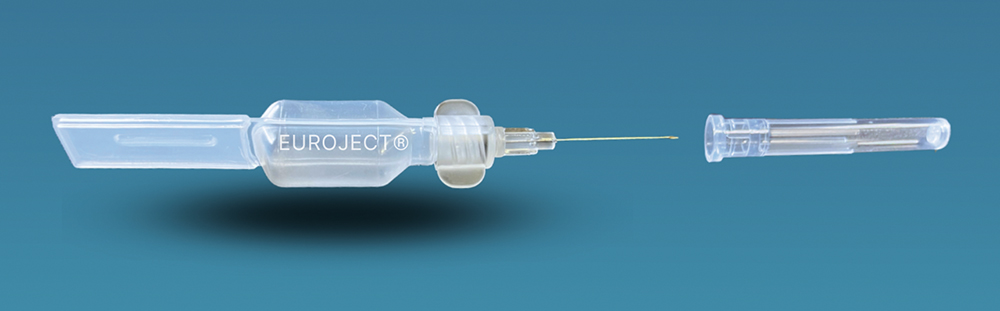
Figure 1: EuroJect® – Unither’s novel injection device made using BFS technology.
We see EuroJect® as a potential replacement for traditional multidose glass vials – it’s ready to use with minimal preparation, reducing the risk of errors during delivery and cross-contamination. Compared with prefilled syringes, EuroJect® has a much simpler mono-material design, using only low-density polyethylene Interview (LDPE), a well-characterised and accepted material for primary containers, including for biologics. The BFS process (Figure 2) is fully automated, minimising the risk of contamination during filling compared with multidose glass vials or prefilled syringes. The device is lightweight, unbreakable and there’s essentially no risk of raw material shortage, unlike with glass vials or prefilled syringes.
Additionally, BFS is recognised by regulators as an alternative primary container process for injectables.
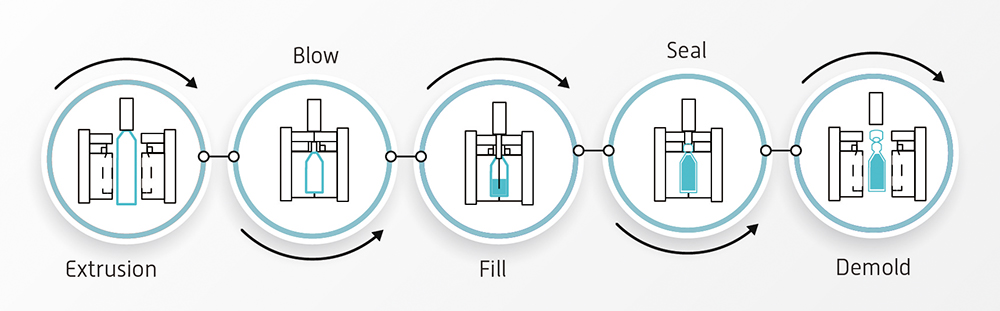
Figure 2: The BFS process.
Q Could you provide more details on the production scale and cost effectiveness of solutions for vaccines and biologics?
A The BFS process is fully automated, not requiring any manual input (Figure 3). We feed LDPE pellets into the production machine and the product is manufactured automatically in an aseptic environment. In terms of scale, we can produce about 200 million doses a year on a single machine, which is a significantly higher capacity than we see with glass vials or prefilled syringes.
We are currently building a new workshop in our facility in Amiens (France), with five lines in a BSL-2 environment – a capacity of a billion doses per year – with the first line to be installed by the end of 2024 and qualify for GMP production by the beginning of 2025 (Figure 4). The equipment we use is all standardised. The core of the system is a machine from Rommelag (Sulzbach-Laufen, Germany), which is equipped with various options to maintain the product and system temperature, ensuring that it is compatible with biologics.
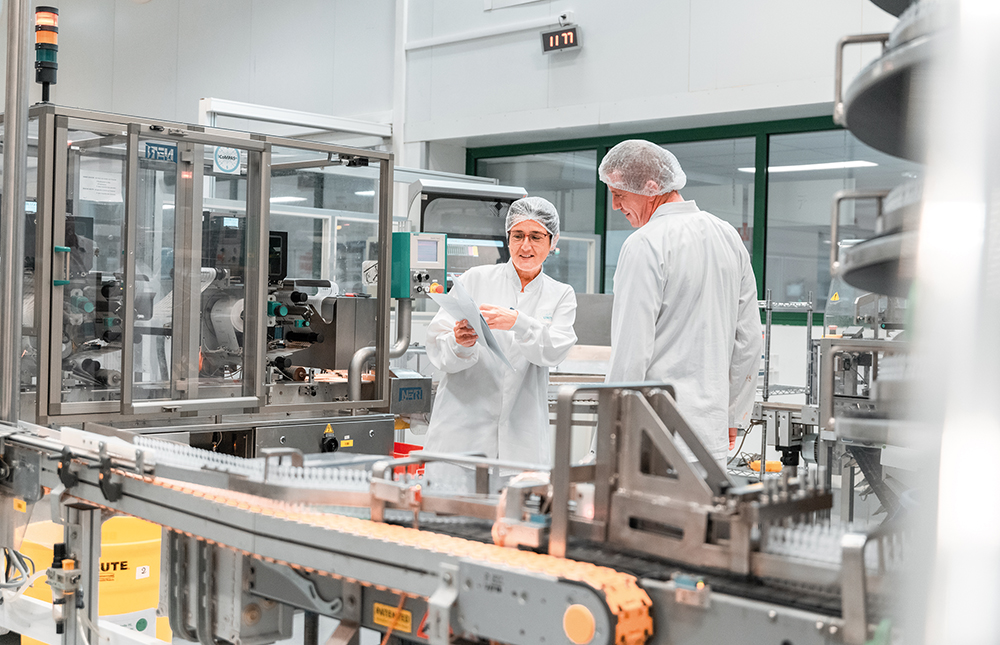
Figure 3: Fully automated BFS production at Unither’s Amiens facility.
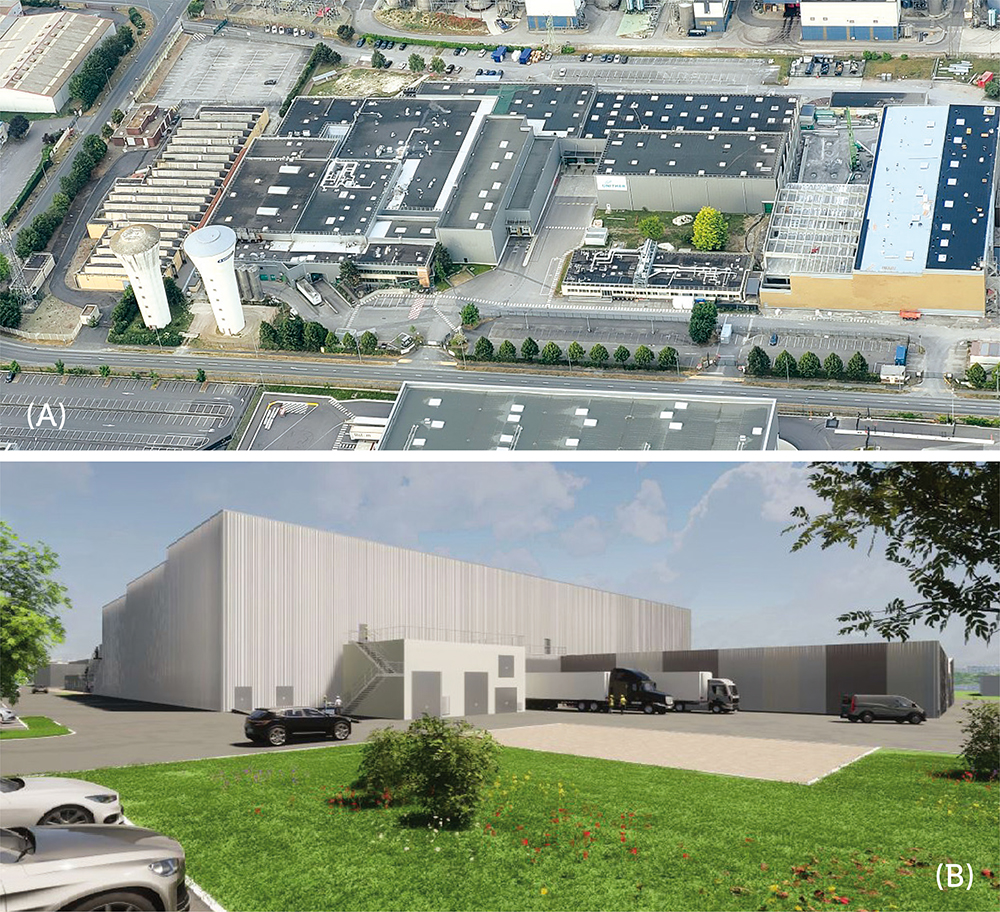
Figure 4: Unither’s (A) present and (B) future facilities in Amiens, France.
In terms of size and weight, Euroject® is generally smaller and lighter compared with traditional primary containers, giving it a smaller logistical footprint, therefore making it cheaper to transport. Coupling that with the fill/finish being comparable to glass vials, we firmly believe that EuroJect® is well positioned to be competitive in the market, and is particularly suited to low- and middle-income countries. EuroJect® has all the advantages of prefilled solutions, but the price point of a multidose vial.
We also have an advantage in dosing accuracy compared with multidose vials. As our doses are prefilled, there’s no risk of administering a lower or higher dose. Unlike multidose glass vials, where unused doses might be discarded, the EuroJect® system ensures that no dose is wasted.
Q Let’s talk about ease of use – is EuroJect® easier for healthcare professionals to use compared with traditional syringe-based injection methods?
A We conducted a study concerning this with healthcare professionals in January 2023. We gave healthcare professionals in the UK the opportunity to try EuroJect® and most of them approved of it, saying that they found it easy to prepare and use. They had no difficulty attaching the connector and found it straightforward for all types of injection.
Even those who were initially unconvinced became more comfortable with the device after a few uses. This wasn’t unexpected because EuroJect® changes the traditional way of injecting – instead of pushing a plunger, users gently squeeze the flexible primary container to deliver the dose. While the injection method is different, requiring some practice perhaps, it’s straightforward. For example, the angle of injection is more vertical than horizontal, as for classical intramuscular injections, but the end result is completely equivalent. Overall, we found the response very convincing and it suggests that EuroJect® will receive a positive reception amongst healthcare providers.
“It’s applicable for vaccines, monoclonal antibodies, coagulation factors, insulin and GLP-1 agonists.”
Q Could you elaborate on the main therapeutic applications you’re targeting with EuroJect®?
A EuroJect® is primarily targeted towards biologics, with routes of administration including intramuscular, intradermal and subcutaneous, and we’re also considering the potential to use the system for intraocular and intratumoral administration. It’s applicable for vaccines, monoclonal antibodies, coagulation factors, insulin and GLP-1 agonists. Looking further into the future, we could even extend it to gene and cell therapies, which are currently generating significant interest in the industry.
Q In the autoinjector space, we’ve seen devices with a variety of delivery volumes – up to 5 mL – what is the upper volume limit for EuroJect®?
AThe capacity is 4 mL but, for injection, we consider the upper dose limit to be around 1.5 mL, as we need some air to push the product during delivery. Alternatively, the ampoule can be used as a primary container to aspirate the full volume for transfer or reconstitution.
“EuroJect® has a significant advantage for extractables and leachables, which is that it only has one component, LDPE, whereas glass is often coated and may add other molecules, complicating its extractables and leachables profile.”
Q How do you manage the quality and safety of therapeutics during the filling process for EuroJect®, for example, how do you manage temperature during the BFS process for sensitive biologics?
A The BFS technology melts the polymer to form the primary container, which, as you can imagine, requires high temperatures. However, we use machine options to cool down the drug product and limit the heat it experiences. During experiments using a thermochrome indicator, we’ve validated that, for a minimum of 90% of the product, the temperature never exceeds 40°C during filling, even for a few seconds. We’ve conducted experiments and tests with biologics, proteins and live attenuated viruses that have confirmed no loss in biochemical and functional activity.
Considering safety and quality more broadly, we have several controls throughout the filling process, including automatic visual and leakage inspections. Another challenge is detecting particles, given the machine’s speed. Regarding extractables, Unither has 30 years of experience with this technology, so we have comprehensive data on the extractables from LDPE. For leachables, it depends on the product, and we conduct trials to evaluate them.
Q Speaking of extractables and leachables, how does EuroJectv compare with glass on that front?
A EuroJect® has a significant advantage for extractables and leachables, which is that it only has one component, LDPE, whereas glass is often coated and may add other molecules, complicating its extractables and leachables profile. Our system is simpler as we don’t have these additional components. Adding compounds increases the complexity of potential interactions with different products. A common example is silicone coating, which is often used as a lubricant in glass syringes – with EuroJect®, we don’t have to worry about any of that.
Q Is there anything else you’d like to add or any points you’d like to make that we haven’t covered?
A As I’ve mentioned, EuroJect® is a monomaterial LDPE device, which makes it highly recyclable. We already recycle leftover LDPE from the production process, and we’re planning to organise the collection and recycling of used doses. LDPE is easy to sort for waste management and, in terms of raw material, we receive LDPE in bulk, reducing packaging waste. During melting, LDPE is sterilised, eliminating waste. EuroJect® is beginning to be recognised for its sustainability advantages compared with traditional packaging methods for biologics and injectables.