Citation: Beckstoffer D, “Material Selection and Efficient Development Processes for Wearable Injector Drive Systems”. ONdrugDelivery, Issue 163 (Jul 2024), pp 36–39.
Dave Beckstoffer explains the importance of material selection in drive system development, the key attributes of materials towards a wearable and auto-delivery device, and discusses the need to achieve industrialisation based on material selection and relevant manufacturing processes.
“In line with increasing demand from the pharmaceutical market to deliver biologics from wearable devices, demand is increasing on the drive systems that power drug delivery.”
Drive systems for wearable and automatic drug delivery devices are central to patient outcomes. Key to ensuring the value of these devices is materials specification, which helps to achieve critical factors such as delivery precision, device reliability and light weight for comfortable use. Material selection also significantly impacts the industrialisation of the drive system. Whether or not the design can achieve the right performance, at the right cost point, means a focus on material selection is essential throughout a development project.
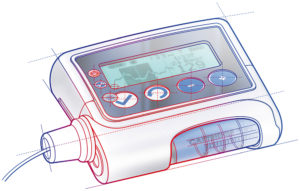
Figure 1: Rendering of a wearable infusion pump.
In line with increasing demand from the pharmaceutical market to deliver biologics from wearable devices, demand is increasing on the drive systems that power these drug delivery devices. While ensuring that the drive systems achieve essential requirements relating to treatment efficacy, patient safety and wearer comfort, the design must also optimise commercial viability. This means turning an effective concept into an industrialised product, from a computer assisted design (CAD) drawing and prototype through to manufacturing scale (Figures 1 and 2).
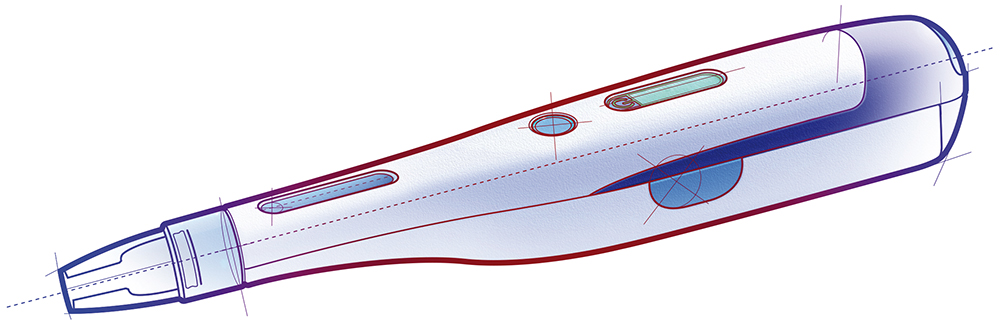
Figure 2: Rendering of an autoinjector.
Crucial to achieving a commercially viable, industrial-scale production drive system is material selection, and the implications of the types of material used are far reaching. The selection impacts the performance of the device from the patient perspective, where competing design needs must be balanced. The material specification also depends on meeting medical device conformance, as well as ensuring effective integration with the actuation mechanism.
To optimise commercial viability, these material requirements must be carefully balanced to minimise cost. However, the materials used in the early stages of development, including prototyping, can differ significantly to those necessary for a final, production-ready design. Every iteration impacts the next, so this process must be carefully managed, avoiding deviations in material selection that can affect the delivery of the overall project, including the ability to efficiently industrialise a design. As a result, a guiding theme in drive system development is to focus on material selection at the earliest opportunity and maintain this focus throughout.
MATERIAL SELECTION ON PAPER
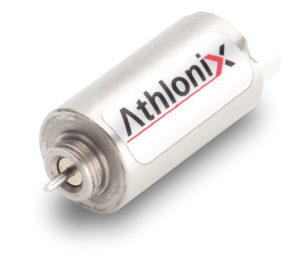
Figure 3: A 10 mm brush DC motor used for drive and delivery systems.
Each drive and delivery system has its own requirements relating to factors such as drug viscosity and method of delivery, so the design is typically customised. An overriding factor across all wearable devices and autoinjectors is the need for a compact form with low weight to achieve patient ergonomic requirements. Direct current (DC) micro-motors are typically optimal for these characteristics, such as having a diameter as small as just 10 mm. However, the gearbox is often the larger component, especially when the design has an integrated output drive mechanism, such as a lead screw or a pump. As a result, the gear system and drive mechanism present the typical opportunity for customisation, and this includes material selection too (Figure 3).
“The drive system must ensure reliability, informed by the required volume of delivery cycles and lifetime of the device.”
In addition to size and weight requirements, the fundamental design needs, supported by material choice, include the efficacy and safety of drug delivery. This means that the drive system must ensure reliability, informed by the required volume of delivery cycles and lifetime of the device. Here, material choice is integral.
For example, plastic, such as polyphenylene sulphide or polyamide, may be a suitable material for use up to 100 hours, while applications with higher physical demands and lifetimes up to 3,000 hours would need a more durable material. Metal, such as stainless steel, aluminium or brass, is typically used in these instances. Dealing with day-to-day use, the delivery system must also be able to withstand accidental drops and impacts.
DESIGNING FOR PRODUCTION
Efficacy and safety of treatment also depend on accuracy of delivery – here, too, materials are an important consideration. For continual 24/7 administration, moulded plastic components might be sufficient, whereas, for infrequent, low-volume dosing, metal machined drive components might be necessary to achieve accuracy of ±0.5%.
Keeping the patient at the forefront of the design also means that the device requires an efficient system that minimises energy use, enabling a smaller and lighter battery system. The device should also minimise audible noise – the longer the lifecycle, the more important this is. While metal gears are typically more efficient, achieving lower friction losses, plastic gears are usually quieter, with reduced audible output during meshing.
Material demands can also impact conformance requirements, from common needs such as Restriction of Hazardous Substances (RoHS), Registration, Evaluation and Authorisation of Chemicals (REACh) and Conflict Minerals, through to meeting manufacturing regulations such as ISO 13485 (Quality Management System for Medical Devices) and IEC 60601 (Medical Electrical Equipment Safety Standards).
To optimise the industrialisation of a design, balancing the required criteria will help to guide material selection from a cost perspective. However, this does not just relate to the value of the raw materials but also includes the cost of the manufacturing process.
DESIGN CONCEPTS AND MATERIAL CHOICE
Designing the drive and delivery mechanism to achieve the best outcome for the patient, which includes specifying the ideal materials, is the right starting principle. However, the need to develop certain elements of the design sequentially to varying schedules means that the materials used at each phase will also likely change as the project progresses (Figure 4).
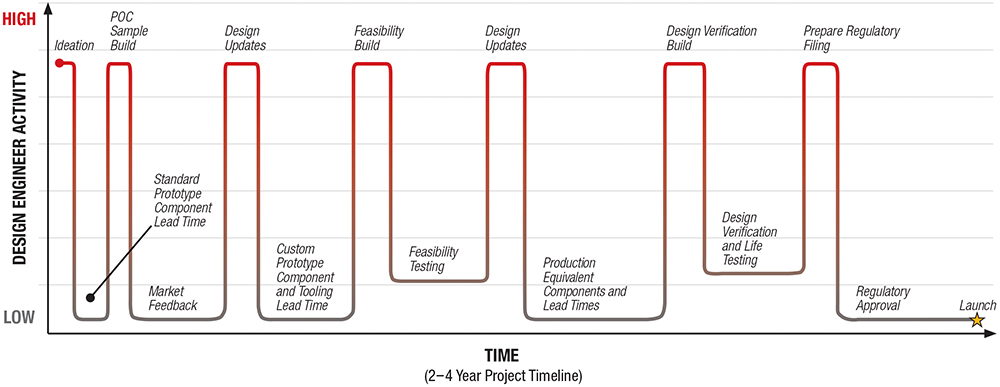
Figure 4: Example project timeline from concept to launch.
“In real-world development, a drug delivery design contractor, or the motion developer, needs to prove the concept to the pharmaceutical company.”
In real-world development, a drug delivery design contractor, or the motion developer, needs to prove the concept to the pharmaceutical company. This stage will take place within a specific, and relatively short, timescale; the quicker it can be done, the faster the delivery device can be brought to market. To achieve this, initial decisions around material selection and part design are often made based on speed and availability, rather than optimising for longer-term design objectives.
Off-the-shelf drive system designs might be used to confirm general requirements. From the start, this means that there can be a discrepancy between the materials involved in a conceptual test compared with those ultimately required for an industrialised product.
PROTOTYPING
At this stage, 3D-printed parts are commonly introduced, with their short lead times being a key advantage for the development of a low-volume parts run. While it is possible to prototype a drive and delivery system in a metal 3D print, commonly, plastic 3D printing is used because of its advantages in simplicity, speed and cost. While there will be limitations in the tolerances of 3D printed parts, material testing will not be a factor at this stage.
However, the key consideration during the concept phase, as well as throughout the feasibility stage of development, is that it is important to make decisions regarding materials and designs that can be carried forwards into industrialisation. This means that, at the project’s culmination, the desired material qualities can be achieved at high manufacturing scale and at the forecasted cost point. If not, the deviation in material choice between design iterations can become restrictive towards meeting the final specification.
This challenge may only be realised, as late as the validation and verification stage, where the design is nearly set for confirmation. At this stage, a resolution will require either a rework of previous design steps, adding time and cost to the project overall while the design and materials are revised, or it will mean that the final design objectives are unable to be met.
MOVING FROM CONCEPT TO PRODUCTION
The design process is complex, and there are a multitude of reasons why it may reach an industrialisation pivot point, which occurs when a part that is effective from a performance perspective fails to be commercially viable because of manufacturing capabilities or cost. Either the final part becomes prohibitively expensive to manufacture in the desired material, or the specified material does not meet the intended tolerance.
For precision, machined metal parts may prove the concept, but they may not be viable for the industrialisation of all drug delivery devices. Alternatively, plastic moulding can deliver high volume, economical manufacture, but it might not deliver the required tolerance if accuracy is vital.
COMMUNICATION IN DESIGN AND MATERIALS SPECIFICATION
A key point of friction during device development is design and material changes to components in the drive and delivery system that are made in isolation. From using metal components that could react to the motor’s magnets, to the decision on whether or not to use plastic or metal parts in gearing and how this might integrate with the delivery system, material selections must be made in conjunction with each other. Similarly, commercial demands introduced during ongoing development could ask for a cost reduction – or for a shorter timeframe – on the procurement of specific parts. This should be met with a thorough examination of how this would impact material specifications, including the subsequent impact on other system components.
Ultimately, the only way to fully validate material selection for a given design is by testing products from the manufacturing run. Of course, in reality, this is too late, so the most effective means of achieving the right material specification is through the decisions that are made earlier on in the project.
“At every stage of development, keeping a focus on the materials used is crucial.”
At every stage of development, keeping a focus on the materials used is crucial. Supporting this, communication throughout all stages – between the pharmaceutical company, device design contractor, drive system developer and material suppliers – is also key. The more that the various aspects of the design process, including materials specification, are considered in parallel, the more efficient the entire process will be in achieving the optimised industrialisation of the drive system.