To Issue 166
Citation: Ingvarsson P, “Nolato’s Virtual Factory”. ONdrugDelivery, Issue 166 (Oct 2024), pp 96–99.
Patrik Ingvarsson, showcases the Nolato‘s virtual factory, highlighting the advantages of virtual tools for product development in the medical device industry.
Design robustness can be improved through the combination of injection moulding software with measuring software (Figure 1). Advantages of this combination can include avoiding some of the following:
- Project delays
- Tool adjustments
- Moulding imperfections
- Material changes
- Manufacturing defects affecting device functionality
- Delayed process qualifications
- Unpredictable outcomes
- Late and costly design changes
- Inaccurate measurements
- Expensive moulds.
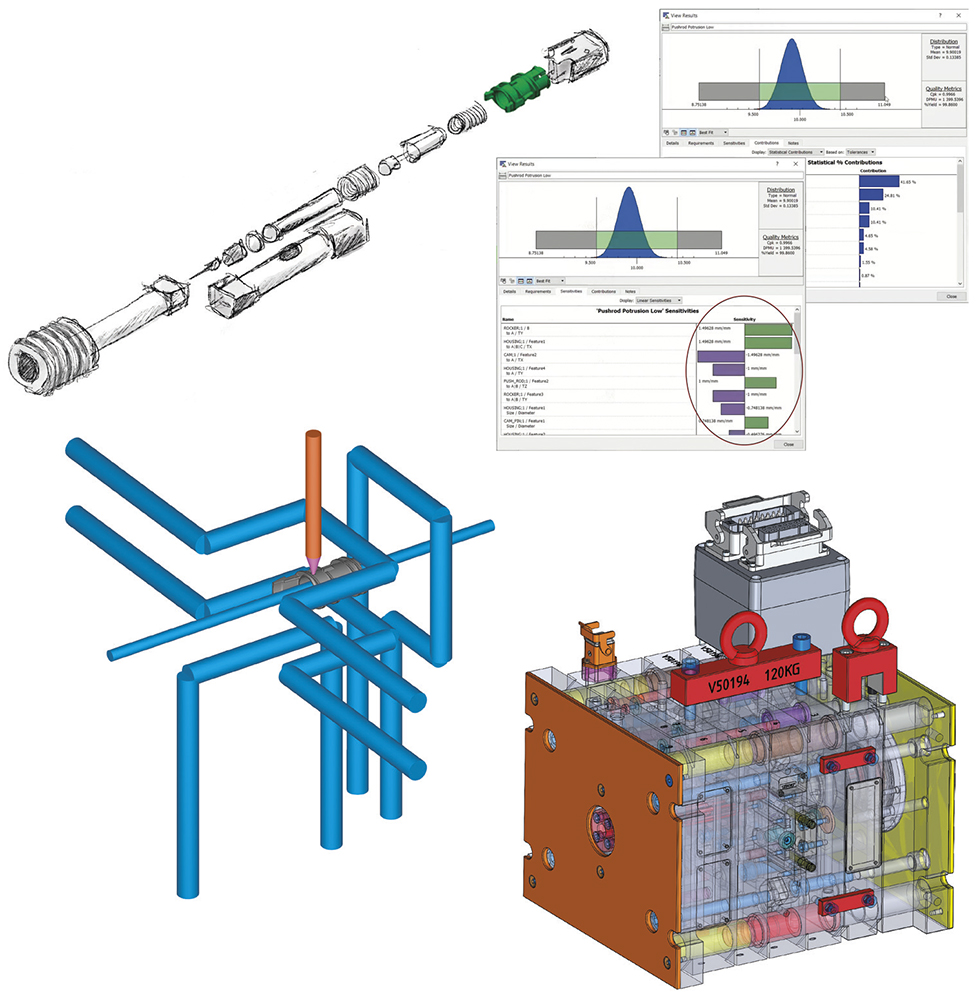
Figure 1: Injection moulding software combined with measuring software.
As technology progresses, it becomes increasingly important to use virtual simulations to continue advancing and improving product development, manufacturing and industrialisation workflows. Simulations offer a safe and cost-effective environment for optimisation, testing and evaluation to identify the best design.
“Virtual tools, such as mould flow simulation software, mechanical simulation software and virtual measuring software, provide project teams with invaluable data and information.”
Virtual tools, such as mould flow simulation software, mechanical simulation software and virtual measuring software, provide project teams with invaluable data and information. Combining these tools revolutionises the development process, and it is possible to predict the final result on a whole new level. For example, it allows for full dimensional virtual measurement of virtually manufactured components based on mould flow simulations, using the same measurement principles and machine parameters that will be used for physical components at a later stage (Figure 2).
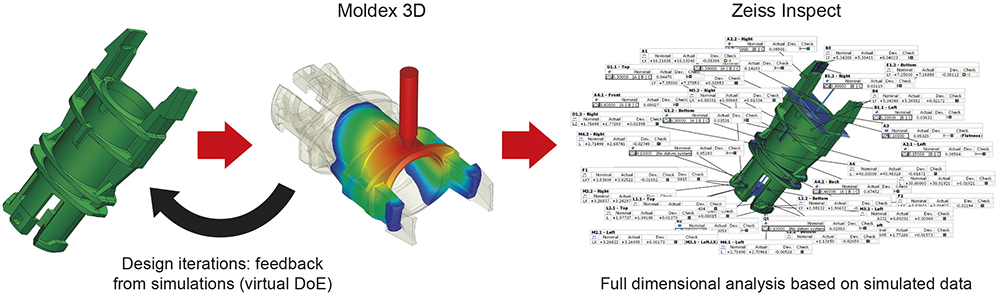
Figure 2: Virtual tools provide project teams with invaluable data and information.
DESIGN AND TOLERANCES
The successful development of new products within the medical device industry requires close collaboration between designers/customers and manufacturers.
“Confidence and control of product functionality is key to achieving the perfect balance between focusing on critical dimensions and allowing wider tolerances for less important features.”
Confidence and control of product functionality is key to achieving the perfect balance between focusing on critical dimensions and allowing wider tolerances for less important features. Nolato therefore recommends using tolerance analysis software to shorten lead times and build confidence in the design.
Tolerance standards for plastic moulded parts, taking into account material selection and production conditions, should also be used as a guideline and reference for dimensional reviews.
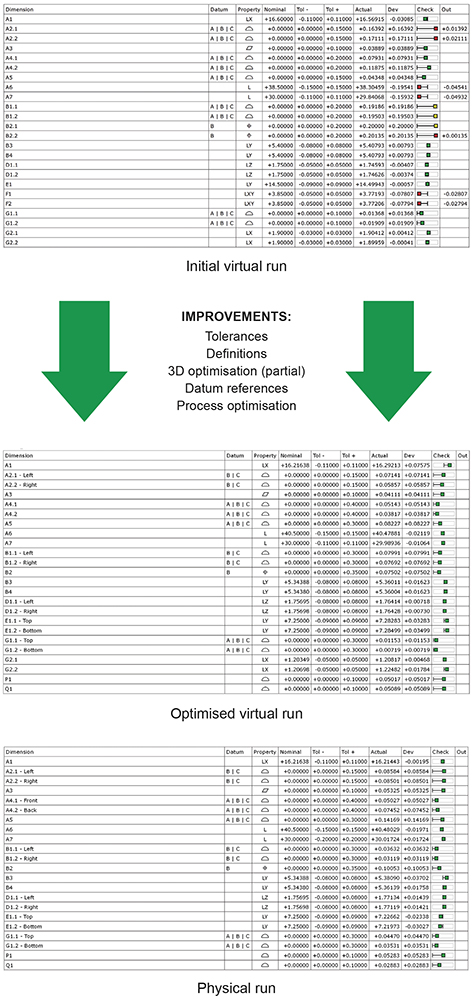
Figure 3: The use of virtual testing enables designers to improve and optimise a mould ahead of physical testing, thereby saving time and cost.
DATA-DRIVEN MOULD DESIGN
For customers seeking excellence in their injection mould design and looking to reduce the number of unnecessary tool iterations to reduce time to market, the answer is to involve Nolato in the early development phase.
Using a virtual toolbox consisting of advanced mould flow simulations, finite element analysis simulations and tolerance analysis software, and combining them with the power of dimensional evaluation in measuring software, it is possible to predict outcomes and effectively evaluate different design options with high confidence.
With the software, Nolato fine-tunes gate positions, evaluates cooling layouts and optimises the design from a moulding and product perspective. Moulding imperfections, such as sink marks, air enclosures and weak areas, are identified at an early stage and can then be resolved or reduced. By using a measurement program, developed alongside the design work, complete virtual measurement reports can be provided for all virtual test runs and design of experiments (Figure 3). This makes it more efficient to analyse and select the best design track.
STEEL STRATEGIES
Adjusting injection moulding moulds after the first out of tools (FOT) can pose several risks, including incorrect adjustments, tool damage, cost overruns and more. Nolato believes in using steel strategies to address warpage and displacement issues identified during virtual runs using virtual measurements. This applies not only to surfaces that are steel safe (steel added with intention to remove) but also to surfaces where steel is removed upfront (more aggressive approach). This saves time and will result in higher accuracy than adjusting the mould afterwards.
ROBUST MEASUREMENT STRATEGIES
Nolato supports customers with metrology expertise in the early development phase. The company provides advice and works with clients to develop robust measurement methods and define the individual dimensions to secure product functionality and a reliable control method.
The measuring software normally used for 3D scanning is developed based on virtually manufactured models (from mould flow simulation). Measuring software can evaluate all kinds of dimensions of virtual components. The benefit of this is that the company can check all dimensions from the simulation, and also review the checks from a functional point of view and verify the strategies upfront.
“Simulations allow the identification of any moulding or design issues early on in the process.”
Shorter Lead Times
Simulations allow the identification of any moulding or design issues early on in the process, reducing lead times for product development and the risk of delays later on due to unidentified issues.
MEASUREMENT AGREEMENTS
Even if model-based definitions are used, the most common way of defining dimensions and tolerances is still using 2D drawings. The main problem with 2D drawings is ambiguous definitions of dimensions, which could result in additional work and misinterpretations during measurements and evaluations.
To mitigate the risk of this, measurement agreements should be established between manufacturer and designer/customer in which every dimension is set out in detail using text and images. The same applies to alignments and datum systems, in other words, anything that could have an impact on the result. Control and alignment are important.
MOULD QUALIFICATION
Mould qualification greatly benefits from using the combined strength of virtual tools: virtual manufacturing, virtual testing and virtual evaluation. Simulations and a robust design significantly enhance mould qualifications by optimising the mould design, detecting potential issues early on, saving time and costs, ensuring precise tolerance analysis and facilitating regulatory compliance.
The virtual factory will have already prepared initial settings for run-in, evaluated the process window and identified and resolved weaknesses, ensuring higher success rates during qualification.
“Since measurement programs will have already been developed during the evaluation of virtual samples, time saving and risk mitigations will have also been established.”
Since measurement programs will have already been developed during the evaluation of virtual samples, time saving and risk mitigations will have also been established and will be ready to evaluate physical samples.
CONCLUSION
To optimise the product development process and ensure high product quality, bring Nolato on board, preferably before the design is frozen and moulds have been ordered. Nolato’s team of experts is ready to support the customer in developing state-of-the-art products, optimised for high-volume production.