To Issue 151
Citation: “Product Showcase: Complete System for Standard-Compliant Testing of Wearable Autoinjectors”. ONdrugDelivery, Issue 151 (Sep 2023), pp 72–74.
Specifically tailored to on-body delivery systems (OBDSs) / wearable injectors, ZwickRoell showcases its customised, comprehensive solution for performing functional tests in accordance with the ISO 11608-6 standard.
One of the most exciting areas of development in injectable drug delivery is on-body delivery systems (OBDSs), also known as wearable autoinjectors or simply wearables. These are devices that automatically administer highly viscous biologic drugs, while attached to the patient’s body. In the fast-growing market for biotechnological applications, machine manufacturer ZwickRoell now offers a customised, comprehensive solution for performing functional tests in accordance with the ISO 11608-6 standard.
“ZwickRoell now offers a customised, comprehensive solution for performing functional tests in accordance with the ISO 11608-6 standard.”
People suffering from an illness are likely to recover faster in a familiar environment – in other words, at home. For chronically ill patients, shortening the healing process is of particular significance and OBDSs can help achieve this. They not only reduce the cost of long-term therapies; they also have the ability to promote patient comfort by allowing them to set up and undergo treatment in their own surroundings. These systems can reduce the required frequency of visits to a clinic or doctor’s office for injections that would otherwise have to be administered by qualified personnel.
The benefits provided by an injection system securely attached to the patient’s body are clear – they reduce the possible risks that result from the administration of medicines through more commonly used needle-based injection systems. Additionally, they are capable of optimally dispensing drug volumes ranging from 2 mL to 20 mL, in time intervals from as little as a few seconds up to several hours. This form of therapy is ideal for daily self-treatment and can be implemented without having to spend time in a medical facility. The adhesive side of the injection system is attached directly to the patient’s skin, and the injection is administered through a needle or cannula integrated in the device.
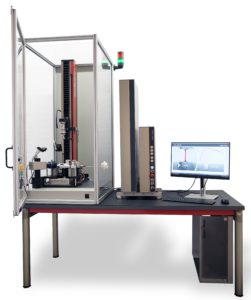
Figure 1: Universal testing system for function tests on OBDSs.
SEMI-AUTOMATED TESTING SOLUTION
However, in today’s OBDS market – which is growing by more than 20% annually – manufacturers face a number of challenges when it comes to developing large-volume injectors. More specifically, ISO 11608-6 requires them to test the forces experienced by the device during the injection process due to the viscosity of the drug, the high volume, the injection time, the internal diameter of the syringe and needle, the needle length and any frictional forces (including static friction).
ZwickRoell has responded to this challenge by applying its many years of experience in materials testing and collaborating with pharmaceutical companies and autoinjector device manufacturers to develop a sequential testing solution for OBDSs (Figure 1). The solution is based on the zwickiLine 2.5 kN static testing machine.
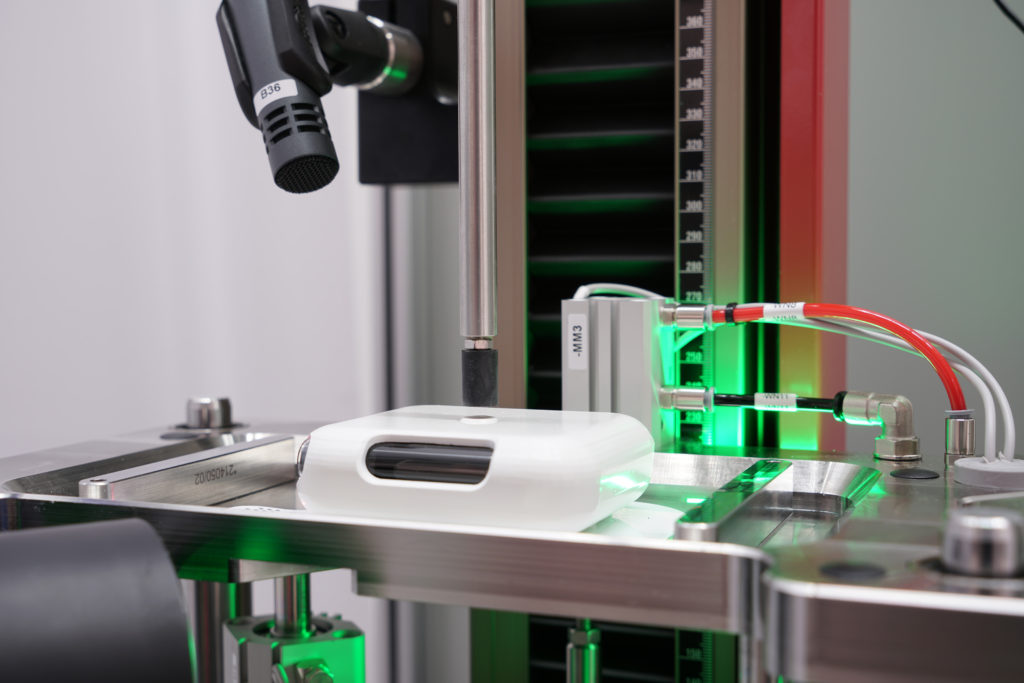
Figure 2: The machine measures the force required to trigger the actuation button.
“Throughout the machine development process, ZwickRoell accounted for every requirement specification included in the standard.”
With a number of newly designed adaptations, the machine now measures the force required to trigger the actuation button (Figure 2), as well as the injection depth, injection time and the amount of liquid delivered using a high-resolution, camera-based measuring system (Figure 3). An integrated camera records the process to verify how the sequences of the display elements react and documents the audible signals (clicking sounds) of the injection system via a microphone.
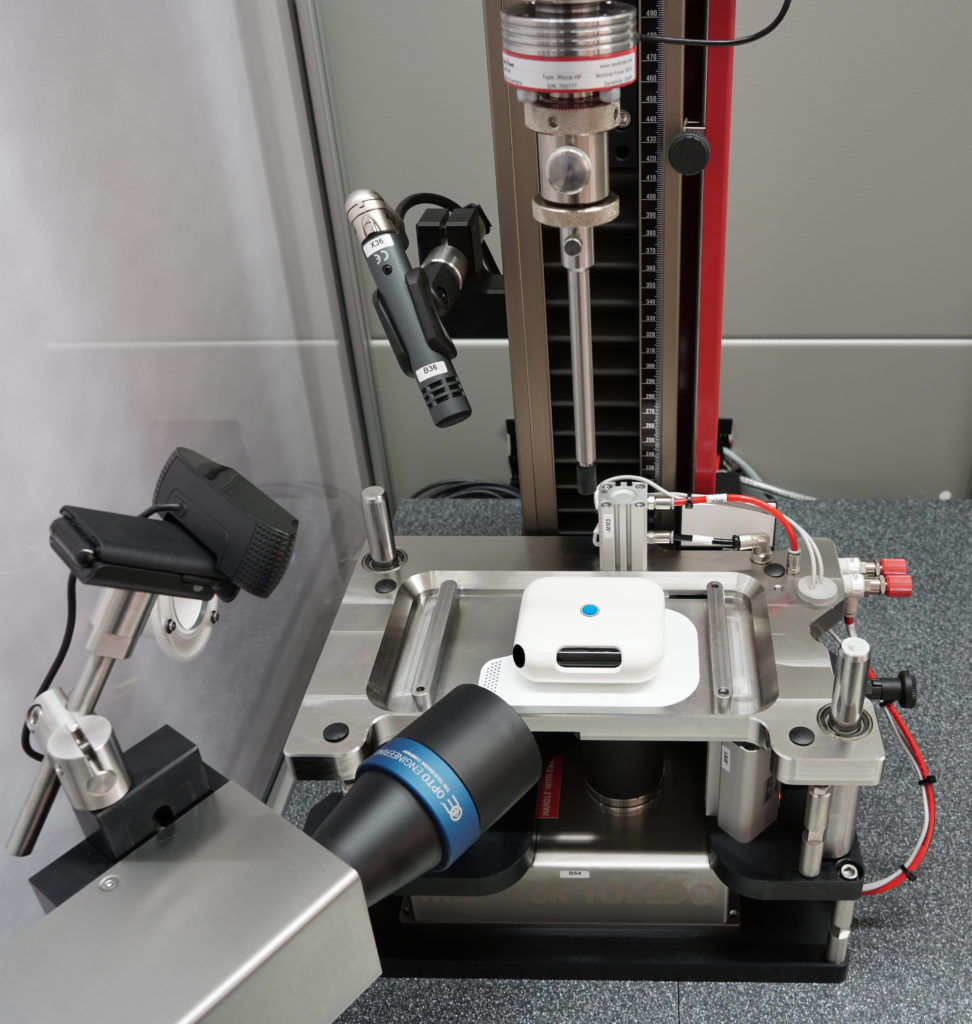
Figure 3: A high-resolution, camera-based measuring system is used.
In a second test area, the testing machine optionally supports additional tests, such as determining the adhesion force of the bonding surface.
TRACEABILITY OF TEST RESULTS
Another advantage of ZwickRoell’s comprehensive solution is the corresponding test sequence for its testXpert III testing software. It not only documents the obtained results, but also quickly displays them in a clearly presented format. For maximum transparency and secure traceability for validation and quality control, the machine performs the tests reliably and according to the required standards. This is important because, in the biotechnology sector and the pharmaceutical industry, it is imperative to know who did what, when and why, and who is responsible. Every action must be documented in a tamper-proof and traceable manner, according to US FDA CFR Part 11.
Throughout the machine development process, ZwickRoell accounted for every requirement specification included in the standard. The result is a complete solution for the development of autoinjectors for cancer treatment therapies, autoimmune diseases and neurological disorders. ZwickRoell says this is very close to meeting every customer requirement and is ultimately intended to benefit the patient.
Find out more about ZwickRoell’s drug delivery device testing at: www.zwickroell.com/industries/medicalpharmaceutical/therapy-systems.