Citation: Glöckler L, Delauney C, “State-of-the-Art Solutions for Ophthalmic Sterile Drug Product Manufacturing.” ONdrugDelivery, Issue 118 (Apr 2021), pp 8–10.
In the first in a series of two articles, Rainer Glöckler and Carole Delauney discuss how Swissfillon’s state-of-the-art filling line meets the requirements and complexities that are particular to ophthalmic drug product manufacturing. The second article, to be published in May, will explore partnerships between pharma, CDMOs and syringe manufacturers in more detail.
Advanced drug products (DPs) filled in innovative containers, with small to midsize annual demand (fewer than 500,000 units) pose a major challenge to existing manufacturing business models based on large throughputs. Ophthalmic DPs, which often fit into this advanced DP category, additionally require a high level of process knowhow and state-of-the-art manufacturing technologies in order to maximise safety, meet stringent regulatory requirements and minimise costs.
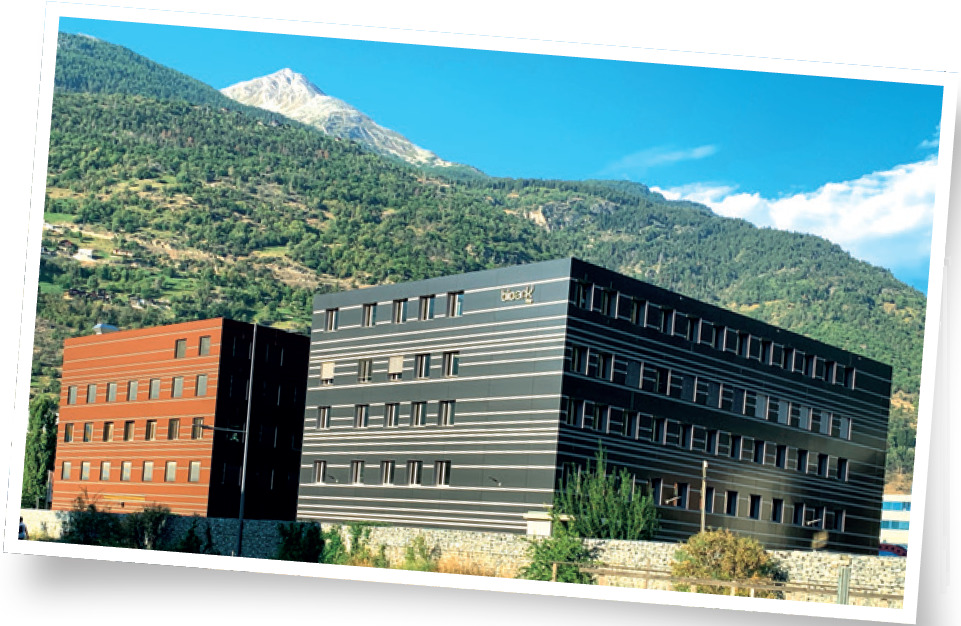
Figure 1: Swissfillon’s facility in Visp, Switzerland.
Here we will show how Swissfillon’s aseptic manufacturing services, and its innovative, fully automated, highly flexible filling line at its facility in Visp, Switzerland (Figure 1), are perfectly positioned to fulfill the requirements of this market segment.
OVERVIEW OF THE OPHTHALMIC MARKET FOR RETINAL DISORDERS
Retinal disorders include diabetic retinopathy and age-related macular degeneration. They are caused partly by over-production of a protein called vascular endothelial growth factor (VEGF), and are treated with anti-VEGF drugs, which can be administered by intravitreal injection into the back of the eye using prefilled syringes. These require the highest quality primary packaging and DP manufacturing (filling) technologies which ensure maximum safety, meet regulatory requirements and minimise overfill of the syringes.
The global ophthalmic drug market is forecasted to grow from US$28.4 billion (£20.1 billion) in 2020 to $36.2 billion in 2025, and to reach $47.6 billion by 2030. In 2020, retinal disorder drugs accounted for the largest share of the market, with sales of $13.1 billion and 46% market share.1 Growth in the market will be driven by the rapidly ageing global population, the increasing prevalence of diabetes leading to ocular diseases, unmet clinical needs in many disease areas, and economic growth resulting in increased demand in developing countries, particularly in Asia.
The opening up of the market to biosimilar drugs as the patents of blockbuster drugs expire over the next few years represents a major opportunity for new players wishing to enter the sector, and pharma companies are working on next-generation ophthalmic formulations. The R&D pipeline for drugs to treat retinal disorders is very strong, with new classes of therapeutic agents and innovative formulations being developed by biopharma companies.
SPECIFIC REQUIREMENTS AND COMPLEXITY IN OPHTHALMIC DP MANUFACTURING
“At the Phase II clinical stage, as the product becomes more mature, there is often a switch from vials to prefilled syringes.”
In most cases, the vial is the preferred choice for primary packaging at the development stage. At the Phase II clinical stage, as the product becomes more mature, there is often a switch from vials to prefilled syringes. For some indications, including ophthalmics, vials are preferred for some specific markets, and therefore they remain a focus until the DP reaches the market.
Key considerations for ophthalmic primary packaging and DP manufacturing are set out below.
Manufacture Vials and Prefilled Syringes for the Same DP
The Optima multipurpose filling line qualified at Swissfillon (Figure 2) offers the flexibility for customers to fill both vials and syringes during the full cycle of their product launch on the same machine. As long as the packaging is already implemented on Swissfillon’s system and the starting material is available, the customer can place a purchase order for filling vials or prefilled syringes and can readily switch from one to the other. Swissfillon has very good relationships with the main primary packaging suppliers offering ophthalmic solutions, which leads to improved and timely solutions for customers.
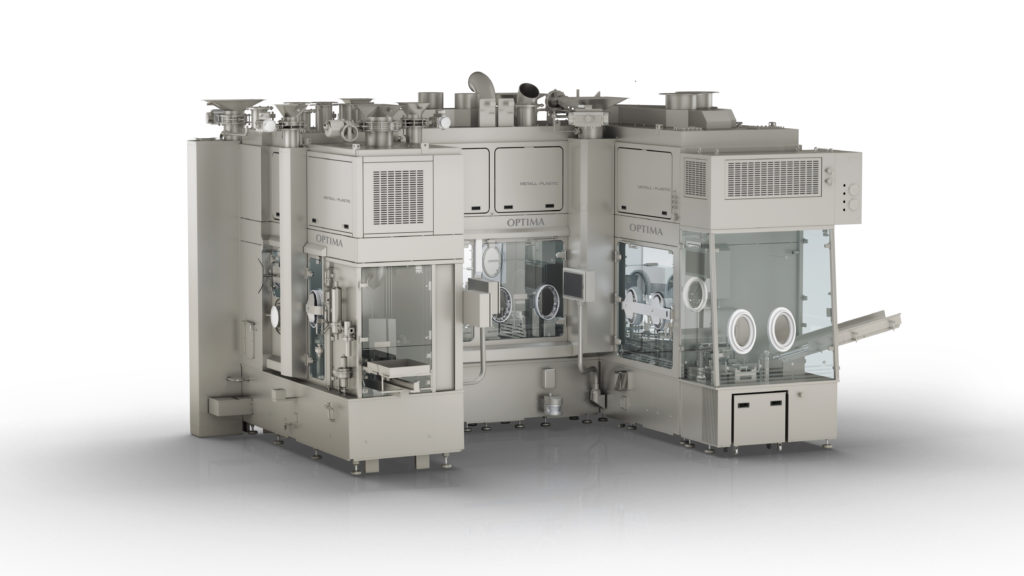
Figure 2: The heart of Swissfillon – the filling machine from Optima.
Meeting Regulatory Requirements on Subvisible Particles and Avoiding “Floaters”
Ophthalmic drugs should essentially be free of visible and subvisible particles. These can occur due to contamination or may arise from primary packaging or during the filling process. There is evidence that silicone oil plays a role in both the denaturation of proteins and the initiation of aggregation processes in proteins.2 USP <789> relates to visible and subvisible particles, and there are specific guidelines for clinical ophthalmic applications. Even if the subvisible particle requirement is met, “floaters” may occur. These are a kind of a micro silicone oil droplet which remains in the eye.3
Ensuring Accuracy at Low Volumes
“Swissfillon’s speciality is that its filling line transports through vial by vial or syringe by syringe on the same machine.”
The range of the fill volume is usually 100–200 μL. Swissfillon’s speciality is that its filling line transports through vial by vial or syringe by syringe on the same machine. This allows every container to be weighed using the tare and gross weigh installed on the machine, so it can calculate how much volume there is in each container, and a feedback loop corrects the pump automatically.
This approach means it can achieve exceptionally precise filling. Despite such low fill volumes, Swissfillon guarantees an accuracy of ±5%, and typically achieves an accuracy well within ±2%. Also, any underfill or overfill results in just a single syringe being rejected, compared with nest filling where inaccurate filling would usually result in 10 to 50 syringes being rejected. If required, Swissfillon is able to perform filling activities for ophthalmic drugs using a rotary piston pump, which precludes the possibility of particulates occurring due to damage to the pump tubing.
Minimising Overfill for Drug Substance Cost Savings
Containers are typically overfilled by a factor of three in order to guarantee the safe expected extractable volume, either directly injected from the prefilled syringe or extracted from a vial before injection. This means that two-thirds of the drug substance is wasted. A close relationship during the development phase between the primary packaging manufacturer and the filling company can help to minimise overfill and lead to significant cost savings for the client.
Bubble-Free Process
“A drug manufacturer can minimise risks by working with experts who have a proven track record and who are able to offer the latest technology.”
When required for a specific project, Swissfillon can offer vacuum filling in order to remove or reduce residual air in the system. This is important for a number of reasons:
- Denaturation of a protein-based product could start at the fluid-air interface.
- The container may be exposed to variations in pressure during transport, leading to stopper movement and loss of sterility of the product.
- Final sterilisation which involves vacuum can be carried out more easily if the bubble is smaller.
- Any air in the container must be expelled before an injection can be administered, and this will result in loss of the drug substance.
- If the drug has a high viscosity, any existing small air bubbles cannot be removed and so would be injected into the eye.
Stoppering
Implementation of the stoppering process on a filling line can be highly complex when using very small stoppers to close 0.5 mL prefilled syringes. In addition, the behaviour of stoppers developed for the ophthalmic market (i.e. silicone oil-free) means that the DP manufacturing requires an even higher level of expertise and know-how from the contract development and manufacturing organisation (CDMO) to guarantee that the stoppers are correctly transported and positioned and are not damaged.
SWISSFILLON ADVANTAGES MEET OPHTHALMIC DP REQUIREMENTS
Due to the many complexities and specific requirements for ophthalmic DPs, a drug manufacturer can minimise risks by working with experts who have a proven track record and who are able to offer the latest technology.
Swissfillon’s key principles are readiness and communication. Time to market is often a key factor in the success of a new product and one of the most critical steps is the time taken to establish a process on its filling machine. This requires discussions on the best way to work together so that the solution can be achieved on the machine in the shortest possible time. Tiny details in the process can have a huge impact on the finish, and it is vital to optimise the overall value chain.
Swissfillon’s filling line provides exceptional flexibility, accuracy and efficiency, with a 100% automated filling process in which every glove intervention is documented, 100% tare and gross weighing to deliver high accuracy on extremely low filling volumes, and 100% stopper setting control to minimise bubbles. Swissfillon is confident that it offers a best-in-class solution for ophthalmic drugs and can provide reliable and optimal solutions to meet your product’s specific requirements.
REFERENCES
- “Ophthalmic Drugs Market Size, Share & Trends Analysis Report By Disease (Dry Eye, Eye Allergy, Glaucoma, Eye Infection), By Drug Class, By Dosage Form, By Route Of Administration, By Product Type, By Region, And Segment Forecasts, 2021–2028”. Market Analysis Report, Grand View Research, Feb 2021.
- Khurana RN, Chang LK, Porco TC, “Incidence of Presumed Silicone Oil Droplets in the Vitreous Cavity After Intravitreal Bevacizumab Injection With Insulin Syringes”. JAMA Ophthalmol, 2017, Vol 135(7), pp 800–803.
- Yu JH et al, “Silicone oil droplets following intravitreal bevacizumab injections”. Am J Ophthalmol Case Rep, 2018, Vol 10, pp 142–144.