Citation: Niedermann N, “Success Factors for the Ypsomate Family of Autoinjectors”. ONdrugDelivery Magazine, Issue 101 (Oct 2019), pp 6-10.
Orfeo Niedermann looks at the key factors behind the growth and continued success of the YpsoMate family of two-step autoinjectors. He also introduces YpsoMate Design, which enables freeform outer shell design around the proven YpsoMate mechanism and manufacturing lines.
SIGNIFICANT DEMAND
With the large number of new biologics and biosimilar product launches, the demand for devices for the subcutaneous self-injection of biopharmaceuticals continues to grow and develop. Above all, the growing demand of autoinjectors for antibody-based therapies impresses the most.
“After the launch of the first disposable autoinjectors in 2006, for the administration of therapeutic proteins, it was believed that 1 mL was the maximum injectable volume that could be tolerated by a patient within the typical 10 second injection time. Over the last five years, however, this myth has been dispelled and the demand for therapies based on standardised 2.25 mL prefillable syringes compatible with autoinjectors has grown significantly.”
Some of the autoinjectors are used to cover the increased overall demand for biosimilars of blockbuster biologics, but most are needed for new injectable drugs, such as liquid-stable, once-weekly glucagon like peptide-1 analogues (GLP-1s) treating diabetes, and for treating autoimmune diseases, such as rheumatoid arthritis, psoriasis and multiple sclerosis. There are also many innovative biologics in pharma pipelines for treating a range of conditions including more specific arthritis indications, psoriasis, IBD/Crohn’s disease, dermatitis, asthma, migraine, orphan therapies, haemophilia and cancers.
After the launch of the first disposable autoinjectors in 2006, for the administration of therapeutic proteins, it was believed that 1 mL was the maximum injectable volume that could be tolerated by a patient within the typical 10 second injection time. Over the last five years, however, this myth has been dispelled and the demand for therapies based on standardised 2.25 mL prefillable syringes compatible with autoinjectors has grown significantly.
YPSOMATE – THE TWO-STEP AUTOINJECTOR
YpsoMate serves patients with an easy and convenient two-step automatic injection. The patient pulls off the cap to remove the needle shield from the prefilled syringe and then pushes the autoinjector onto the skin to trigger the injection. The operation does not involve any additional button-activated steps.
YpsoMate signals the start as well as the completion of the injection through clearly audible clicks. In parallel, the patient can observe the injection progress in the large viewing window. The needle remains hidden at all times and is shielded after use to prevent needle stick injuries. All these features are built into a compact housing that fits nicely into the palm of the hand and, due to its unique square shape, the YpsoMate autoinjector does not roll off tables or other flat surfaces.
“For more viscous drugs, Ypsomed has developed the YpsoMate 2.25 Pro – which uses the same proven handling concept – and features a proprietary constant force drive system.”
Low Risk, Short Time-to-Market
Ypsomed decouples the development of new platform products from the customer project and thereby moves the timeline and risks associated with platform development and installation of manufacturing infrastructure in-house.
Each customer-specific commercial variant is derived from an existing platform product based on proven technology. The custom product platform strategy continues to attract new customers and many established customers are running a number of projects at Ypsomed. Being able to work on multiple projects fosters a close working relationship, increases synergies and significantly reduces overall development timelines and project management activities for each programme.
Pharma partners continue to be attracted by the fast and low-risk supply of innovative injection systems manufactured on automated equipment in Switzerland and Ypsomed’s new manufacturing site in northern Germany.
YpsoMate Family of Autoinjectors
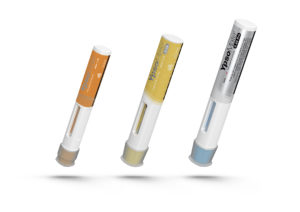
Figure 1: The family of YpsoMate autoinjectors with the YpsoMate for 1 mL long syringes (left), YpsoMate 2.25 for 2.25ml syringes (centre) and YpsoMate 2.25 Pro (right) for elevated viscosities.
Based on the preferred two-step use concept, Ypsomed has developed and industrialised a family of YpsoMate autoinjectors (see Figure 1) to support different drug needs. The YpsoMate 2.25 holds a 2.25 mL syringe and offers injection volumes up to 2 mL. For more viscous drugs, Ypsomed has developed the YpsoMate 2.25 Pro – which uses the same proven handling concept – and features a proprietary constant force drive system.
Reliability and Differentiation
A self-injection device should provide product differentiation through improved human factors and increased safety compared with vial-syringe and prefilled syringe product presentations. Moreover, pharma companies strive to differentiate their own self-injection device from devices used by competitors. Meeting these objectives can be challenging for pharma companies and device manufacturers.
A modern and safe self-injection device needs to be customised to fit the primary container, the formulation characteristics such as drug volume and viscosity, the needle insertion depth and injection time as required for certain therapies. YpsoMate is compatible with all major 1 mL long and 2.25 mL syringes made of glass or copolymer and can be customised within defined specification ranges for all relevant parameters and to new colours and shapes within defined design limits.
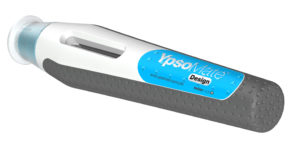
Figure 2: YpsoMate Design is an option to use the proven autoinjector technology and manufacturing line together with a unique free form outer design.
If specific patient groups or demand for differentiation in a specific market calls for a completely new outer shape Ypsomed offers YpsoMate Design (Figure 2).
The mechanism relies on the proven YpsoMate technology, and external design shells allow more design freedom to generate a unique and ergonomically optimised shape. In addition to the possibility of designing free-form surfaces, it is also possible to use different surface materials to improve grip and to emphasise how to hold and use the device.
AUTOMATED MANUFACTURING AT MULTIPLE FACILITIES
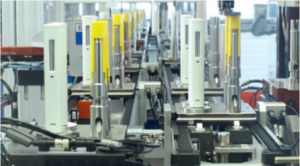
Figure 3: Fully automated assembly with validated process and IPC for YpsoMate and YpsoMate 2.25 (YpsoMate 2.25 pictured).
Consistent High Quality & Efficient Scale-Up
To keep timelines short and project upfront investment low, Ypsomed has invested in automated manufacturing capacity for YpsoMate and YpsoMate 2.25 (Figure 3). This allows customers to access and source the device at a fraction of the overall upfront cost compared with investing in bespoke manufacturing infrastructure. Furthermore, Ypsomed’s manufacturing infrastructure allows customers to increase their reserved capacity incrementally after launch when they have better control of the drug / device forecast.
Ypsomed increases the manufacturing capacity for YpsoMate autoinjectors continuously ahead of market demand based on customer forecasts. Today, Ypsomed has three automated lines installed and qualified that assemble the YpsoMate and YpsoMate 2.25 devices, with additional lines on order. With multiple lines situated in Switzerland and Germany, Ypsomed provides risk mitigation measures for its customers.
Ypsomed has invested in automated manufacturing capacity for YpsoMate and YpsoMate 2.25. This allows customers to access and source the device at a fraction of the overall upfront cost compared with investing in bespoke manufacturing infrastructure.”
Flexibility & Support for Final Assembly
For the drug and device end-assembly process, Ypsomed supports its pharma customers in selecting the best possible setup for their production and supply chain strategy. For pharma companies that want to assemble in-house, Ypsomed recommends a select number of renowned assembly equipment manufacturers that offer existing YpsoMate machine concepts for manual, semi-automatic and fully automated end-assembly covering different capacity needs.
Alternatively, the key global filling and packaging contract manufacturing organisations have installed equipment to assemble the YpsoMate autoinjector family. These end-assembly options provide customers with the freedom to implement the best final assembly set-up including backups and capacity increase options.
UPGRADE OPTION ADDS CONNECTIVITY
Connected drug delivery systems will become instrumental in improving medication adherence and supporting the effective self-management of chronic diseases. SmartPilot for YpsoMate (Figure 4) is a reusable connected add-on module with built-in sensor technology and wireless communication capabilities for the YpsoMate two-step autoinjector.
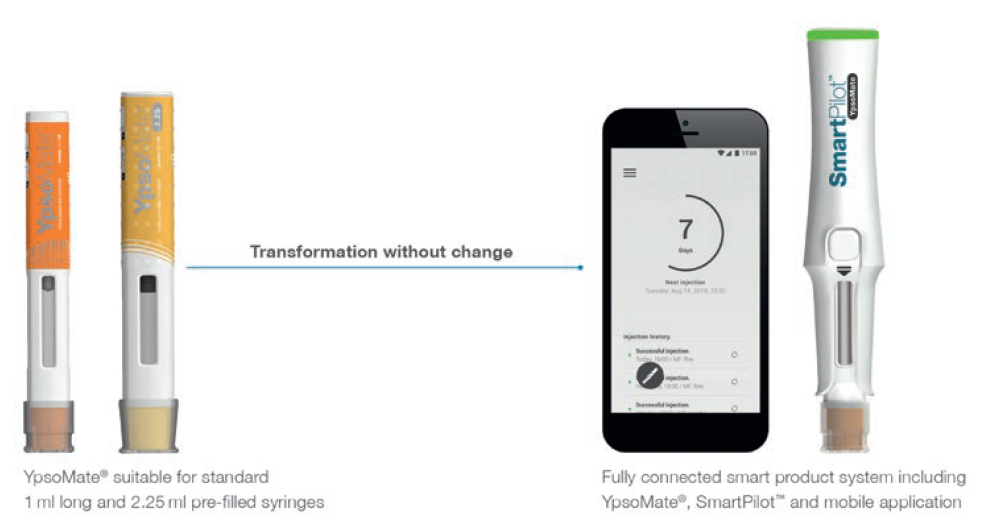
Figure 4: SmartPilot for YpsoMate is a reusable smart add-on that flexibly transforms YpsoMate into a fully connected system with advanced sensor capabilities to track device usage and guide patients.
With the help of the SmartPilot monitoring device, Ypsomed transforms every existing standard shape YpsoMate platform variant into a fully connected smart product system. SmartPilot comes with two sets of functionalities. One monitors device usage and makes available the therapy-relevant injection data to providers, caregivers and healthcare stakeholders using Bluetooth connectivity. The other guides patients step-by-step through the self-injection process including, for example, authentication of the self-injection device, or advice on the following use step.
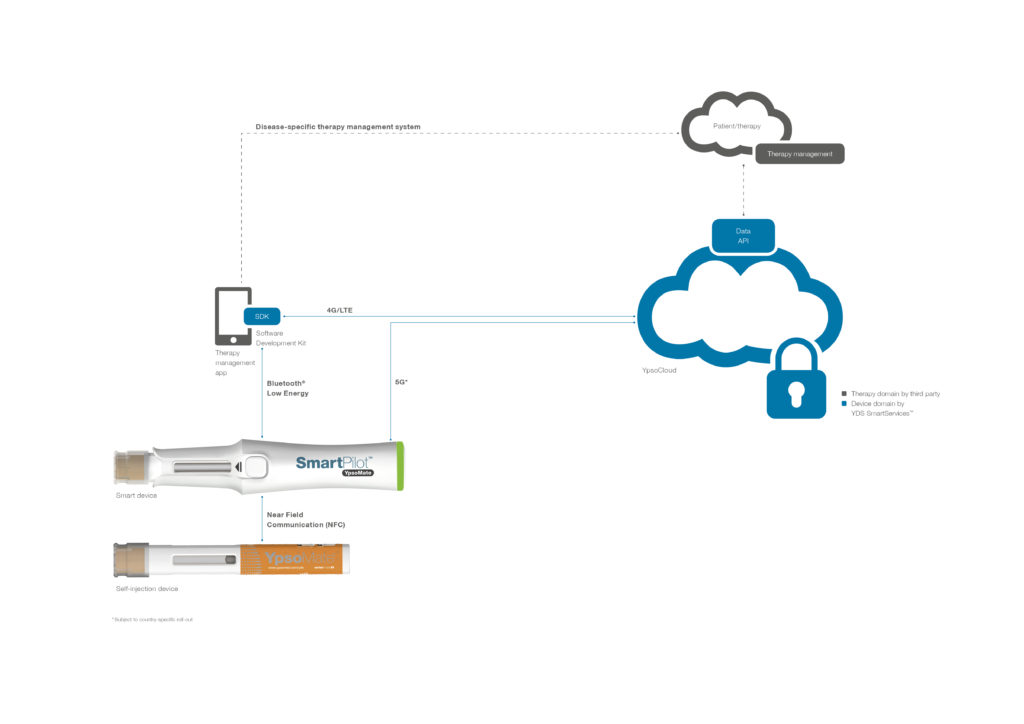
Figure 5: YDS SmartServices provides a secure, medical-grade device-to-cloud backbone for pharma partners.
“With SmartPilot and YDS SmartServices, Ypsomed has built a device and full device management solution that allows pharma customers to develop therapies and services rapidly that address non adherence in clinical trials and commercially.”
The adoption of connected devices requires the implementation of scalable device-to-cloud communication before building a therapy solution. Ypsomed offers YDS SmartServices (Figure 5) that reflect a medical-grade device-to-cloud IoT backbone. This device management solution securely and seamlessly provides relevant injection data to therapy solution providers, CROs, and other third-parties.
With SmartPilot and YDS SmartServices, Ypsomed has built a device and a full device management solution that allows pharma customers to develop therapies and services rapidly that address non-adherence in clinical trials and commercially.
OUTLOOK
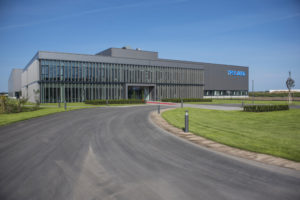
Figure 6: Ypsomed’s newest manufacturing site in northern Germany meets future demand and provides risk mitigation for YpsoMate and other Ypsomed platform products.
YpsoMate has been approved in combination with five drugs to date, including Mylan’s biosimilar Hulio® (adalimumab), Teva’s Copaxone® (glatiramer acetate) and Amag’s Vyleesi® (bremelanotide). A number of further launches are imminent, including the first YpsoMate 2.25 customised devices.
The capacity growth for YpsoMate autoinjectors is supported by the new Ypsomed manufacturing facility in Germany (Figure 6), which came on stream in Q3 2019.
Originator drug molecules dominate the YpsoMate customer portfolio reinforcing the technology’s competitive edge for patients and pharma customers alike. The Ypsomed platform portfolio continues to grow as we move into the second decade of the custom product journey, with the development of the new prefilled, connected, large-volume patch injector YpsoDose, in addition to the SmartPilot connected add-on for YpsoMate 1.0 mL and YpsoMate 2.25 devices.
Ypsomed’s smart device solutions strive to transform patients’ lives by capturing therapy-relevant injection data and processing them to facilitate the self-management of chronic diseases.