To Issue 161
Citation: Comer I, Murph A, Pratt J, “Targeting Nitrosamine Precursors with Novel Active Material Science Scavenger Technologies”. ONdrugDelivery, Issue 161 (May/Jun 2024), pp 12–16.
Ivy Comer, Amanda Murph and Jason Pratt, discuss the challenges in combatting N-nitrosamine formation in oral solid dosage forms, and present Aptar CSP Technologies’ 3-Phase Activ-Polymer technology as a novel packaging-based solution.
N-nitrosamine or nitrosamine drug substance-related impurities (NDSRIs) are a class of potentially carcinogenic compounds that have been wreaking havoc on the pharmaceutical industry, leading to product recalls and heightened regulatory scrutiny of both commercialised and in-development drugs. Nitrosamines are found as impurities in various drug products, and studies show that, over time, nitrosamine formation levels can grow beyond the US FDA’s daily thresholds, potentially putting patients at risk.
“Controlling the presence of nitrosating agents and their interaction
with precursors is crucial in mitigating nitrosamine formation.”
Nitrosamines are substances that can form under certain conditions through a process known as nitrosation, especially in the presence of nitrosating agents such as nitrite salts, alkyl nitrites, nitrogen oxides (NOx), nitrosyl halides, nitrosonium salts and nitro compounds, along with amines or amides. Nitrosating agents can arise from the use of recycled solvents or reusing catalysts across different processes or manufacturing lines with inadequate control and inappropriate monitoring. They can also be generated from impure starting materials or intermediates in the upstream step or from the carry-over of other manufacturing processes along the same production line.
Another key variable in nitrosamine formation is the nitrite levels in many of the most commonly used excipients – for example, magnesium stearate and microcrystalline cellulose (MCC) can average 2,000–3,000 ppb levels of nitrites, aiding in nitrosamine-forming reactions.
“The mechanism of reaction and root cause of nitrosamine formation is not always fully understood, complicating the process of finding an adequate risk-mitigation strategy.”
Controlling the presence of nitrosating agents and their interaction with precursors is crucial in mitigating nitrosamine formation. Aptar CSP Technologies has conducted a series of studies1 that explores the possibility of leveraging innovative active material science technologies to develop a novel nitrosamine-mitigating solution for oral solid dosage forms. The branch of the study presented here focuses on the role that nitrites in excipients play in nitrosamine formation (Box 1). It also investigates how Aptar CSP Technologies’ proprietary Activ-Polymer™ platform technology can mitigate the risk associated with MCC. The data presented explore whether nitrite impurity levels contained in a sample lot of placebo MCC tablets can be meaningfully reduced when placed together with Aptar CSP’s Activ-Film™ material in a sealed environment.
BOX 1: THE IDEA IN BRIEF
The Problem
Pharma companies are facing increasing regulatory scrutiny and higher risk of product recalls due to N-nitrosamines and NDSRIs in drug products. The mechanism of reaction and root cause of nitrosamine formation is not always understood, which makes mitigating this risk difficult.
The Challenge
The current mitigation strategies employed by pharma developers, such as making changes to their formulation or manufacturing processes, can be costly. Additionally, it is difficult to control the variables associated with N-nitrosamine formation with any certainty. Additional or alternative mitigation strategies may need to be considered to fully address the risk.
The Solution
New innovations in active material science technologies can offer an active packaging-based solution that can react with NOx gases in the packaging headspace to inhibit nitrosamine formation. Not only can these technologies stop nitrosamine formation, but they can serve as an additional “insurance policy” by adsorbing or scavenging N-nitrosamines post-formation, providing a holistic risk mitigation solution.
MITIGATING NITROSAMINE RISKS ASSOCIATED WITH EXCIPIENTS
Oral drug formulations typically involve a blend or granulation of their APIs with various excipients, many of which have been shown to include nitrite impurities at trace levels. According to Boetzel et al, the excipients, such as fillers and diluents, have the greatest influence over the nitrite concentration.2 MCC is an extremely common diluent in oral solid dosage forms, particularly tablets and capsules, and has the highest number of results in Lhasa Limited’s (Leeds, UK) “Nitrite in Excipients” database at 0.04–2.4 ppm. These nitrites can form nitrosating species, such as nitrous acid and various volatile NOx compounds, especially under moderately acidic conditions. For APIs at risk of nitrosamine formation, the presence of nitrosating species in the excipients used in the formulation has been shown to directly increase the rate of formation of nitrosamines.
As pharmaceutical developers seek to assess and mitigate the risk of N-nitrosamine formation in their current drug products and in-development APIs, they have employed strategies such as using nitrocellulose-free packaging or choosing alternate or supplemental excipients, reagents or catalysts. However, these solutions are not infallible, as companies may not always be able to source low- or no-nitrite excipients, and these strategies can result in over formulation, which could potentially lead to new problems.
Additionally, the mechanism of reaction and root cause of nitrosamine formation is not always fully understood, complicating the process of finding an adequate risk-mitigation strategy. Aptar CSP’s challenge as an active material science company is to provide pharma companies with an active packaging-based solution to prevent nitrosamine formation and/or remove nitrosamine impurities post-formation at the point of packaging, reducing the need for changes to formulation or manufacturing processes. The technology could be used as a primary solution or as an additional measure of protection to complement other strategies used to prevent N-nitrosamine formation.
INNOVATIONS IN ACTIVE MATERIAL SCIENCE TECHNOLOGIES
Nitrites are known to form volatile, gaseous NOx components, especially through protonation under mildly acidic conditions.3 In the absence of any additional reactions, such gases will come to an equilibrium in the environment. However, by removing the NOx from the environment, the equilibrium reaction will drive the formation of additional NOx gases that, if removed, will continue until the trace levels of nitrite are consumed.
New innovations in active material science technologies can offer an active packaging-based solution that can react with NOx gases in the packaging headspace to inhibit nitrosamine formation. Leveraging over 20 years of material science expertise, Aptar CSP Technologies’ 3-Phase Activ-Polymer™ platform technology is delivered in a unique formulation comprised of a base majority polymer that provides the structure, a channelling agent and active particles (Figure 1). The channelling agent coats and distributes active particles throughout the polymer matrix and allows targeted molecules to enter through the hydrophilic channels. Those molecules migrate to the active particles, where they are adsorbed and permanently removed from the headspace.
Figure 1: Video, Aptar CSP’s 3-Phase Activ-Polymer™ technology matrix.
For the purposes of this study, the technology, deployed as an Activ-Film™ material sealed together with MCC tablets, was engineered to quickly and efficiently capture and/or react away the volatile NOx species, thus preventing the formation of nitrosamines by removing the nitrosating agent (Figure 2). This technology is called N-Sorb (Figure 3).

Figure 2: How N-Sorb can prevent nitrosamine formation.4
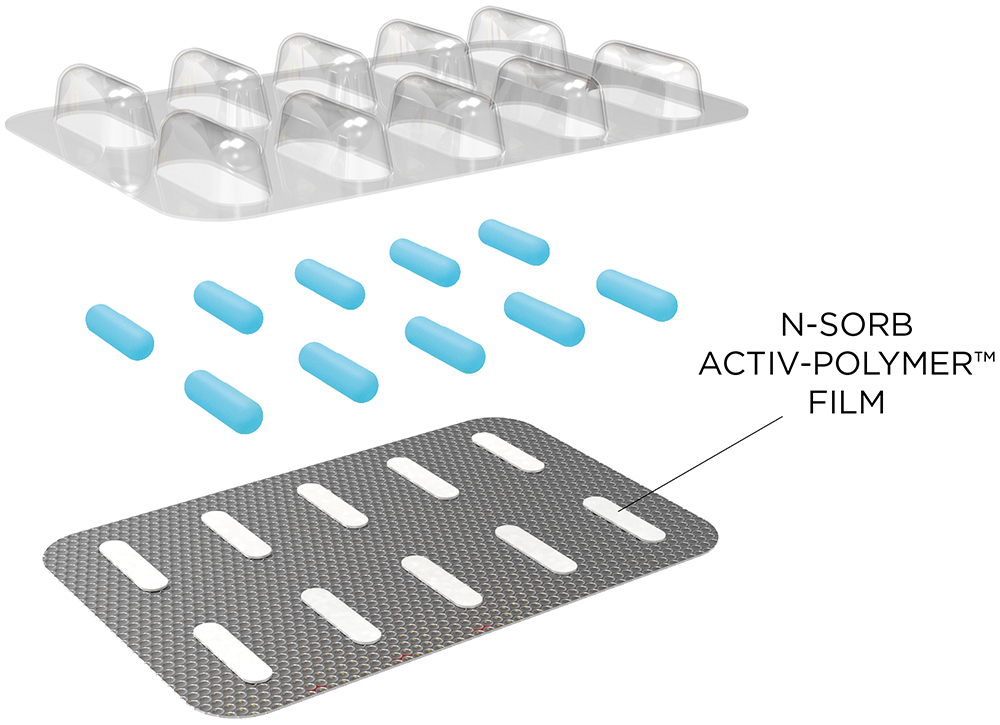
Figure 3: Example deployment of N-Sorb Activ-Polymer™ film sealed in an Activ-Blister™ configuration with tablets.
N-SORB STUDIES
In one study, four versions of N-Sorb mitigation films were exposed to MCC tablets in sealed foil bags during a six-day ageing period. The methodology5 used for the experiment was based on a chemical derivative method that reacts with all available nitrites directly into a measurable compound. The compound was detected and quantified using a gas chromatography-mass spectroscopy headspace, with a detection ranging from 5 to 100 ppm. The instrumentation specifications for the experiment were:
- Agilent GC 8890, Model Number G3542A
- Agilent MSD 5977, Model Number G7077C
- Agilent Headspace 8697, Model Number G4511A.
“After six days of ageing at 60°C in an oven, the samples containing the MCC and either N-Sorb 20 or N-Sorb 23 mitigation film had the lowest level of nitrite concentration remaining in the headspace.”
All four versions of the N-Sorb mitigation film significantly reduced the average levels of nitrite present in the samples compared with the controls. None of the mitigant’s range of concentration overlapped or extended into the control concentration, indicating that nitrite levels were significantly reduced after ageing. After six days of ageing at 60°C in an oven, the samples containing the MCC and either N-Sorb 20 or N-Sorb 23 mitigation film had the lowest level of nitrite concentration remaining in the headspace (Figure 4).
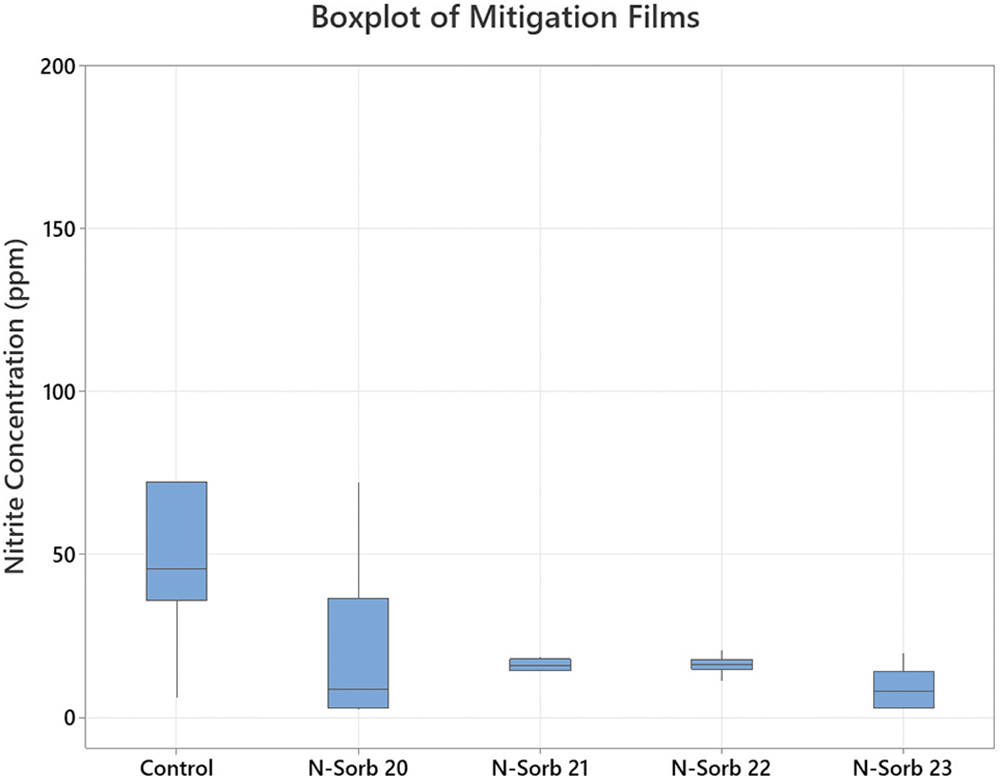
Figure 4: Nitrite concentration (ppm) versus N-Sorb mitigation films sealed with MCC tablets.
Nitrite was reduced by all N-Sorb mitigation films tested with MCC tablet samples during the ageing period compared with the amount measured in the control samples (Figure 5). All the mitigation films exhibited a reduction of ~70% or more compared with the amount measured in the control sample. MCC tablet samples exposed to the N-Sorb 23 mitigation film during the test period resulted in the highest reduction of nitrite concentration, along with the lowest variation of the top two mitigation film performers, as illustrated by Figures 4 and 5.
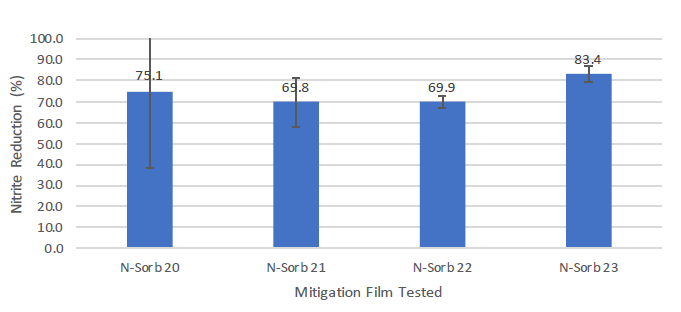
Figure 5: Percentage reduction of nitrites in MCC tablets sealed with N-Sorb mitigation films when compared with control sample.
“Aptar CSP Technologies’ innovative Activ-Polymer™ platform with its N-Sorb technology offers pharmaceutical developers a promising alternative to current nitrosamine mitigation strategies.”
CONCLUSION
Aptar CSP Technologies’ innovative Activ-Polymer™ platform with its N-Sorb technology offers pharmaceutical developers a promising alternative to current nitrosamine mitigation strategies by actively removing nitrosamines from the headspace of sealed drug packaging. The key findings from this study demonstrate the potential of N-Sorb as a potent scavenger of nitrite precursors:
- Significant Nitrite Reduction: All tested N-Sorb mitigation films significantly reduced nitrite levels in the headspace compared with controls, with reductions exceeding 70% in some cases.
- Efficient Capture: N-Sorb 23 exhibited the highest nitrite reduction and lowest variation, demonstrating its efficacy in capturing and/or reacting with the volatile NOx species responsible for nitrosamine formation.
- Post-Formation Mitigation Potential: While the study focused on preventing nitrosamine formation, the technology’s ability to capture nitrite supports its potential efficacy for reducing existing NDSRIs in packaged drugs.
For drug formulation and analytical scientists, N-Sorb presents a compelling solution offering several advantages:
- Targeted Intervention: N-Sorb specifically addresses the root cause of nitrosamine formation – the presence of nitrosating agents, such as NOx gases – without requiring extensive formulation changes.
- Simplicity and Ease of Integration: N-Sorb can be seamlessly integrated into existing packaging formats and processes, minimising disruption to manufacturing workflows.
- Flexibility and Potential for Broad Applicability: The modular design of Activ-Polymer™ technology allows for customisation to suit specific drug product requirements and target various nitrosating agents beyond NOx gases.
While further research is warranted to fully validate the long-term effectiveness and compatibility of N-Sorb with diverse drug products, this study provides a strong foundation for its potential as a game changer in the fight against NDSRIs. By offering a targeted, efficient and easily implementable solution, N-Sorb can empower drug developers to ensure the safety and quality of their products while streamlining compliance with regulatory requirements.
To find our more about the oral solid dose offering from Aptar CSP Technologies, visit: csptechnologies.com/markets-served/oral-solid-dose.
ACKNOWLEDGEMENTS
The authors would like to acknowledge Jean Daou, PhD, R&D Manager, and Madison Pipkin, Project Manager, both at Aptar CSP Technologies, for their contributions to the work presented in this article.
REFERENCES
- Baertschi S, Daou J, Pratt J, “Mitigating N-Nitrosamine Risks with Novel Active Material Science Innovations”. White Paper, Aptar CSP Technologies, May 2023.
- Boetzel R et al, “A Nitrite Excipient Database: A Useful Tool to Support N-Nitrosamine Risk Assessments for Drug Products”. J Pharm Sci, 2023, Vol 112(6), pp 1615–1624.
- Sluggett GW, “Artifactual degradation of secondary amine-containing drugs during accelerated stability testing when saturated sodium nitrite solutions are used for humidity control”. J Pharm Biomed Anal, 2018, Vol 149, pp 206–213.
- Carloni L-E et al, “Solid State Kinetics of Nitrosation Using Native Sources of Nitrite”. J Pharm Sci, 2023, Vol 112(5), pp 1324–1332.
- Zhang S-X et al, “A high-throughput headspace gas chromatographic technique for the determination of nitrite content in water samples”. J Chromatogr A, 2018, Vol 1538, pp 104–107.