To Issue 172
Citation: Glotzbach M L, Moakes G,”The Power of Partnership and Close Collaboration for Filling On-Body Injectors”. ONdrugDelivery, Issue 172 (May 2025), pp 20–23.
Mary Lou Glotzbach and Dr Greg Moakes consider the implications of the increasing demand for high-volume injections across the drug delivery industry, and how technologies such as wearable injectors are creating novel challenges for the fill-finish process due to the novel containers involved, making the case that it is only through clear communication and close collaboration between partners that these challenges can be met and surmounted.
A key frontier in today’s drug delivery industry is biological therapeutics. These medicines hold great potential to treat indications previously out of reach and provide much needed treatment for multiple patient demographics. As a result, biologics now represent a major part of the drug delivery market and pharmaceutical pipeline, with drug formulators keen to capitalise on these medications and get patients the treatment they require.
However, biologics are notoriously difficult to deliver. The large proteins that comprise biologic therapeutics are fragile and prone to denature or agglomerate under adverse conditions, meaning that successfully storing and delivering them to patients is proving to be an ongoing challenge with no hard-and-fast solution. While many different approaches are in development, the broad consensus is that the injectable route is favourable for most biologics, as they tend towards liquid formulations and are prone to lose their therapeutic effectiveness if exposed to the gastrointestinal tract.
“WHILE SOME DEVELOPERS ARE INVESTIGATING THE BOUNDARIES OF PATIENT TOLERANCE WITH AUTOINJECTORS, OTHERS ARE PIONEERING A NEW APPROACH – OBIs.”
Injecting biologics is, of course, not without its own challenges. The large molecules lead to biologic formulations either being significantly more viscous than traditional small-molecule therapeutics or needing to be delivered in significantly higher volumes. While efforts have been made to deliver biologics with traditional autoinjectors, compromises have had to be made, either in injection time, needle gauge, increased volume or a combination of the three. However, while some developers are investigating the boundaries of patient tolerance with autoinjectors, others are pioneering a new approach – on-body injectors (OBIs).
THE DEMAND FOR LARGE-VOLUME INJECTIONS
A number of companies across the industry have dedicated significant resources to the development of OBIs, however, entrenched scepticism remains towards OBIs and the concept of large-volume injection more broadly. This is not unexpected, as the strict regulations surrounding pharma products naturally leads to a conservative mindset and a strong preference for established technology – formulators and regulators understand and trust autoinjectors, which is why efforts are ongoing to push the technology beyond its usual 1 mL and 2.25 mL standards into the realm of 5 mL autoinjectors.
When trying to push autoinjector technology to larger volumes, a number of challenges arise. A critical one has proven to be injection time – when using an autoinjector, the patient must hold the device at the injection site for the full duration of the injection, which is significantly longer than suggested limits for a 5 mL injection. While studies have demonstrated that patients are willing to hold an autoinjector in place for longer injections, 5 mL formulations of biologics are often viscous, presenting yet further challenges to autoinjector-based delivery.
THE POTENTIAL OF WEARABLE INJECTORS
This has led to the development of OBIs such as LTS’s Sorrel platform. These devices represent an alternative path to solving the challenge of delivering biologics. As OBIs are worn on the body, holding an autoinjector in place ceases to be a consideration, which means injection times can be significantly longer and injections more comfortable for the patient. Furthermore, OBIs can handle volumes even greater than 5 mL, with some pushing up to 20 mL or more, unshackling formulators from the need to force their biologics into ill-suited established formats.
This is a critical factor in the modern drug delivery industry due to its intersection with another key trend – the drive to move care from the hospital to the home. Due to a wide array of factors, from ageing populations to sustainability concerns, healthcare systems across the world are under ever-increasing pressure. A key approach to alleviate this pressure is to facilitate patient self-administration at home, which both reduces the pressure on clinic hours and provides patients with greater agency over their own lives.
To achieve this paradigm shift in the way care is delivered, the issue of adherence must be addressed – for at-home treatment to be successful, patients must be able and willing to self-administer their medications successfully. This has required the drug delivery industry to adopt a mentality of patient-centricity in its design focus, putting the patient at the centre of its decision-making. OBIs are a key part of this, presenting a simple and effective treatment method for patients to self-administer complex, high-volume biologics that interferes with their daily lives as little as possible.
“AS IT EVOLVES, OBI DEVELOPMENT IS CONTINUING TO ACCOUNT FOR THE NEEDS OF FORMULATION DEVELOPERS, PATIENTS AND OTHER STAKEHOLDERS, WHICH HAS LED TO A VERSATILE PLATFORM APPROACH EMERGING AS A TREND.”
However, OBIs come with their own design challenges. Given their relative novelty in the industry, there are currently no standards or conventions for their design, so device developers have taken often wildly different approaches to designing these complex devices, from form factor to drive mechanism to primary container (Figure 1). As it evolves, OBI development is continuing to account for the needs of formulation developers, patients and other stakeholders, which has led to a versatile platform approach emerging as a trend.
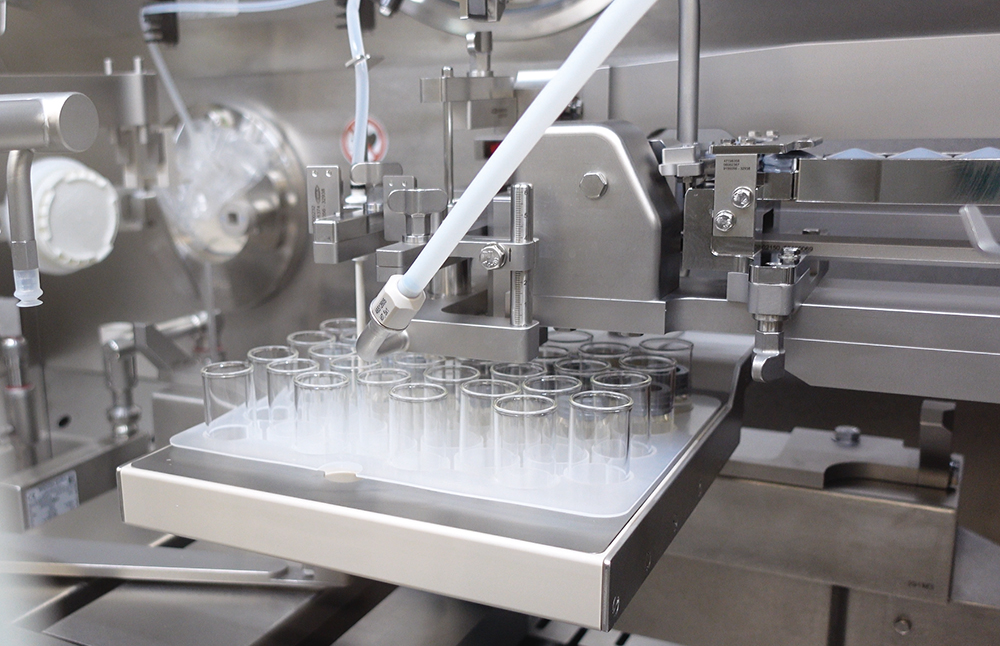
Figure 1: Grand River Aseptic Manufacturing cartridge filling for custom drug delivery innovations.
Versatility is a key feature of the Sorrel platform, with the device able to accommodate a range of volumes in either a vial or cartridge format. LTS is able to adapt the core chassis to fit the primary container that best suits the formulation in question and then tailor the injection profile using Sorrel’s onboard electromechanical drive. This represents an excellent solution for LTS and its pharma partners, but presents a new challenge all of its own – with such a variety of primary containers available, how are they filled?
THE CHALLENGES OF FILLING NOVEL CONTAINERS
Fill/finish is a critical part of manufacturing any injectable product and one that requires specialist equipment and know-how. Grand River Aseptic Manufacturing (GRAM) is an expert in this field, with extensive experience in ensuring safety and quality when filling pharmaceutical products. The rise of biologics and shift towards patient self administration has created challenges not only for device developers, but across the industry, including for fill/finish experts (Figure 2).
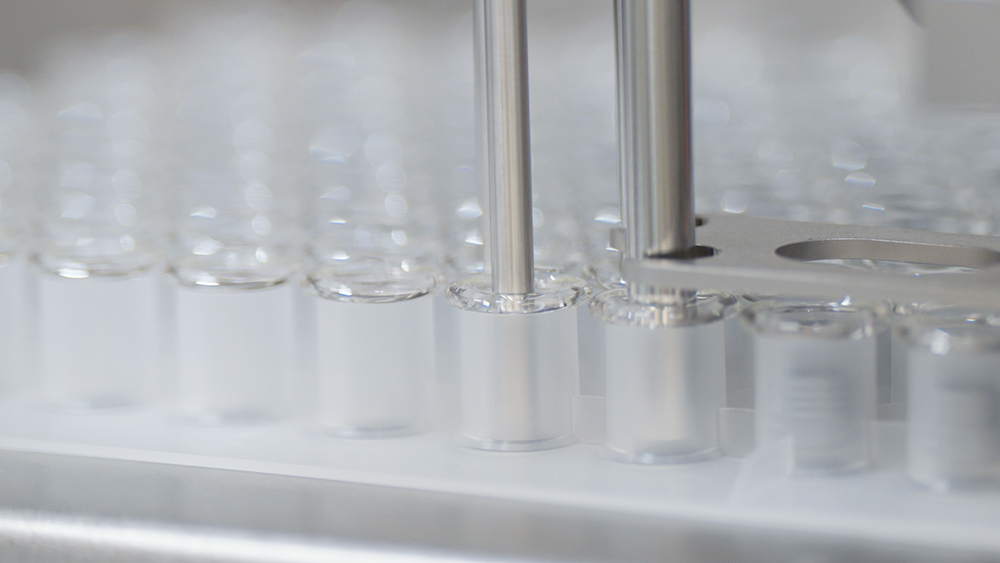
Figure 2: Grand River Aseptic Manufacturing prefilled syringe and cartridge filling inserting stoppers.
Large-volume injectables, and OBIs in particular, have required fill/finish experts to step up. For more traditional injectables, such as vials and 1 mL long syringes, there are long-established industry standards for their dimensions. So, in tandem, filling lines have been adapted to accommodate these primary container formats with minimal friction – the line components are standardised along with the primary containers. However, there are no standards for larger formats, such as 5 mL and 10 mL cartridges or other, even more unusual primary containers used by some OBIs, so fill/finish experts such as GRAM have had to rapidly innovate and adapt to meet the demands of large volume injection devices.
“FOR DEVICES WITH A HIGH DEGREE OF VERSATILITY IN THEIR PRIMARY CONTAINERS, SUCH AS SORREL, FILL/FINISH PARTNERS NEED TO BE ABLE TO MATCH THAT VERSATILITY TO KEEP UP WITH THE RAPID PACE OF DEVELOPMENT IN THIS SECTOR.”
With many OBIs, device developers continue to iterate on their primary containers as their devices evolve in response to the needs of pharma partners and patients. For devices with a high degree of versatility in their primary containers, such as Sorrel, fill/finish partners need to be able to match that versatility to keep up with the rapid pace of development in this sector. With primary containers often being adapted to the needs of individual pharma partners, one 5 mL cartridge may not share dimensions with another, which places even greater demand on the fill/finish expert to be able to deliver top quality products throughout the development and commercialisation journey.
CLEAR COMMUNICATION AND THE POWER OF PARTNERSHIP
Meeting the demands of development and fill/finish for OBIs requires a wealth of expertise and experience from across the value chain. To be able to deliver a safe, efficacious product to patients and healthcare providers and stand up to the rigorous requirements of regulators, partners in this endeavour must engage in open and frank communication with each other. Inefficient or inaccurate communication can only lead to delays and unnecessary errors in the development process, which all parties should be eager to avoid.
An ideal example of this principle in action is the partnership forged between GRAM and LTS to deliver Sorrel OBIs to patients. In the process of partnering with GRAM to provide fill/finish services for its Sorrel device, LTS was sure to engage early in the process and foster trust through clear and open discussions around Sorrel’s specifications and requirements. In doing so, GRAM and LTS have been able to keep up momentum throughout the development process, adapting to evolving needs and ensuring quality at all stages, thereby securing a position at the forefront of the OBI market.
“THROUGH FREQUENT AND TRANSPARENT COMMUNICATION AND ENGAGING EARLY ON IN THE DEVELOPMENT PROCESS, GRAM AND LTS HAVE MANAGED TO CIRCUMVENT SEVERAL ROADBLOCKS AND ISSUES BEFORE THEY AROSE.”
Through frequent and transparent communication and engaging early on in the development process, GRAM and LTS have managed to circumvent several roadblocks and issues before they arose. Close collaboration has enabled the companies to combine their experience and expertise across device development, fill/finish and the supply chain to maximise Sorrel’s competitive advantage and improve what Sorrel can offer to pharma partners.
Working together so closely has been possible for GRAM and LTS due to both companies sharing an understanding of the needs of the modern drug delivery industry; patient centricity and the culture that surrounds it is no longer only a concern for human factors specialists, it must be integrated into all aspects of the value chain. Clear communication has been key for ensuring that GRAM and LTS’s values align and that the companies are working towards the same goal – better outcomes for patients.
CONCLUSION
The demand for large-volume injectors to meet the needs of novel biologic therapeutics is undeniable. As such, the drug delivery industry must rise to the challenges presented by these molecules and the needs of the healthcare sector so that patients can self-administer these life-changing medications. A key aspect of meeting this goal will be OBIs capable of delivering much larger volumes than traditional syringe-based injection devices in a patient-centric fashion. Novel large-volume devices also require an adaptive and innovative approach from fill/finish experts, who must meet the demands of filling primary containers in a fast-moving section of the industry with no established standards.
If this challenge is to be met, it will require close collaboration between partners across the value chain and a willingness to engage in open and frank communication to foster trust and co-operation. GRAM and LTS have achieved this with the Sorrel OBI, building up momentum in a rapidly evolving sector to offer pharma partners a versatile and adaptable OBI offering complete with fill/finish capacity. This collaboration enables GRAM and LTS to position Sorrel as a leading device in the OBI market and will allow patients to self-administer their biologics in a safe and effective manner, progressing healthcare towards a more patient-centric future.