Citation: Schopferer B, “Z.Blizzard Automation System – It Doesn’t Get More Tailor-Made Than This”. ONdrugDelivery Magazine, Issue 99 (Aug 2019), pp 60-62.
Berthold Schopferer explains how Zahoransky’s integrated syringe manufacturing and assembly equipment allows maximum customisation and full customer involvement.
“Just because something works in the laboratory does not necessarily mean it will work in an industrial environment.”
Customisation, an aspect valued so highly by consumers when it comes to coffee or specially made muesli, and standard practice in the auto industry, has now also become firmly established in the world of mechanical engineering with the mould and machine engineering specialist ZAHORANSKY Automation & Molds. We can build our systems in series in different versions, greatly adapted to each specific customer. We implement the modularity that is both desired and required on a one-to-one basis – naturally based on the principle that our customers’ products will meet the high quality requirements that are not just promised but demanded in the medical technology sector. This is because we want and need to ensure that our systems pose no risk whatsoever to the product or a person’s health.
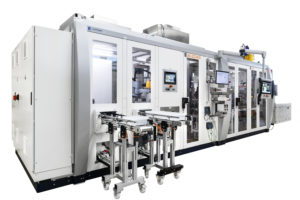
Figure 1: The Z.BLIZZARD produces ready-to-fill staked-needle syringes from COC/COP polymers with a very high autonomy time.
THE CUSTOMER’S ROLE IN THE DEVELOPMENT
The following examples of configuration options for the Z.BLIZZARD (shown in Figure 1), an automation system which includes injection moulding, show what is meant by the high degree of customisation of the systems. In current systems, if so desired, more than ten camera systems can ensure continuous monitoring of the product during the manufacturing process, as well as an integrated 100% X-ray system for quality assurance after assembly (Figure 2).
It is virtually impossible to achieve more comprehensive quality assurance based on today’s technology. Nevertheless, maximum machine capability is important as the foundation for achieving high process capability. Our customers also have the advantage that they cansource these options from a single supplier. After all, when it comes to X-ray technology, certain standards and guidelines must be followed, and not everyone has that capability. We have our own specialists in this area, therewith providing the customer with legal and regulatory security.
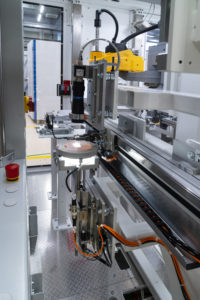
Figure 2: More than ten camera systems can ensure continuous monitoring, as well as an integrated 100% X-ray system for quality assurance after assembly.
The same careful approach also applies to cleanroom modules. Here, ZAHORANSKY uses industry-proven systems to enable our customers’ products to be produced in hygienic conditions. The customer is also involved in many more decisions: How should the bevel be oriented? Should it be straight or bended? Which area should the camera cover? Is integrated X-ray inspection needed? Should the Z.BLIZZARD be equipped with additional access doors? These and other details are worked out in close collaboration with the customer, then implemented in exactly the same way. Customers are involved from an early stage, guiding the entire design and manufacturing process, which usually takes 12 months.
GOOD MANUFACTURING PRACTICE GUARANTEED
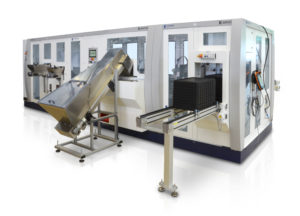
Figure 3: The connected Z.MISTRAL and
Z.LODOS can cover the entire process
chain, from granulates to packaged PFS
Some of our customers bring with them their own knowhow regarding special components or technologies that they need in order to manufacture their final product. Of course, this doesn’t always have to be the case; we are also happy to provide customers with comprehensive advice and recommendations. However, if our customers already have fixed ideas about tried-and-tested modules or technologies, and they want these to be integrated into our systems, we do prove these very carefully in advance. After all, just because something works in the laboratory does not necessarily mean it will work in an industrial environment. Therefore, in some cases we also develop these solutions ready for series production.
It is so important that the customer is closely involved in the development process whenever possible and as much as they wish to be. Whether and how much development work must be carried out with the customer is examined at an early stage of the project and, naturally, follows GMP guidelines.
The customer is provided with evidence to prove that the implementation of the proposed solution will be audit-proof. We must be able to show why something does or doesn’t work. When it comes to machine manufacturers, that is what separates the best from the rest. For us, 100% means 100%. We also think in a future-oriented manner for our customers. That is to say, even after we have delivered and installed a customer’s Z.BLIZZARD system, it is still important to us that they have an innovative and future-proof piece of equipment.
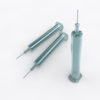
Figure 4: The Z.BLIZZARD
manufactures plastic PFSs
that boast several advantages
over their glass counterparts.
SAME LOOK, DIFFERENT CHALLENGES
The interior of the Z.BLIZZARD is but one opportunity for customisation. If the Z.MISTRAL, which handles downstream processing, and the Z.LODOS palletising system are also connected (Figure 3) the entire process chain, from granulates to packaged COC/COP polymer ready-to-fill staked-needle-syringes (PFS), can be covered with a very long autonomy time. It’s worth mentioning that although most PFS look quite similar and have an identical basic function, each customer brings different challenges and different specifications. Obviously, we have to take these into account when manufacturing the equipment.
ZAHORANSKY customers opt to make their PFS out of plastic (Figure 4). The major advantage here compared with their glass-syringe counterparts is thatthe needle is overmoulded and not fused or glued in. The conditions during the glass syringe’s fusing process, which involves temperatures of more than 1000 °C and materials with high temperature-resistance such as tungsten, cause heavy metals to be released. These heavy metals may migrate into or interact with the glass container and can later also be detected in the product, even though the containers are subsequently washed, dried and sterilised. Moreover, the plastic variety also benefits from a minimised risk of breakage and greater design freedom.
TOP QUALITY
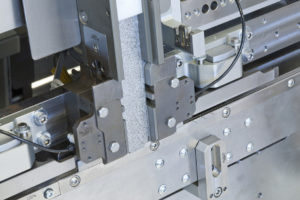
Figure 5: The Z.NFS needle feeding system, which can separate 4-32 needles or cannulas at up to 12 cycles per minute.
The Z.NFS Needle Feeding System (Figures 5 & 6) also guarantees that needles are processed on a “first-in, first-out” basis. The system can be filled with the required quantity of cannulas, which are then used in order for the batch. This prevents the needles from remaining in the system for longer periods. The Z.NFS can separate between four and 32 needles or cannulas at up to 12 cycles per minute; in other words, up to 400 units per minute. It can currently handle needle diameters from 0.2 mm and lengths up to 45 mm. The Z.NFS is also an integrated system and thus guarantees maximum purity in the production process, since there is no human contact and the process is cleanroom compatible. One can hardly imagine higher quality in medical device manufacture or a greater degree of customisation for the producer.
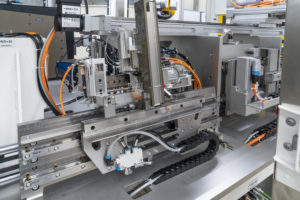
Figure 6: The Z.NFS combined with the Z.BLIZZARD forms an integrated system for a cleanroom compatible process with no human contact.