To Issue 132
Citation: Atkinson N, “How Can the Pharma Industry Prepare for New pMDI Propellants?” ONdrugDelivery, Issue 132 (Apr-May 2022), pp 38–40.
Nick Atkinson looks at the changes that are set to hit pressurised metered dose inhaler manufacturing as new propellants are introduced and how pharma companies can prepare for the switch.
Pressurised metered dose inhalers (pMDIs) are the most frequently prescribed inhaler devices worldwide (Figure 1), enabling patients to manage respiratory conditions such as asthma and chronic obstructive pulmonary disease (COPD).
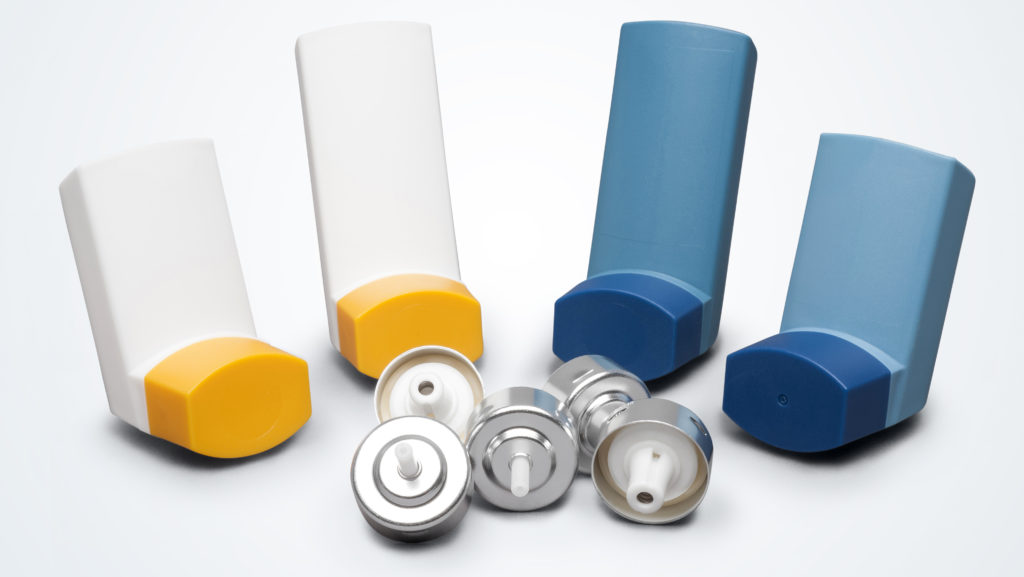
Figure 1: A selection of pMDI actuators and valves.
However, pharmaceutical companies must prepare for new changes that are set to impact the industry as legislation governing the use of pMDI propellants is tightened. Many pMDIs use hydrofluoroalkanes (HFAs) – specifically HFA-134a and HFA- 227ea – as propellants, which are set to be phased out across other industries due to their high global warming potential (GWP) to pave the way for lower-GWP alternatives.
“Pharmaceutical companies must assess the potential risks of new propellants to determine how to safely handle, transport and contain them.”
Although the pharmaceutical industry is currently exempt from the HFA phasedown, their industrial use across other sectors is already on the decline. As a result, these propellants will become more difficult and costly to acquire.
This transition is likely to present challenges to pharmaceutical companies, as next-generation low-GWP propellants can potentially impact formulation requirements, valve design and manufacturing equipment. As such, companies must prepare their manufacturing environments and processes for the introduction of new low-GWP propellants for pMDIs in the near future.
Pharmaceutical companies must assess the potential risks of new propellants to determine how to safely handle, transport and contain them. This leads to one of the main challenges that manufacturers must overcome with the introduction of new propellants: working with flammable gases. This article will explore flammability challenges and how pharma companies can prepare their pMDI manufacturing environments to safely handle new propellants.
TACKLING FLAMMABILITY CONCERNS
There are two potentially sustainable propellant candidates currently under consideration with lower GWP levels than HFA-134a (which has a GWP of 1,430) and HFA-227ea (which has a GWP of 3,220):
- 1,1-difluoroethane (HFA-152a): GWP of 124
- 1,3,3,3-tetrafluoropropene (HFO-1234ze(E)): GWP of less than 1.
Under certain conditions, HFA-152a and HFO-1234ze(E) have been classified as flammable and mildly flammable, respectively, which means that production of pMDIs using them will require pharmaceutical companies to develop a deep understanding of the safety controls that must be implemented across their processes.
When working with flammable aerosol propellants, fire or explosion risks must be carefully considered. At a basic level, there must be fuel, oxygen and an ignition source present for a fire to occur. Regardless of the propellant that is used, it is imperative that pharmaceutical companies assess the risk and prepare their processes and environments to prevent scenarios where a fire or explosion could occur.
“Reducing the risk of working with flammable propellants requires manufacturers to carefully consider their cleanroom environments.”
WHAT ARE THE RISKS ASSOCIATED WITH FLAMMABLE PROPELLANTS?
There are a number of potential risks related to the handling, storage and transportation of pMDI propellants. Typically, a mixing vessel containing the propellant, API and any excipients is required to manufacture a given pMDI formulation. Before pMDIs can be filled, mixing must take place within a sealed manufacturing system.
It is crucial that steps are taken to prevent the propellant escaping the vessels and pipework. However, if this does happen, under the right conditions there is an increased risk of propellant (fuel), oxygen and an ignition source coming together to create a fire or explosion. The risk of an undetected leak taking place must be mitigated against, as this could result in a catastrophic event, given the potential volume of propellant in the manufacturing system.
Propellants must also be properly stored in an area where they cannot come into contact with a heat source, as the overheating of storage vessels could cause aerosol expansion and possibly result in a boiling liquid expanding vapour explosion (BLEVE). Controls must be implemented that aim to prevent overheating of flammable aerosols during storage and bulk transport.
“Preparing manufacturing environments as soon as possible for the changes that new, more sustainable propellants will bring is key to ensuring the safe development and delivery of inhalable drugs.”
REDUCING RISK IN A GMP MANUFACTURING ENVIRONMENT
GMP manufacturing requires rigorous cleaning and inspection measures across each process, which can heighten the risk of a leak occurring. High levels of intervention across cleaning, inspections, product changeovers, connections with mobile equipment (e.g. drug addition vessels) and filter changes will, in turn, heighten the risk of a leak.
There are a number of measures that can be taken to reduce this risk in a GMP manufacturing environment. As set out in Regulation 6 of the Dangerous Substances and Explosive Atmospheres Regulations (DSEAR) – the UK implementation of the EU ATEX Workplace Directive – the steps that should be taken to minimise risk include the following:
Reduce Quantity – Compartmentalising
Manufacturers can take steps to segregate and isolate parts of their manufacturing system to minimise the quantity of the dangerous substance in one place, with isolation valves being an effective method.
Preventing Releases – Gas Detection Systems
Equipment must be appropriately designed and engineered to prevent leaks. Integrity of the manufacturing system can be confirmed following intervention by pressure testing. If a leak were to occur, gas detection systems can be used to monitor the concentration of a flammable substance in the atmosphere, and can be linked to isolation valves to minimise further leakage.
Control Ignition Sources – Classification
Manufacturers must also ensure that any hazardous areas are classified, and that all equipment is rated appropriately to minimise the risk of ignition.
Mitigation – Damage-Limiting Construction
Damage-limiting construction (DLC) can be used to mitigate the detrimental effects of a vapour cloud explosion (deflagration) and limit its impact to within the enclosure.
Instruction – Ensuring User Competence
Accurate instruction is necessary to ensure that any risk is safely contained, removed to a safe place or otherwise rendered safe. Operators must also possess the skills, knowledge, training and ability to safely conduct their operations.
Determining Necessary Levels of Hazard Control
If the hazardous substances cannot be eliminated, there must be measures in place to minimise risk. This typically requires several independent “layers” of protection, and the potential shortcomings of each layer of protection must be carefully evaluated.
CLEANROOM CONSIDERATIONS
Reducing the risk of working with flammable propellants requires manufacturers to carefully consider their cleanroom environments. The formulation, mixing and filling activities required for pMDI projects should be performed in an ISO 8-grade cleanroom (Grade D). This environment must be designed for accessible and easy cleaning, with no crevices or surfaces for dust and debris to settle. Spaces should also be fitted with air exhaust systems to prevent the formation of a flammable atmosphere when hazardous substances are being handled. The air-change rate must be confirmed as adequate and would typically be higher than that needed to maintain GMP conditions. For areas classed as highly hazardous, manufacturers must ensure that extracted air cannot be recirculated back into the system to avoid redistributing the flammable vapour into other uncontrolled areas.
LOOKING AHEAD
Preparing manufacturing environments as soon as possible for the changes that new, more sustainable propellants will bring is key to ensuring the safe development and delivery of inhalable drugs. While HFA-152a and HFO-1234ze(E) are currently the most promising contenders to replace existing propellants, there is still work to be done to fully assess their flammability risks and implement appropriate engineering controls.
Future-proofing drug supply will require pharmaceutical companies to seek support from a dedicated partner specialising in pMDIs. Choosing a partner, such as Recipharm, that can help them through these changes will allow companies to better understand and adapt faster to the requirements of these new propellants.