To Issue 150
Citation: Keinicke Hansen M, “How a Flexible Approach to Autoinjector Assembly Equipment Can Deliver a Competitive Advantage.” ONdrugDelivery, Issue 150 (Jul 2023), pp 36–38.
Mads Keinicke Hansen presents an overview of Stevanato Group’s Standard Autoinjector Assembly Machine platform, providing an in-depth examination of its key features and advantages to illustrate how it is transforming autoinjector assembly processes in the pharmaceutical industry.
“The Standard Autoinjector Assembly Machine platform is designed to support a wide range of popular autoinjector device platforms, including 1.0 and 2.25 mL.”
Whether managing a chronic condition or dealing urgently with a life-threatening allergic reaction, patients today play an increasingly central role in their own medical care through the self-administration of essential drugs.
By enabling patients to take drug delivery into their own hands, technologies such as autoinjectors are key facilitators of this shift, and innovation in this space means the range of devices on the market continues to expand in terms of specification and application. From a manufacturing perspective, capitalising on new autoinjector opportunities relies not only on high-precision engineering capabilities but also having the agility and flexibility to answer increasingly diverse production requirements at speed and minimal cost. To address these needs, Stevanato Group introduced the revolutionary Standard Autoinjector Assembly Machine platform that, through its cutting-edge design, delivers a more versatile and scalable approach to efficient autoinjector assembly.
FLEXIBILITY AND SCALABILITY TO SUPPORT AUTOINJECTOR FORMATS
Flexibility and scalability are at the heart of the Standard Autoinjector Assembly Machine platform, which has been designed for seamless future expansion of production capacity through the addition of new equipment to existing process modules. This feature provides users with the freedom to scale up their operations as needed without completely overhauling the assembly line at each iteration. The platform also provides support for collaborative in/outfeed robots that can assist manual operators by automating the transportation of products from pallets to in/outfeed modules.
The Standard Autoinjector Assembly Machine platform is designed to support a wide range of popular autoinjector device platforms, including 1.0 and 2.25 mL. By using a single, versatile assembly line for multiple autoinjector device platforms, manufacturers can streamline their production process, reduce costs and optimise efficiency.
STANDARDISATION FOR FASTER AND MORE EFFECTIVE PROJECT EXECUTION
By embracing standardisation, the Standard Autoinjector Assembly Machine platform offers faster and more effective project execution compared with fully customised assembly lines. Standardisation eliminates the need for lengthy customisation processes, significantly reducing lead times. It also means that maintenance and repairs can be carried out more efficiently, helping to limit any downtime. In the fast-paced pharmaceutical industry, this ability to accelerate time to market and turnaround time can help manufacturers gain a competitive edge.
The ability to switch between different products swiftly is crucial for pharmaceutical manufacturers seeking to maintain production efficiency. The Standard Autoinjector Assembly Machine platform excels in this aspect, boasting a remarkably fast changeover time. With minimal downtime, manufacturers can transition between autoinjector device platforms seamlessly, maximising productivity and minimising production delays.
To optimise efficiency and use of resources, the Standard Autoinjector Assembly Machine platform enables multiple devices to be assembled on the same line. This innovative feature eliminates the need for separate assembly lines for each autoinjector format, reducing costs and floor space requirements. As a result, manufacturers can achieve higher productivity and economies of scale, ultimately enhancing their competitiveness in the market.
CUSTOMISABLE FEATURES TO ANSWER DIFFERENT MARKET NEEDS
Stevanato Group’s Standard Autoinjector Assembly Machine platform offers the option of in-line laser engraving. This capability allows manufacturers to add essential product identification information, such as branding or batch numbers, directly onto the autoinjector. The in-line laser engraving feature ensures accurate and permanent marking, enabling serialisation on the assembly line and enhancing product traceability and compliance. This is achieved by engraving a 2D barcode onto the device, which enables full product provenance throughout the lifetime of the product. This can be integrated with the company’s data-collection platform for a data-driven, real-time monitoring approach to component traceability. Additionally, an independent laser engraving module can be installed in extension of the labelling module, which provides the ability to engrave customer-specific data onto various label heights, with the machine able to inspect and reject any labels that do not meet quality standards. It also ensures that the labels are accurately applied to the autoinjectors.
In addition to its flexibility in handling multiple autoinjector formats, the Standard Autoinjector Assembly Machine platform is also designed to accommodate various tray sizes for infeed and outfeed. This means the machine can handle different tray sizes without requiring extensive modifications or changes to its set-up, making it easier for operators to switch between different products, saving effort and time.
“By having a dedicated syringe infeed module on the assembly platform, it is possible to verify the syringe on a plethora of parameters and provide local rejection of faulty components before they are assembled with other autoinjector components.”
LINE CLEARANCE AND LINE OPERATOR FRIENDLINESS FOCUS
The machine’s design prioritises operator safety and ease of use, which aims to promote a more comfortable and productive work environment. All assembly machines designed on the BasiQX XTV – Stevanato Group’s flexible platform based on a vertical transport system – have a clear distinction between the production side and the operator side to make line clearance easier. Additionally, the standard autoinjector platform can perform an automatic format-set check on critical points, which enhances productivity and machine safety by preventing collisions and avoiding a potential production stop.
DEDICATED SYRINGE INFEED AND VERIFICATION MODULE
By having a dedicated syringe infeed module on the assembly platform, it is possible to verify the syringe on a plethora of parameters and provide local rejection of faulty components before they are assembled with other autoinjector components. In production, the platform supports the use of multiple syringe formats, with the sole requirement of changing format parts on the infeed module and not on the main assembly line.
The inspections include checks for plunger position, rigid needle shield (RNS) presence, position and alignment, colour code, radio frequency identification, major chips and cracks, and debris on the plunger, as well as cut-flange orientation. The figure above shows an inspection module where the device is inspected for multiple precision factors between assembly sequences. If the configuration does not meet the requirements, the device will be rejected at the end of the assembly sequence (Figure 1).
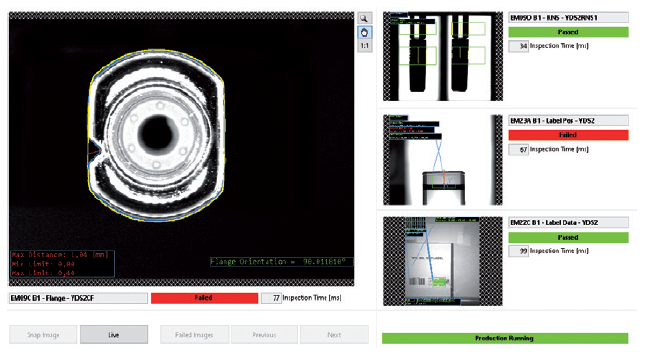
Figure 1: Inspection module with a variety of device verification checks.
PREPARED FOR DIGITALISATION
The platform is designed with high-frequency force and path monitoring systems for assembly verification and data-collection, providing product provenance throughout the lifetime of the autoinjector. The data picked up by these systems can be used for diagnostics through the data-collection smart production interfaces. The green boxes in the high-frequency force distance verification graphs below illustrate the minimum and maximum force for four different checks during the assembly process (Figures 2 & 3).
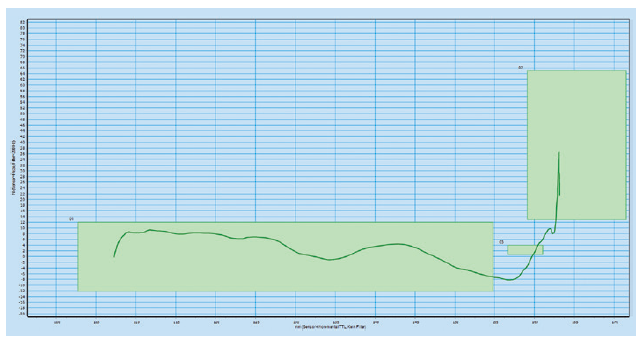
Figure 2: High-frequency force distance verification system where the configuration
meets the requirements.
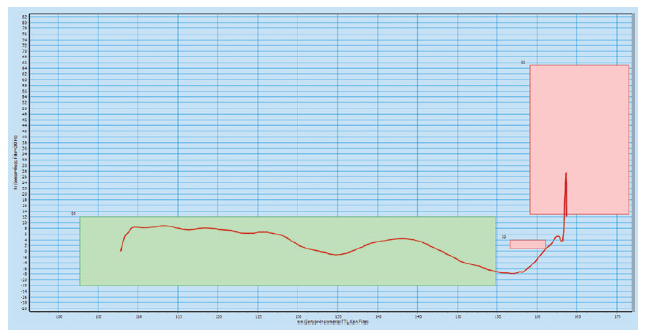
Figure 3: High-frequency force distance verification system where the configuration
does not meet the requirements.
Graphs, such as the ones above, are available for every module of the assembly process that includes a high-frequency force and path monitoring system, and the data is prepared for Stevanato Group’s data-collection platform for a data-driven approach and real-time monitoring.
CONCLUSION
In summary, the Standard Autoinjector Assembly Machine platform is a flexible, scalable and efficient solution for the assembly of a wide range of autoinjector formats. Its standardised design enables faster and more effective project execution compared with fully customised assembly lines, while its modular construction allows for seamless upgrades and modifications to accommodate changing production requirements.
The machine’s fast changeover time, ability to run multiple devices on the same assembly line and optional in-line laser engraving and labelling features further enhance its versatility and suitability for a range of production scenarios. Its focus on operator safety and convenience, as well as its dedicated syringe infeed and verification module, ensure that the finished product is of the highest quality and reliability.
Overall, the Standard Autoinjector Assembly Machine platform is an excellent choice for pharmaceutical manufacturers looking to improve the efficiency, flexibility and quality of their autoinjector assembly process. By investing in this advanced technology, manufacturers can stay ahead of the competition and meet the demands of an ever-changing industry.