To Issue 152
Citation: Hendrawan E, Lu Y-C, Walter C, “An Autoinjector Revolution: Enhanced Global Manufacturing Networks Through Advanced Simulation Technologies”. ONdrugDelivery, Issue 152 (Oct 2023), pp 8–11.
Edwin Hendrawan, Yi-Chi Lu and Christian Walter set out how SHL Medical is building simulation capabilities, and describe how simulation will propel the business forward on every level, from individual shop floors to overall global expansion planning, in order to be able to meet the growing and increasingly complex demands from both pharma customers and patients.
We are witnessing a new global revolution across industries – a universal pursuit of bigger machines, faster production processes and smarter, more connected systems – with the objective of unleashing added value for today’s manufacturing infrastructures. This stride into Industry 4.0 is a pivotal undertaking, significantly transforming the medtech industry landscape.1
“From platform-based manufacturing to modularisation, SHL has already left an indelible mark on the past and is poised to shape the future of autoinjectors.”
A BRIEF LOOK INTO THE RECENT PAST
It should be noted that, prior to Industry 4.0, in medtech, particularly in the field of autoinjectors, a few important landmarks in its relatively short history have given rise to this newfound era.
Autoinjectors commercialised in the late 1990s to early 2000s were characterised by an increasing heterogeneity in their design, development and production requirements. This bespoke approach required varying assets for each project in question.
Moving away from this resource-intensive bespoke model, explorations into the practice of platform design and manufacturing allowed device manufacturers to utilise shared production assets for different device constituents. SHL’s DAI® autoinjector, which features a recognisable industrial design commercialised for various user-group scenarios, is one of the industry’s first such devices.
The platform philosophy in autoinjectors then rose to the next level with the application of modularisation.2 The modularity of platform-based manufacturing can be described by the arrangement of its discrete, standardised modules, enabling companies to benefit from enhanced scalability of production setups.
To this day, the manufacturing infrastructure behind SHL’s Molly® autoinjector remains one of the most successful modular platforms within the industry. The Molly autoinjector has now been commercialised in 17 distinct combination product projects covering a wide range of disease areas.3
MEETING PHARMA’S NEEDS WITH INDUSTRY 4.0
It could be argued that many of the hallmarks of industrialisation in the autoinjector space have been shaped by the efforts of SHL. From platform-based manufacturing to modularisation, SHL has already left an indelible mark on the past and is poised to shape the future of autoinjectors.
The healthcare industry’s advance into Industry 4.0 translates into evolving demands at various points in the value chain. As novel drugs and several biosimilars enter the market in broadening disease areas, pharmaceutical companies seek medical device partners to address growing market demand. This growth – which can be seen on both global and local scales – is characterised by differing healthcare providers, payers, policymakers, and patients.
The portmanteau “glocal” (an adjective combining global and local)4 describes the pressing challenge for pharma to bring combination products closer to local healthcare systems, a challenge in autoinjector combination product development that SHL takes very seriously.
With glocal challenges in pharma requiring glocal solutions, device companies like SHL are investigating strategies to expand manufacturing operations globally by leveraging the power of Industry 4.0 technologies. SHL has proven itself in this regard over the decades, implementing digitalisation of end-to-end processes, in-house automation, machine learning based attention mechanisms in the assembly validation process, deep learning in the robotic systems of testing machines and extensive data analytics for scalable production – the examples are manifold.
In championing its global expansion through Industry 4.0, the next natural step for SHL is to create virtual models of its processes, production lines, machines and supply chains by applying advanced simulation methods and tools.
THE DAWN OF SIMULATION AT SHL
Simulation is a powerful technology that is transforming the manufacturing industry by allowing for the reliable assessment and optimisation of complicated processes. While it might be the case that people are more familiar with the term “digital twins”, both digital twins and simulation utilise virtual representations to reflect objects of varying degrees of complexity. Digital twins arise from libraries of simulated entities. Simulation is advantageous for the examination of one particular process, as well as the dynamic interdependencies between different processes. The capacity to carry out multiple simulation events to study varied conditions – all within a virtual environment – makes simulation a powerful technique to facilitate informed decisions on manufacturing operations and expansion plans.
As part of SHL’s end-to-end digitalisation and global expansion strategies, a dedicated team of plant simulation engineers uses advanced modelling techniques to simulate the processes that go into autoinjector development (Figure 1).
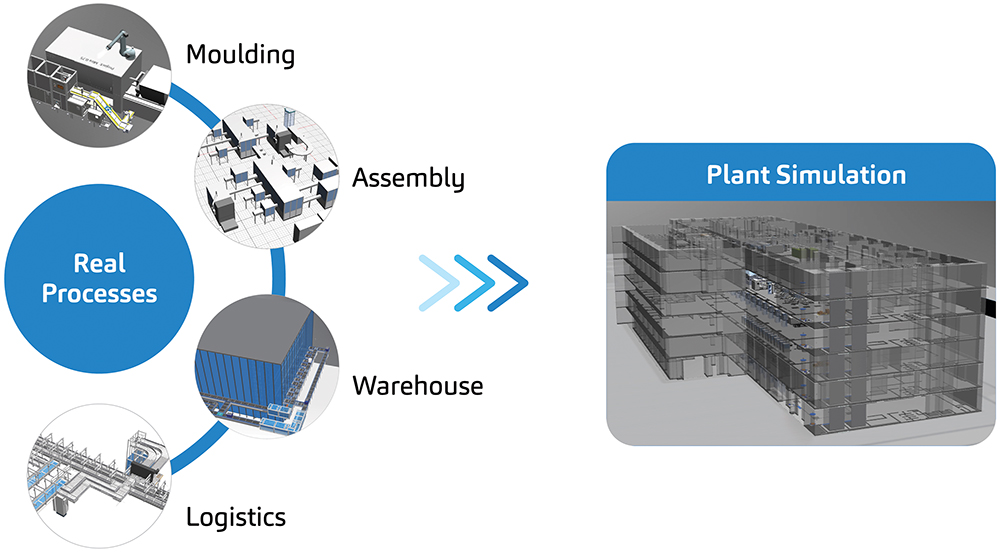
Figure 1: SHL has set up a dedicated plant simulation team to simulate complex processes during autoinjector development, using advanced simulation modelling techniques tailored to SHL’s operations.
“The ability to build simulation expertise in house sets mature device companies apart from other industry players who wish to expand manufacturing operations across continents.”
Simulation technologies perfectly fit the situational needs of the business of autoinjectors, which entails complex processes, physically large objects, well defined supply chains and numerous related system constraints, to name but a few. Likewise, the ability to build simulation expertise in-house sets mature device companies apart from other industry players who wish to expand manufacturing operations across continents.
When seeking to harness the potential of simulation technologies, quite a few essential tools enable adequate computing power in simulation. For instance, SHL uses a combination of simple static models and dynamic simulation modelling – adopting their usage according to the contextual needs of operations and the problem statement’s complexity.
Simple spreadsheet-based models and static modelling are powerful tools to organise data and apply basic formulas to assess and understand specific events. Static modelling is an efficient technique to establish multiple scenarios and produce feasible results for approximation at a high level.
Consequently, the method can eliminate infeasible solutions for a problem being explored. For instance, static calculation allows us to assess production quantities easily, as well as throughputs and space constraints in individual production areas. With the correct input variables, model requirements and conditional formulas, a plant simulation engineer can quickly establish several production settings, define average and worst-case scenarios, and facilitate informed decisions on key parameters of the model setup.
On the other hand, simulation modelling using discrete event simulations (e.g. via Siemens Tecnomatix®) is a highly visual and advanced technique that allows us to build animated representations of highly complex systems and study dynamic interactions of multiple processes and subsystems. Simulation modelling – or plant simulation for the purpose of this article – enables the systematic creation of well-structured and modularised 3D models of SHL’s entire manufacturing infrastructure. More specifically, plant simulation allows the modelling of discrete and continuous manufacturing processes that constitute SHL’s global facilities, specific production processes, material flows and automated machinery.
Managing production capacities across multiple autoinjector platforms is a highly demand-driven process. Plant simulation supports the optimisation of material flow, resource utilisation and various other dimensions of the production operation.
“Plant simulation allows the modelling of discrete and continuous manufacturing processes that constitute SHL’s global facilities, specific production processes, material flows and automated machinery.”
VIRTUAL PLANT SIMULATION IN REAL ACTION
In what ways can one concretely demonstrate the utility of plant simulations? It should be remembered that autoinjector manufacturing entails an architectural hierarchy with dynamic and branching processes. For example, a Molly or DAI autoinjector project for a pharma customer inherits the same pathway from design to production. However, they differ in their specific steps for the same process. Additionally, these projects will also require differing amounts of time to complete the same steps.
For pharma, time-to-market is a crucial requirement in combination product development, which calls for a device partner that offers shorter lead times. For new and existing projects, SHL’s pharma customers benefit from a plant simulation team that dynamically analyses real-time process improvement and optimisation opportunities.
Through an internal request management system, any function can document and investigate optimisation proposals for specific production processes or operational flows. With various production floors utilising SHL’s Fully Automated Assembly Machinery (FAAM), it becomes beneficial to analyse the interactions between the people, the machines and the production layout with an eye to maximising operational efficiency.
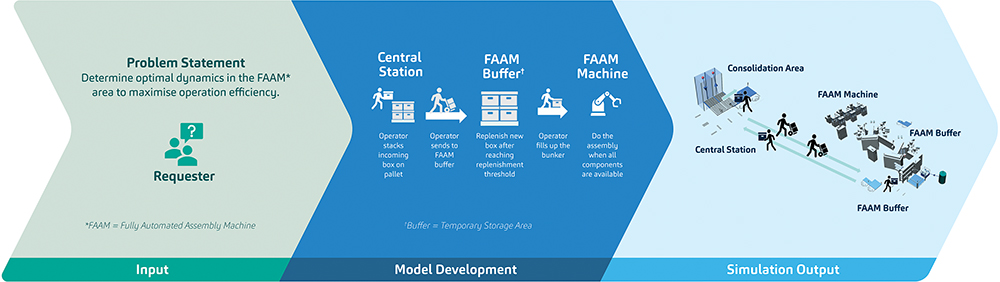
Figure 2: A scenario that mirrors actual situations encountered in SHL’s production lines and how simulation can advance the solution-finding process.
“This ushers SHL’s production lines into continents where many of the world’s leading pharma and biotech companies reside, and epitomises the true essence of 24/7 operations that transcend time zones.”
Figure 2 demonstrates how plant simulation opens pathways for throughput modelling and optimisation. The model shown visualises one of many possible scenarios where initial production components are stacked near the material distribution station, brought to the buffer area, and then sent to the FAAM for the assembly process. In detail, it demonstrates the trade-off between low and high workforce to replenish the materials for the assembly machine. While less workforce assigned to a shop floor can be viewed as an economic positive, it may also impact the overall equipment efficiency for the process in specific scenarios. There is an acceptable balance between these two, and simulation allows SHL to assess this at a granular level.
Thus, plant simulation allows SHL to gain comprehensive insights into the flow of materials and the use of resources, personnel and space. In the grander scheme of things, the modularity and heritability of simulation outputs allow future device projects to leverage these newfound learnings. Likewise, these attributes show how simulation can be a powerful tool for planning and expanding global manufacturing operations.
THE ROLE OF SIMULATION IN GLOBAL EXPANSION
On the polar opposite end of granularity lies the opportunity for simulation to impact on a macroscopic scale. With a growing patient population relying on autoinjector products to administer their treatments, SHL is committed to a global expansion journey (Figure 3).
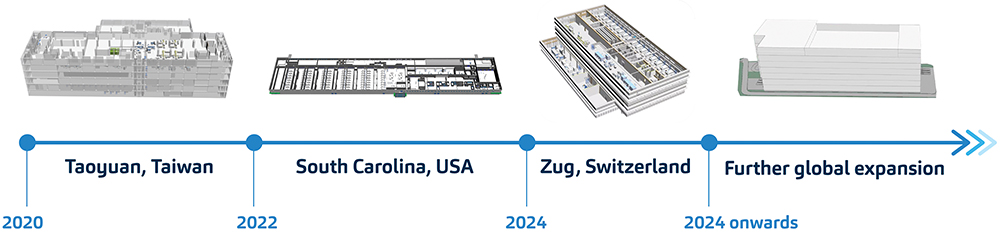
Figure 3: Expert simulations facilitate progressive global expansion plans. SHL’s simulation team has created a model of each factory site that encapsulates the entire operations, including the process flow, material handling, and machine operations.
This expansion now includes manufacturing sites in development in the US and Switzerland. This ushers SHL’s production lines into continents where many of the world’s leading pharma and biotech companies reside, and epitomises the true essence of 24/7 operations that transcend time zones. As SHL attempts to make supply chains more efficient by being closer to its pharma partners and their patients, the company is staying true to its promise of using digitalisation to embody operational excellence. The use of simulation technologies is a testament to this pursuit.5
It has been said that the future of autoinjectors is mass customisation. To this end, the flexibility and scalability of the entire manufacturing infrastructure are vital for meeting the needs of pharma and the patients. By leveraging the computing power of simulation, SHL is on course to build a sustainable process that achieves flexible, smarter factories that yield products more efficiently than ever across the entire value chain.
Learn more about SHL’s design, development, and manufacturing solutions for autoinjectors, pens and other drug delivery systems at: shl-medical.com.
REFERENCES
- “What is Industry 4.0?”. Company Web Page, IBM, September 25th, 2023. (https://www.ibm.com/topics/industry-4-0. Accessed September 2023)
- Kearns J, Huang K, “Putting Process Engineering into Action”. ONdrugDelivery, Issue 133 (May 2022), pp 8–12.
- Wild L, Fuensalida Pantig GR, “The “Customisable Platform” Paradox”. ONdrugDelivery, Issue 113 (Oct 2020), pp 80–85.
- Blatter J, “Glocalization”. Encyclopedia Britannica Online, May 21, 2013. (https://www.britannica.com/money/topic/glocalization. Accessed September 2023)
- Pedreso T, “Continuous Improvement: From Abstraction to Reality”. ONdrugDelivery, Issue 136 (Aug 2022), pp 44–48.