To Issue 132
Citation: Bhat J, Solanki A, “Capsules: Classic Drug Delivery Form Holds Potential for Sustainable Delivery.” ONdrugDelivery, Issue 132 (Apr-May 2022), pp 42–45.
Jnanadeva Bhat and Anita Solanki discuss the role that hard capsules are able to play in delivering a more sustainable pharmaceutical industry, both as an oral solid dosage form and in dry powder inhalers.
“Sustainability is not a trend but a prerequisite for the pharmaceutical industry to safeguard its future.”
Humanity’s wellbeing is not only associated with our own health but closely related to the condition of our surrounding environment. As such, environmental sustainability and protection are crucial, and it is our responsibility to safeguard environmental resources and ecosystems to ensure wellbeing both now and in the future. The pharmaceutical industry has a significant global environmental impact, from excessive waste creation to greenhouse gas emissions and the use of non-renewable energy. To move forwards, environmental sustainability needs to be considered across all activities and processes, from manufacturing to design and development.
The pharmaceutical industry must acknowledge this and face up to the challenge of improving the way it operates to create a sustainable future, whilst maintaining access to good quality medicines for all. Environmentally accountable pharmaceutical firms should develop practices for manufacturing their products in a more efficient and sustainable manner. Companies should have self-imposed targets and initiatives to reduce the impact of their activities on the environment, while also keeping the patient in mind and product efficacy intact. Strategies that can foster environmental sustainability within the pharmaceutical sector are those that promote the efficient development and production of sustainable products.
Accounting for around 60% of drug products,1 oral solid dosage forms are some of the most widely manufactured drug delivery systems, and advancements in oral drug delivery are contributing to the growing variety of products on the market. It is therefore imperative to take measures and adopt more sustainable practices, particularly within this drug delivery sector.
Capsules are one of the most established and flexible solid oral dosage forms and can play an important role in the journey towards accessible, sustainable drug delivery systems. This article will examine how capsules can become an environmentally friendly and sustainable dosage form, including:
- Capsule formulation development
- Capsule manufacturing
- Sustainable clean label and vegetarian options for capsules
- Capsules for inhaled drug delivery.
“Compared with soft gel, hard capsules require fewer manufacturing steps and have reduced production timelines, waste production and other operational costs.”
HARD CAPSULE FORMULATION DEVELOPMENT
Sustainability is not a trend but a prerequisite for the pharmaceutical industry to safeguard its future. This may mean product development using either direct ingredients or minimally processed excipients or may even refer to products being developed using fewer ingredients.
The very first step in formulation development and design is evaluating the compatibility of various ingredients. The key is to assess crucial attributes, such as the physico-chemical properties of the drug and formulation compatibility. Hard capsules are ideal for this process of dosage form development, as they provide the flexibility of filling the desired dose from large-scale, fully automated filling machines, intermediate-scale semi-automatic filling or very small-scale manual filling operations.
Capsules as a dosage form are relatively easy to design and develop (Figure 1). Complex machines are not required, as capsule formulation development can be achieved in laboratories using either a manual or small-scale capsule filling machine. Hard capsules eliminate the need to make complex formulations compared with other dosage forms. This means a reduction in the use of excipients or additives, which corresponds to using fewer ingredients during large-scale manufacturing.
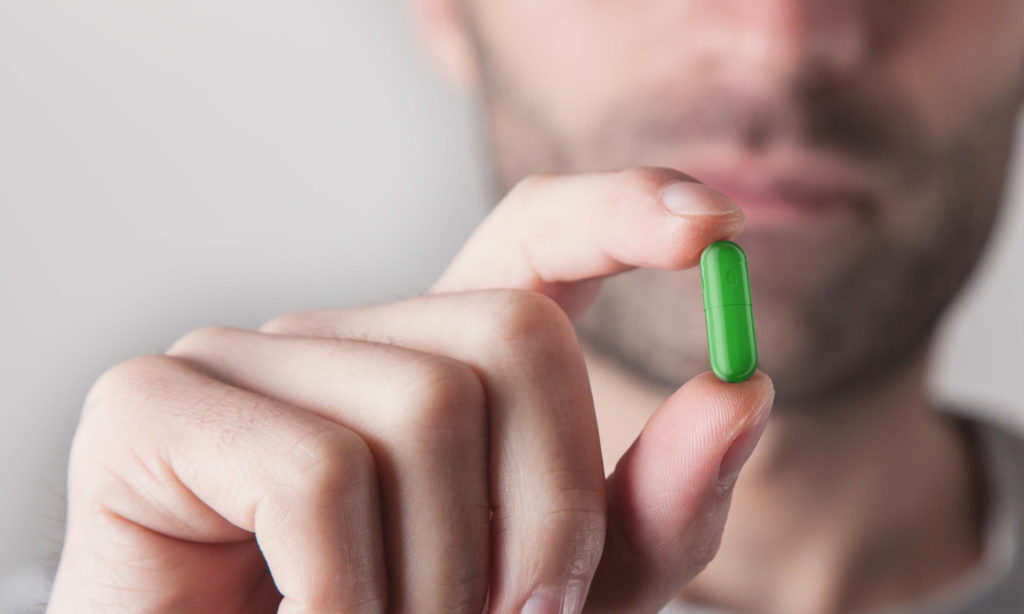
Figure 1: Hard capsules are a versatile and environmentally friendly drug delivery option that are comparatively easy to design and develop for.
“Capsule-based dry powder inhalers are sustainable in large part because the capsules are developed from biodegradable polymers, such as gelatine and HPMC.”
Improvements in capsule technologies mean that two different dosage forms can now be combined into a single hard capsule. This eliminates the need to develop separate formulations or dosage forms. The additional savings that can be made by combining two dosage forms not only include the reduction in required human and manufacturing resources but also reductions of material usage in the wider supply chain, including resources for packaging, storage, transportation and further storage before final distribution. A wide variety of multi-release, multi-phasic and multiple dosage forms can be developed in a hard capsule. A combined formulation of pellets or multi-tablets inside a capsule, or capsule inside a capsule, enables formulation scientists to achieve the desired therapeutic action in a more effective manner.
HARD CAPSULE MANUFACTURING
Hard capsules generally require a lower number of excipients and fewer processes and analytical tests, which accelerates validation and speeds up manufacturing. Unlike tablets, the manufacture of hard capsules does not require granulation, drying, compression, coating or printing.2 As such, the required machinery has fewer components, is more energy efficient and the process is faster.
Compared with soft gel, hard capsules require fewer manufacturing steps and have reduced production timelines, waste production and other operational costs. By comparison, the volume of gelatine offcuts, known as “nets”, generated after soft gel manufacturing can be very high and represents a serious waste of raw materials. Therefore, attempts have been made to recycle discarded gelatine nets but, as gelatine contains a wide variety of additives used in the manufacture of gelatine ribbons, it is a difficult process to recycle gelatine. Due to the presence of plasticisers, water and other preservatives, colourants, opacifier, etc,3 several processes to remove the additives are required. Recycling methods continue to be explored.
Various sustainable processes, such as zero liquid discharge and wastewater management, are being implemented in the manufacture of hard capsules. Zero liquid discharge is a strategic wastewater management system that eliminates the discharge of industrial wastewater into the environment. This is achieved by treating wastewater, adopting a “recycle, recover and reuse” approach for other industrial purposes and reducing the intake of fresh water. Another sustainable strategy is the use of solar energy which helps to reduce non-renewable energy consumption and its associated carbon footprint.
SUSTAINABLE, CLEAN LABEL AND VEGETARIAN OPTIONS IN CAPSULES
Gelatine Capsules – Sustainable Option
Gelatine is a sustainable and versatile polymer, contributing to its place as the main polymer for producing capsules. Unlike many other ingredients, it is derived from animals, being extracted from bone collagen and cattle hides. Gelatine aids in the complete usage of materials that are by-products of the meat industry, contributing to a zero-waste of materials.
HPMC – Clean Label and Vegetarian Option
In recent years, there has been a shift towards hydroxypropyl methylcellulose (HPMC) as the material of choice for capsules in both the pharmaceutical and dietary supplement industries (Figure 2). HPMC offers myriad advantages on top of being a vegetarian polymer. These capsules are widely used by many pharmaceutical companies for new molecules and products. From conventional capsules filled with powder, pellets or liquids intended for oral administration to those intended for dry powder inhalation applications, HPMC capsules are used in a range of therapeutic areas. Capsules come with certifications from the Vegan Society (Birmingham, UK) and Clean Label Project (CO, US), assuring that HPMC capsules are clean, safe and sustainable.
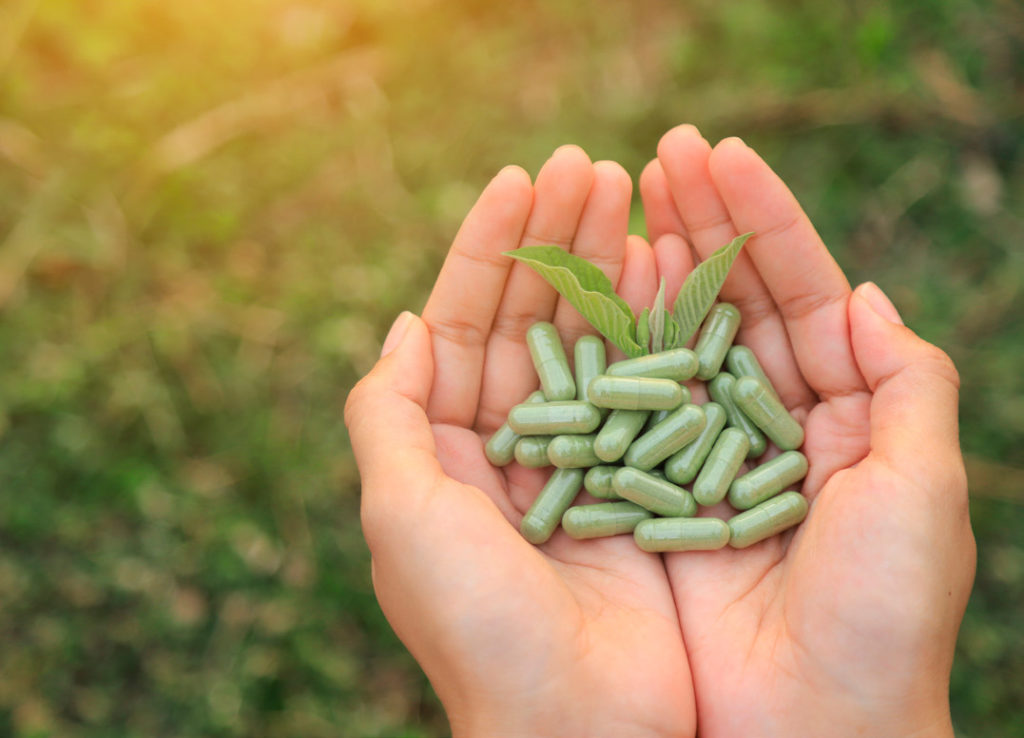
Figure 2: The pharmaceutical industry is seeing a shift towards HMPC as the material of choice for hard capsules.
CAPSULES FOR INHALATION APPLICATIONS
Asthma and chronic obstructive pulmonary disease (COPD) are among the most common chronic respiratory diseases worldwide. One way these conditions are treated is by delivering medication as an aerosol using a metered dose inhaler (MDI). However, MDIs use hydrofluorocarbon (HFC) propellants – powerful greenhouse gases that excessively contribute to the climate temperature crunch.4
Previously, MDIs used chlorofluorocarbons (CFCs) as a propellant but, due to the damage CFCs cause to the ozone layer, MDIs transitioned to using HFCs, which do not deplete the ozone layer but are more potent greenhouse gases than CO2. Modern MDIs depend on hydrofluoroalkanes (HFAs) that have a carbon footprint equivalent to more than 500 g of CO2 per dose – more than 25 times that of dry powder inhalers (DPIs).5 In a case study, it was reported that MDIs using HFAs as a propellant gas can have, on average, a carbon footprint up to 50 times higher than that of a capsule-based DPI.6
The more sustainable and environmentally friendly alternative is capsule-based DPIs, which are widely accepted by healthcare professionals and patients. Capsule-based DPIs are sustainable in large part because the capsules are developed from biodegradable polymers, such as gelatine and HPMC. DPIs do not require propellants and their effectiveness depends solely on the capsule, the device, the powder formulation and the patient’s inhalation. They are easy to use and control, as well as being cost effective, painless, portable and, most importantly, patient friendly.
In the meantime, steps should be taken to develop all inhalers in a more sustainable way, keeping in mind the “recycle, recover and reuse” approach. Such a move may require higher investment when establishing a product, verifying the efficacy and dose control of a device over many years of repeated use. The device components need to be made from robust materials that are compatible and can be recycled. Furthermore, it is anticipated that such use of sustainable materials and reduction of waste and carbon emissions will be enforced by future regulation.
CONCLUSION
Owing to urgent ecological demands, an emphasis on protecting the natural environment for coming generations is crucial. With a shift to more reliable use and product development, pharmaceutical companies are willing to adopt more eco-friendly approaches. Sustainability and environmentally friendly practices should be a priority for the pharmaceutical industry. Reducing the industry’s carbon footprint and developing sustainable products are of key importance.
Hard capsules, being an oral solid dosage form, play an important role in sustainability. Gelatine and HPMC hard capsules are environmentally friendly and biodegradable, while being capable of delivering accurate doses. Hard capsule formulation development and manufacturing both hold potential for sustainable drug delivery. Furthermore, dry powder formulations are one of the most sustainable ways to deliver drugs via the inhalation route. The pharmaceutical industry must live up to the responsibility of sustainability for the benefit of the natural environment – even the smallest contribution will be one step closer to achieving a better future.
REFERENCES
- “The Reign of Oral Solid Dosage Forms in the Era of Biopharmaceuticals”. Pharma Trends, Mar 2020.
- “Capsule Oral Dosage Forms: Providing Benefits Throughout the Entire Drug Product Lifecycle”. Nutraceutical Business Review, Jun 2021.
- Kim J, “Method and Apparatus for Recovering High-Purity Gelatin from Gelatin Net to be Generated in Gelatin Capsule Preparation Process”. International Patent WO2016/010207A1, Jan 2016.
- “Chronic Obstructive Pulmonary Disease (COPD)”. WHO website, Jun 2021.
- Patel M, Sheridan E, “Sustainability in Drug Delivery: A Green Future Without Compromising Safety and Efficacy “. Chim Oggi – Chem Today, Jan/Feb 2021, Vol 39(1), pp 20–22.
- “Novartis Environmental Sustainability Strategy”. Novartis, 2021.