To Issue 152
Citation: Koyanagi P, Mio A, “Combining Plastic Bag Flexibility with Glass Storage Stability – Next-Generation Packaging for Sensitive Premixed Drugs”. ONdrugDelivery, Issue 152 (Oct 2023), pp 84–86.
Pauline Koyanagi and Atsushi Mio look at the benefits of flexible drug packaging and discuss ZACROS’s MediTect™ packaging for sensitive liquid parenteral formulations.
Intravenous (IV) drugs are most easily administered using a premixed, ready-to-use bag. Unlike injectables that require admixing, these are essentially a closed system, mitigating the risk of exposing patients and medical workers to harmful chemicals and avoiding the risk of human error in drug preparation. Premixed bags eliminate the time needed for drug reconstitution and provide the ideal grab-and-go solution, which may be crucial in emergency situations when every second counts to save a life.
“Conventional IV bags are not suitable for many sensitive drugs due to stability problems, and injectable drugs known to be unstable in plastic are still typically packaged in glass bottles or vials.”
Additionally, flexible plastic packaging is lightweight, robust and easy to handle, with a lower carbon footprint than glass. Lighter and more compact, it requires less material for manufacture than rigid containers and takes less space for transport, storage and disposal.
However, conventional IV bags are not suitable for many sensitive drugs due to stability problems, and injectable drugs known to be unstable in plastic are still typically packaged in glass bottles or vials. The provision of stable, next-generation IV bags promises to solve these problems by helping to ensure the purity of drugs administered to patients, thereby improving patient safety and outcomes and reducing the burden on medical staff.
REDUCING THE RISK OF INTERACTION
When changing a dosage form from a concentrated solution in a glass container, such as a vial or an ampoule, to a ready-to-use plastic bag, the chief concern is the interaction of the drug formulation with the bag’s plastic surfaces. Primary containers are designed to prevent all interaction between the drug contents and the packaging material, including extractables migrating into the formulation and sorption of the API into or onto the bag itself. This is vital to preserve the intended potency of the contained drug.
Conventional IV bags are recommended for IV infusion of stable drugs that have a low level of interaction. However, these are not suitable for several small molecules and biologics, including those with highly diluted APIs such as large-volume parenterals.
Established in 1914, ZACROS is a Japanese company that converts flexible films into a range of packaging solutions. It has created unprecedented functionality in flexible plastics, with core competencies in film casting/co-extrusion and bag-making. This is backed by extensive research into cyclo-olefin polymers and copolymers (COP/COC), which are important engineering plastics with many useful properties.
For parenteral container applications, COP/COC were initially used for prefilled syringes and vials – rigid containers made from injection moulding. ZACROS was the first company to succeed in making COP into a flexible film, and the company has spent seven years developing and refining non-interactive (NI) films that prevent elution and sorption. This has enabled the production of IV bags that offer ultimate stability for sensitive drug contents, combining glass-like storage stability with the flexibility of plastic bags. The NI resin used for the layer in contact with the contained drug enables historically unstable drugs to be packaged in plastic and immediately administered to a patient (Figure 1).
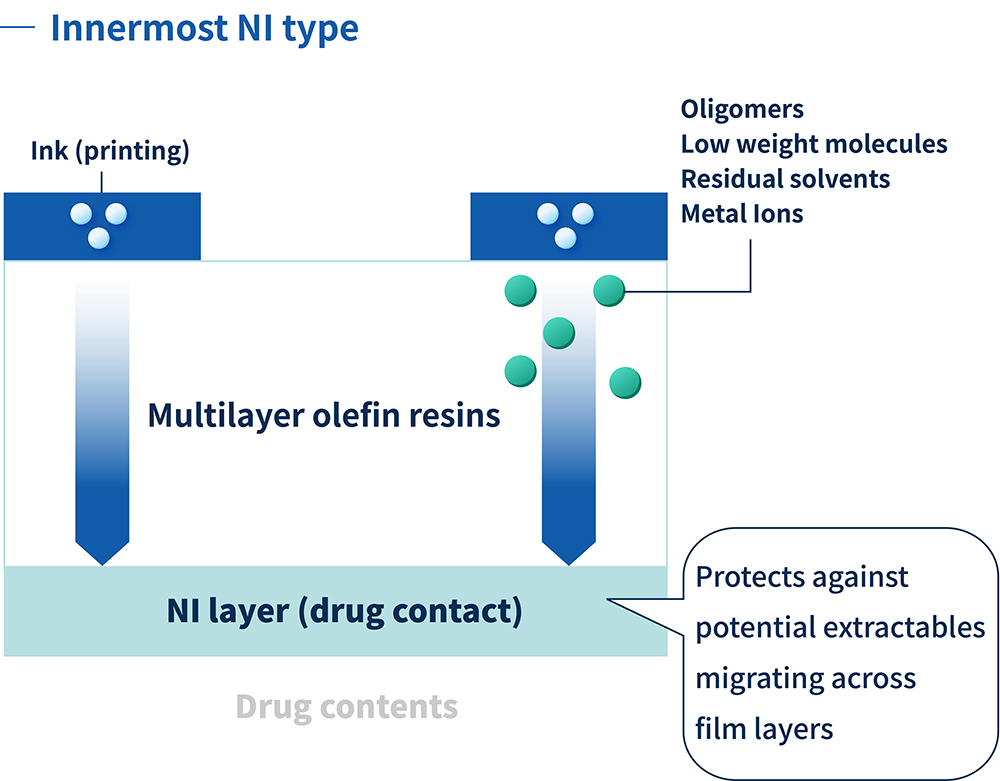
Figure 1: The NI layer acts as the ultimate defence against potential extractables.
MEDITECT™ TECHNOLOGY
MediTect™ packaging has been created by ZACROS specifically for sensitive liquid parenteral formulations, and is dedicated to maintaining sensitive liquid pharmaceuticals in their original state from formulation to administration. It offers a variety of material options and properties, making it ideal for premixed bags. Its main applications are neurological drugs, angina treatments and osteoporosis treatments.
Product features include:
- NI properties, enabling glass-like drug stability performance
- US FDA drug master file (DMF) registered, and compliant with EP, USP and JP regulations
- High level of safety, hygiene and functionality ensured by multilayer co-extrusion technology
- Manufactured in a ISO 15378 & 13485-compliant site (ISO Class 6 cleanroom).
The proprietary NI technology combines an unparalleled level of chemical compatibility and sorption resistance with an ultra-low extractables profile. The multilayer olefin resin minimises extractables of all kinds, including polyolefin oligomers, residual solvents, additives, adhesives and inactive ingredients volatilised from ink. Such extractables cause drugs to become unstable and can compromise the quality of the IV solution.
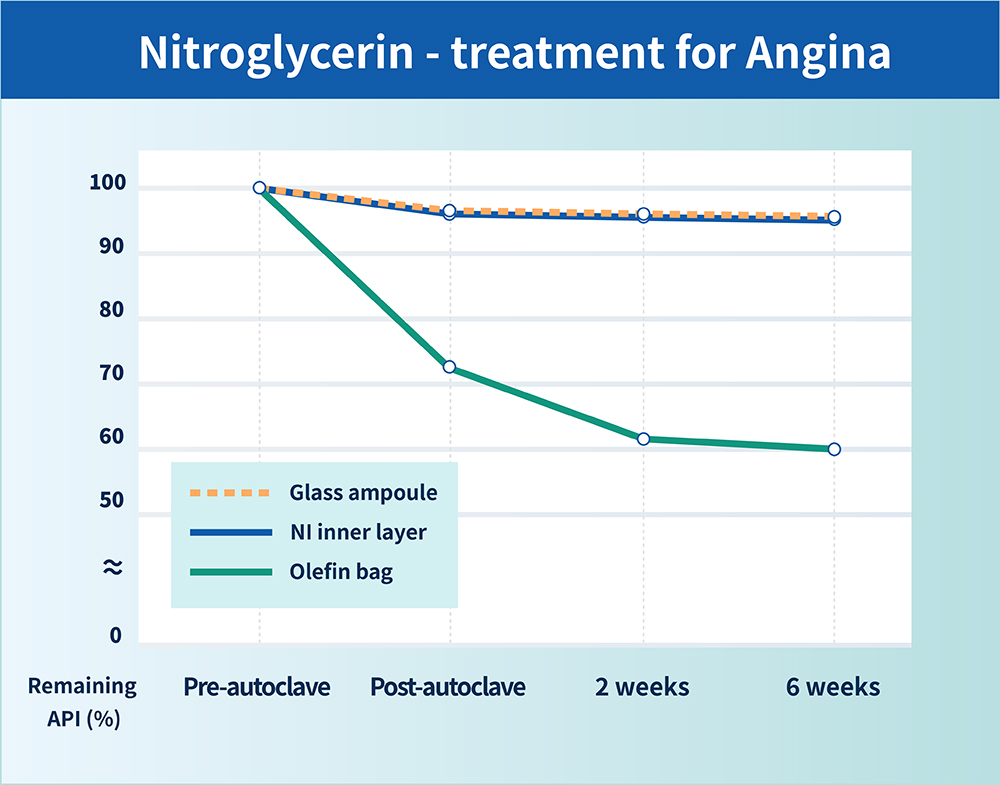
Figure 2: MediTect™ bags maintain the potency of APIs over time comparable with glass container controls.
The properties of the NI film provide product integrity and help to maximise the shelf life for the most demanding applications. Performance data show that the bags maintain the potency of APIs over time by the prevention of sorption effects comparable with glass container controls (Figure 2).
MediTect™ IV bags have many different construction options. Table 1 provides information about ZACROS’s standard bag options compatible with hydrophobic APIs.
NI-PP (inner NI) | NI-PP (inter NI) | |
Film layers | PP/AD/NI | PP/AD/NI/AD/PP |
Fill volumes | 50–300 mL | 50–300 mL |
On-bag printing | Yes | Yes |
MVTR (g/m²/day) | 1.1 | 1.5 |
Heat resistance | 121ºC compatible | 121ºC compatible |
Table 1: ZACROS’s standard bag options compatible with hydrophobic APIs.
WORKING IN PARTNERSHIP TO DELIVER NEXT-GENERATION FLEXIBLE PACKAGING
ZACROS has an integrated manufacturing process for MediTect™ products from start to finish. It can develop products to meet specific requirements and can work directly with companies or introduce experienced contract manufacturing organisations for filling. ZACROS’s liquid medicine primary packaging has been sold in the US and Japan for over 30 years, and some products are DMF registered. Staff are well versed in major regional regulations and guidelines and can help with submissions to the FDA and other regulatory authorities.
MediTect™ IV bags have been commercialised in Japan for over ten years. For example, ZACROS has worked with one of its partners to develop premixed bags for the administration of nitroglycerin to treat heart failure. All infusion bags are compliant with ISO standard 15747 (covering plastic containers for IV injections) and can keep the drug stable after autoclave terminal sterilisation and long-term storage. Bags come in a variety of shapes, sizes and labelling and can be made with various materials of construction. All are non-PVC and DEHP-free. ZACROS is currently broadening its portfolio by including aseptic-filling compatible IV bags that are focused on biologics.
Testing facilities are available for MediTect™ products, and ZACROS’s R&D centre in Japan offers opportunities for joint development. Prototypes and samples are readily available, and bags may be customised to multiple sizes and configurations. The R&D centre offers powerful evaluation equipment to customers, who can make use of the prototype workshop and small scale modular equipment for quick sample creation. The machinery room has filling machines for each type of packaging, sterilisation systems, handling systems and other semi-automated machines that are available for testing and assessing customer tailored packaging and contents.
The experimental factory is intended for joint-development and in-house experimenting, where quick testing and assessing is possible. Isolators make it possible to handle and perform tests with a wide range of pharmaceutical contents directly on the premises.
For additional barrier properties, overwrap secondary packaging is also available. Overwraps are an economic way to add barrier properties to primary packaging as desired. For example, for products that are sensitive to oxygen, wraps are available that have very high oxygen barrier properties – these have been tested and developed and are already on the market. These pouches come in a variety of shapes, sizes and colours, and can be made with various materials of construction (VM-PET, aluminium, etc).
Increasing interest from overseas means that ZACROS is now working with a range of pharma and biotech companies to develop products for specific applications and create differentiated, novel containers. The platform is expanding from small molecules and terminal sterilisation to include biologics and aseptic filling, with more formats in development. The bags have proved compatible with all drugs that have been tried so far.
As the technology develops further, ZACROS believes that it will become a key enabler for modern healthcare, allowing safe, regular drug administration in a home setting and therefore fewer hospital visits.
Find out more about ZACROS by visiting: www.zacros.co.jp.