To Issue 138
Citation: Auld J, “Design Strategy and Considerations for Compressed Gas-Powered Device Applications. ONdrugDelivery, Issue 138 (Oct 2022), pp 52–57.
Jack Auld discusses the potential of compressed gas as a power source for drug delivery devices, and explains how Altaviz can empower drug developers with the expertise to make full use of this exciting technology.
“Today, gas-cylinder-powered applications across the drug delivery segment include autoinjectors, on-body injectors, specialty oral dosages and nasal delivery.”
INNOVATIVE ENABLING TECHNOLOGY REQUIRES APPLICATION DESIGN EXPERTISE
Drug delivery device development and manufacturing organisations serve a biopharma customer base whose hallmark is high-diligence, data-based decision making. While this approach reduces risks in delivering life-saving and life-sustaining drugs, it has also led to a slow pace of change and innovation. However, new gas-powered technologies can provide flexibility to tailor the performance in ways that have not been available with traditional technologies.
The vast majority of autoinjector designs on the market today are similar to the first devices developed in the 1970s. These designs are powered by compression springs and have inherent limitations, including:
- Noise and vibration from the moving mass of the spring
- High-volume/viscosity drugs exceeding the limits of existing spring-based systems
- Syringe breakage from the impact of the spring release
- Stress and creep on housing materials
- Force reduction over time due to stress relaxation of the spring
- Manufacturing challenges of detangling and managing large springs
- Requalifying manufacturing lines for simple changes like viscosity or delivery times.
The autoinjector market is expected to grow over the coming years,1 especially considering the increase in higher-viscosity biologics, which are not good candidates for spring-loaded delivery technologies, currently making their way through the pharmaceutical pipeline. Innovation and performance enhancements in compressed-gas-powered autoinjector technology are made possible by Picocyl’s medical-grade compressed gas cylinders (Pico-Cylinders).2 This article will explore design considerations for gas-powered autoinjectors made with these cylinders (Box 1).
BOX 1: DESIGN STRATEGY AND CONSIDERATIONS FOR COMPRESSED GAS-POWERED DEVICE APPLICATIONS
Select a Team to Reduce Risk
A team that can demonstrate past success, is experienced with gas-powered applications and has device and therapy knowledge can help significantly de-risk a project.
Leverage Inherent User Experience Benefits
Gas-powered devices offer key benefits over traditional spring-powered devices, including silent, low-vibration power; the ability to engineer the delivery time; and the ability to engineer the force profile from activation to the end of delivery.
Establish a Design Strategy
It is important to make an early decision on whether to use a platform or a bespoke device, make use of proven accelerator subsystems and build confidence with early data.
Adopt a Systems Thinking Approach
Be sure to consider the product requirements for the patient and use environment; the cylinder size, gas and gas pressure and isolation; and the plunger drive, system volume and Pico-Cylinder deployment and activation options using a systems thinking mindset.
“The key advantage of using gas power is the design flexibility to tailor and increase the performance of a delivery device in ways that were previously unattainable.”
ARE MEDICAL-GRADE GAS CYLINDERS READY FOR DRUG DELIVERY DEVICES?
Today, gas cylinder-powered applications across the drug delivery segment include autoinjectors,3 on-body injectors,4 specialty oral dosages4 and nasal delivery. A summary of Altaviz-developed platforms based on Pico-Cylinder technology is shown in Figure 1.
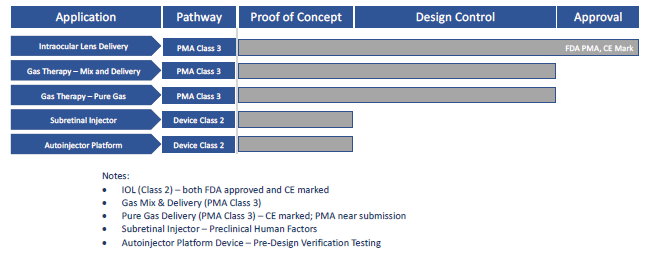
Figure 1: Altaviz platforms based on Pico-Cylinder technology.
Enabled by a design team with proven medical device and gas-powered delivery domain expertise, Pico-Cylinders have been used in precision applications since 2012. One example is a cataract surgery delivery device that was commercialised in 2017. To date, millions of intraocular lenses (IOLs) have been safely delivered across 64 countries via this innovative self-powered device, which offers unparalleled control for surgeons during implant delivery. Integrating the Pico-Cylinder into the IOL delivery device has allowed the IOL manufacturer to have the best-in-class delivery device in the cataract market.
GETTING PAST A COMMON CONCERN: GAS PRESSURE ISOLATION AND SAFETY
Safety questions should always be at the forefront when changing from an established technology. A common safety question is: “How is the gas isolated from the prefilled syringe to prevent any potential exposure that would contaminate the drug?” Figure 2 presents a schematic diagram of a drug delivery device that shows how the gas-powered plunger rod is the only part of the system in contact with the stopper. The gas, fully contained within the Pico-Cylinder and the system volume, does not make contact with the drug, stopper or patient and is isolated by the atmospheric barrier.

Figure 2: Gas pressure isolation from primary drug container.
A second common question is: “Are the gases safe in terms of exposure and the environment?” The most commonly used gases are carbon dioxide (CO2), argon (Ar) and nitrogen (N2), all of which are found in the atmosphere and are environmentally friendly.
A third common question is: “Is pressurised gas safer than springs in a medical device?” In a gas-powered delivery system, the pressure is fully contained within the gas cylinder until point of use and, upon gas deployment, the gas first expands into a “system volume” before any pressure is applied to the plunger rod. As a result, the internal components only see pressures lower than the cylinder pressure and only at the time of use.
Furthermore, the system volume chamber pressure steadily increases from atmospheric pressure up to the point friction is overcome, initiating plunger rod movement, which allows soft loading of the system components, including the primary drug container, thus reducing the chance of breakage. In contrast, a delivery system powered by a spring endures the full preloaded force of the compressed spring over the full shelf life of the device, leading to plastic creep in the housings and stress relaxation in the springs. When activated, a spring in the spring-loaded system rapidly accelerates and as much as a third of the spring’s mass acts like a hammer on the device’s internal system components, leading to syringe breakage and potentially startling users from the noise and feel of the impact.
A fourth common question is: “Are gas cylinders safe and reliable?” Pico-Cylinders are designed with compliance to the BS EN 16509:2014 standard for transportable, non-refillable gas cylinders, ensuring a safe, robust transportable design with burst pressures in excess of 500 bar. Because the gases are hermetically sealed in full metal containers that are 100% tested for leak integrity following temperature cycling above 120°C, shelf-life durations of over five years are common and achievable.
LEVERAGE INHERENT USER EXPERIENCE BENEFITS
The enhanced flexibility offered by compressed gases in generating syringe pressure, tailored to the application via systems engineering of the system volume, opener pin and cylinder pressure, can also extend to offering enhanced user experience factors, such as reduced noise, vibration and injection time compared with conventional spring-based systems. The noise and vibration of a gas-powered system is limited to the opening of the cylinder and the movement of the plunger, compared with the high moving mass and impact forces common to spring-based systems. A demonstration video of a gas-powered platform autoinjector can be found on Altaviz’s website, here.
ESTABLISH DESIGN STRATEGY
Among the first decisions to be made when considering a delivery device for a new drug product is whether to design a bespoke, drug-specific device or start with a platform device that has broader application potential. If opting for the platform path, an early decision is necessary to enable defining the platform performance range, features and customisations. Ideally, a platform’s functionality provides a maximum range of drug volume and viscosity capability, minimum cost and time to customise for each application, and a minimum effort to manage autoinjector variants once in commercial production.
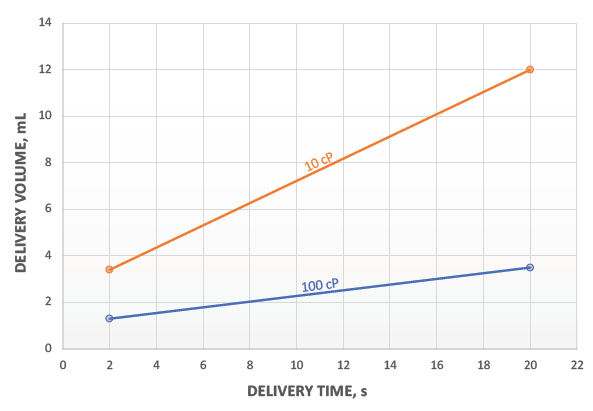
Figure 3: Volume and viscosity window for 1 mL Pico-Cylinder at 270 bar.
This flexibility can be built into a platform that takes advantage of the Pico-Cylinder’s high-energy density. As shown in Figure 3, a 1 mL Pico-Cylinder filled with Ar at 270 bar can deliver a wide range of volumes and viscosities. The intention here is not to suggest what volumes are suitable for a specific drug or within a patient’s tolerability range, but to demonstrate the very broad operating window for a compressed-gas-powered autoinjector, even before considering the ability to change gas pressure easily to tailor the delivery times for specific applications.
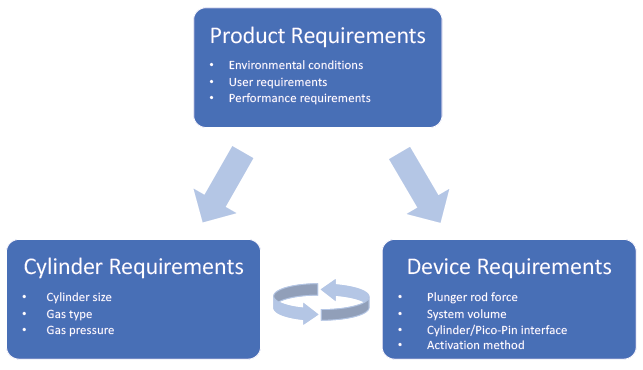
Figure 4: Product, cylinder and device requirements in a Pico-Cylinder driven system.
“To ensure the overall function and reliability of the device, Pico- ylinders are validated with off-the-shelf Pico-Pins that interface with the cylinder’s unique breakaway septum to provide the consistent, low-force opening that is the hallmark of this system.”
SYSTEM DESIGN
The key advantage of using gas power is the design flexibility to tailor and increase the performance of a delivery device in ways that were previously unattainable. Successful implementation requires a thorough understanding and implementation of the product requirements into the device and then optimisation of cylinder requirements to maximise performance (Figure 4). The fastest and most efficient path to product execution is to leverage the expertise and technologies of an experienced team to create early designs that demonstrate the device’s performance.
Whether developing a bespoke delivery device or a broad platform, best practices include first identifying target usage requirements for the specific drug or range of drugs. Parameters, including operating temperature range, drug viscosity, delivery volume and time, should be established to assist in identifying the optimal device subsystems. Each of these design parameters may leverage the available application accelerator subsystems to decrease design risk, project timeline and development cost by building upon prior learnings. These subsystems include standard options for:
- Cylinder size, gas selection and cylinder cap configuration
- Opener pins (Pico-Pins) and valves for selected applications
- Activation mechanisms, such as push to skin, thumb button or side/lever action.
Cylinder Size and Gas Selection
Standard cylinder sizes are 0.7 and 1.0 mL, which are suitable for most applications. Custom sizes can also be made to fit specific applications when required.
In terms of gas selection, the primary consideration is the use environment.

Figure 5: Dual-phase gases provide a constant pressure at a set temperature resulting in a constant force profile.
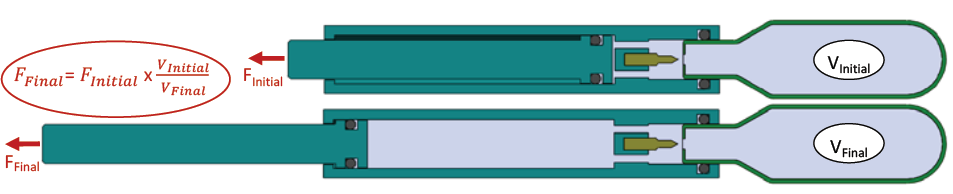
Figure 6: Force drop over stroke due to increase in internal volume as plunger deploys.
When devices are intended for use in a temperature-controlled environment, such as an operating room, dual-phase gases (liquid and vapour) may be preferable due to their ability to provide a constant pressure throughout a long delivery stroke up to the expansion limit of the gas. This allows for a constant delivery force throughout the entire stroke, as illustrated in Figure 5.
Conversely, some devices, such as autoinjectors, may be used across a wide temperature range from low temperatures (shortly after being stored in a refrigerator) to high temperatures (after being stored in automobiles or backpacks). For these applications, a single-phase (vapour only) gas may be preferable because its pressure varies as a function of the absolute temperature (°K), as defined by Gay-Lussac’s Law:
For the use case of an autoinjector operating in the range of 0°C–40°C (273°K–313°K), the pressure of argon will fluctuate by only 15% compared with dual-phase CO2 or HFC 134, where the pressure would increase by 185% and 247% respectively. Vapour phase gases, therefore, are the best choice for autoinjectors or devices where the patient self-administers across a wide temperature range.
Similar to spring powered delivery devices, vapour phase gas devices will demonstrate a reduction in delivery force as the plunger deploys (Figure 6). This is due to an expansion in internal volume resulting in a reduction in system pressure as governed by Boyle’s Law:
The expansion ratio is simply the proportion that the internal volume increases over the stroke of the device, as defined by the equation:
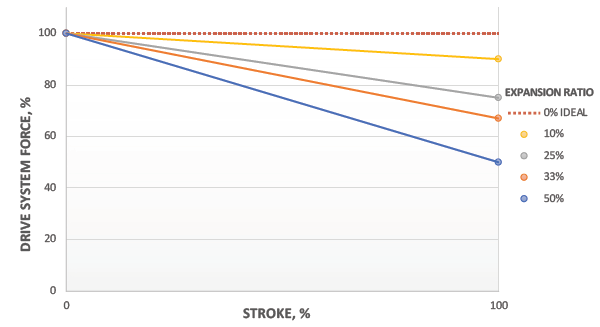
Figure 7: Delivery force profile as function of expansion ratio.
With optimised expansion ratios, the system will deliver near-constant force over the entire injection stroke, as shown in Figure 7. This leads to a consistent drug delivery rate and faster delivery time for a given peak flow rate. As a result, the patient will experience a more consistent delivery and shorter injection times.
Unlike springs, the force drop characteristics can be tailored for an application by designing to a target expansion ratio. As an example, the expansion ratio may be minimised by incorporating additional system volume to provide a more consistent force profile (Figure 8).
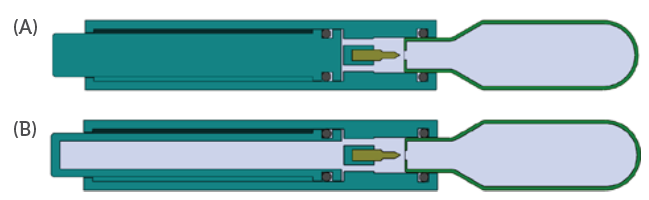
Figure 8: A more consistent force profile can be achieved by incorporating
additional system volume (B) compared to a traditional layout (A).
Pico-Cylinder Deployment
To ensure the overall function and reliability of the device, Pico-Cylinders are validated with off-the-shelf Pico-Pins that interface with the cylinder’s unique breakaway septum to provide the consistent, low-force opening that is the hallmark of this system. Figure 9 illustrates the interface between the Pico-Cylinder and Pico-Pin in two potential deployment concepts.
The interface between the Pico-Cylinder deployment and end-user activation mechanism may be tailored to the use case and patient needs. In the IOL inserter example, the manual activation method was used by incorporating a lever to move the Pico-Pin into the Pico-Cylinder to activate the device (Figure 9a).
In the case of other autoinjector systems, the common two-step activation method (remove cap and press to skin) has been employed with a spring-assist mechanism (Figure 9b) to deploy the gas from the Pico-Cylinder. Alternatively, the same mechanism may be activated with a push button or side lever.
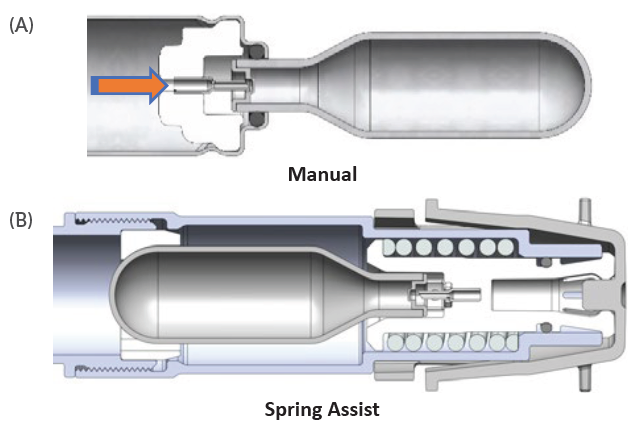
Figure 9: Two Pico-Cylinder deployment concepts.
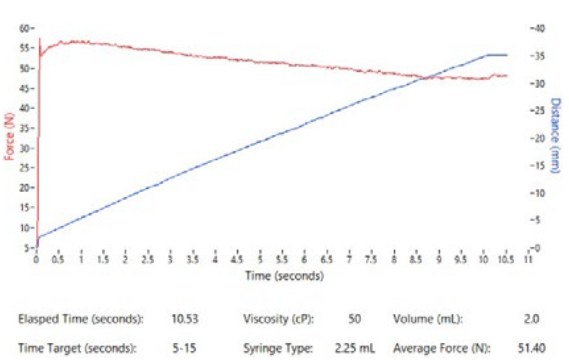
Figure 10: Altaviz test system graphical output showing position data and force profile.
BUILD CONFIDENCE AND REDUCE RISK VIA EARLY DATA GENERATION
Recognising the need for rapid feasibility data, Altaviz has developed a test system capable of using client-provided drug or Altaviz’s silicone oil formulations up to 100,000 cP along with a variety of component inputs and system settings, as summarised in Table 1. The test system is portable to enable use at a client site. This test system provides graphical data (Figure 10) that summarises syringe force and plunger position over time, graphed within seconds of each test sample. It enables ease of experimentation and enables clients to compare options with minimal hassle.
Test Systems Inputs | |
Components | Parameters |
• Prefilled syringes – 1 mL long – 2.25 mL • Simulated drug formulation – Up to 100,000 cP • 0.7 mL gas cylinder – Pressures up to 275 bar • Plunger rod – 3–8 mm diameter • Production Pico-Pin |
• Dose selection – 1 mL long: 0.5, 0.75, 1.0 mL – 2.25 mL: 1.0, 1.5, 2.0, 2.5 mL • System volume – 3–6 cc |
Data Collection and Reporting | |
Collection | Reporting |
• Plunger position • Drive system pressure • Syringe force |
• CSV data • Graphical data output versus time/position |
Table 1: Test system parameters and outputs.
SUMMARY
Compressed gases are a proven power source used across a range of precision healthcare applications. They provide a power option for differentiated, next-generation drug delivery devices. A platform with broad capability and flexibility can be effectively designed around a single cylinder size with the assistance of gas-power experts. These gas-powered systems can solve many problems or address limitations of legacy designs. Leveraging the design expertise and technology of teams experienced with gas-powered systems will mitigate risk and accelerate the time to market to get innovative products into end-users’ hands.
REFERENCES
- Sonar A, Sumant O, “Autoinjectors Market by Type (Disposable Autoinjectors and Reusable Autoinjectors), Application (Rheumatoid Arthritis, Anaphylaxis, Multiple Sclerosis, and Others), and End user (Homecare Settings and Hospitals & Clinics): Global Opportunity Analysis and Industry Forecast, 2020–2027”. Allied Market Research, Sep 2020.
- Welch W, “Advancements and Evolution of Power Sources in Drug Delivery”. ONdrugDelivery Magazine, Issue 133 (May 2022), pp 57–60.
- Roe MJ, “Challenges in High-Viscosity, High-Volume Drug Delivery”. ONdrugDelivery Magazine, Issue 125 (Oct 2021), pp 40–43.
- “New Utility Patent and enFuse® Vial Transfer System Technology”. Enable Injections webpage, accessed Sep 2022.
- “Progenity Announces Several Patents Granted by USPTO, Strengthening the Company’s Intellectual Property Position in Ingestible Therapeutics Technologies”. Bioara Therapeutics Press Release, Oct 2021.
- Shimizu JA et al, “Ingestible Device for Delivery of Therapeutic Agent to the Gastrointestinal Tract”. Patent WO2021119482A1, 2021.