Citation: Kiely M, Linnane G, Carroll J, “Important Considerations when Designing for Sustainability”. ONdrugDelivery, Issue 126 (Oct/Nov 2021), pp 70–74.
Michael Kiely, Gerard Linnane and Justin Carroll discuss how implementing a thoughtful design-for-sustainability process can ensure medical devices not only improve patients’ lives but are also kinder to the environment.
A recent study from Deloitte suggests that sustainability is a major issue for most customers in 2021.1 It reports that 32% of consumers are “highly engaged” with adopting a more sustainable lifestyle and 28% have stopped buying certain products due to ethical or environmental concerns. Younger generations are seen to be the most apt to adopt sustainable behaviours, with 50% saying they have reduced how much they buy and 45% have stopped purchasing certain brands because of ethical or sustainability concerns.
“A design for sustainability process should cover the entire product lifecycle – from design to disposal – and needs input from all stakeholders.”
The most common way consumers demonstrate their commitment to sustainability is by avoiding single-use plastics (61% of people). The single-use medical device reprocessing market was valued at US$1,858 million (£1,358 million) in 2018 and is expected to register a compound annual growth rate of about 15% during the forecast period of 2019–2024.2 Yet still approximately 90% of medical device waste comes from disposable, single-use components or products.3
Regulations and standards such as the Waste Electrical and Electronic Equipment; Restriction on Hazardous Substances; Registration, Evaluation, and Authorization of Chemicals; and the Energy Using Products have already positively impacted the sustainability of medical devices containing electronics. However, aside from meeting regulatory requirements, medical device manufacturers have typically not led the way in driving sustainability and sustainable product design, citing obvious challenges around cost, safety, functionality, usability and convenience.
The introduction of new regulations, increased consumer awareness of the environmental impact from medical waste and a sense of responsibility from companies to produce eco-friendly drug delivery devices has driven a rise in sustainability goals and policies in the medical and pharmaceutical industries. There are now programmes in place to reduce medical device waste by returning used devices for recycling, repurposing, refurbishing and re-use. These programmes present device companies with additional challenges such as establishing a safe means of returning the devices with a low burden on the user and developing infrastructure to introduce the returned devices safely and efficiently into the circular economy.
As medical device manufacturers navigate the many regulatory hurdles to approve a refurbished or multi-user medical device, there is also the obstacle of patients accepting treatment with a refurbished device. For now, it is unlikely that the medical device industry will transfer to a model where refurbished or multi-user medical devices are the norm. But to meet their sustainability goals, there are many small improvements that will make a big difference when introduced to the product lifecycle.
A process where design for sustainability is an integral part of the conceptual design process will ensure that environmental and sustainability considerations are elevated to a similar level as regulatory, functional and business requirements. A design for sustainability process should cover the entire product lifecycle – from design to disposal – and needs input from all stakeholders.
THE EARLY-STAGE DESIGN PROCESS
Jabil Healthcare has an established early-stage design process that meets regulatory design control requirements and supports optimisation of medical device design for large-volume manufacturing (Figure 1).
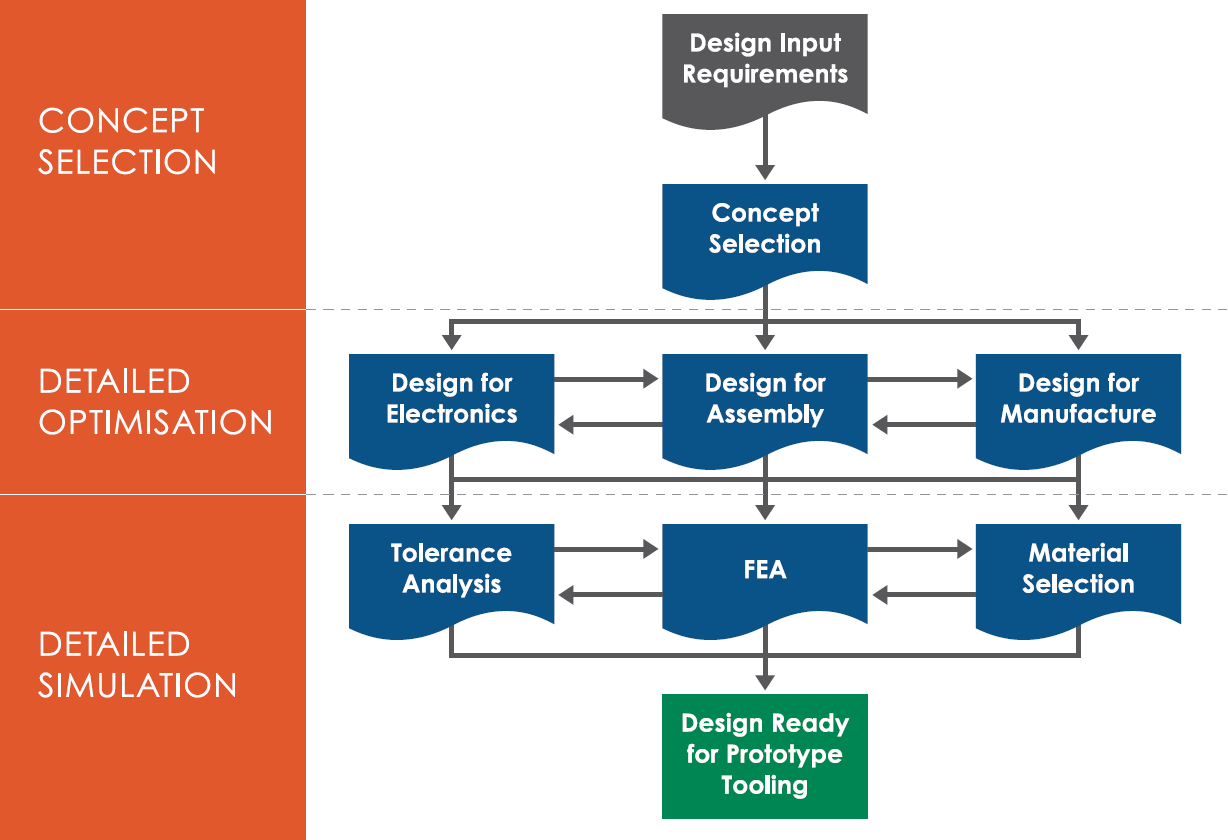
Figure 1: Early-stage design process elements.
This process commences with concept selection, where all potential concepts are reviewed and optimised into one selected design. The selected concept is then brought forward to the detailed optimisation stage, where subject matter experts from a range of disciplines (e.g. manufacturing, assembly and electronics) work with the design team to further improve the device design for each area. Following implementation of these optimisations, analytical tools, such as mould flow, tolerance analysis and finite element analysis simulations, along with final material selection, are conducted prior to the design being released for prototype manufacture. By integrating design for sustainability into its established early-stage design process, Jabil can have maximum impact on the sustainability of the device with minimal impact on project timeline and cost. However, this decision-making process for optimising sustainability needs to be informed and data driven, as we will discuss here.
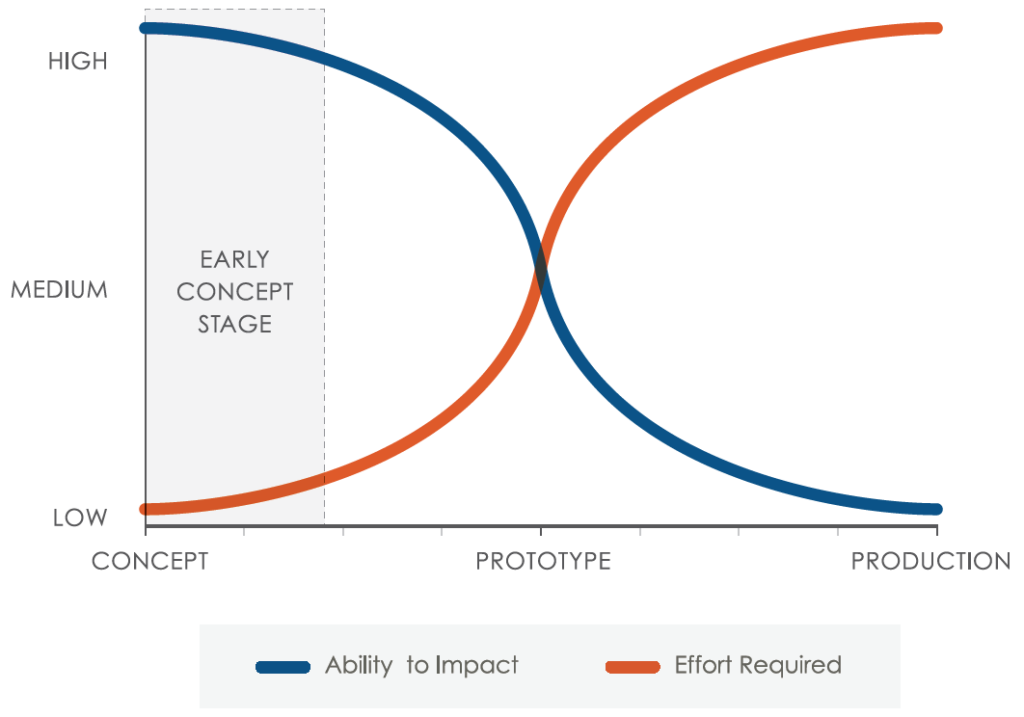
Figure 2: Device sustainability – ability to impact versus effort required.
STAGE 1: CONCEPT-SELECTION
At concept-selection stage, the opportunity to optimise a device design for sustainability is at its peak. Conversely, if you do not consider sustainability at this stage, your chance to consider it at later stages is much reduced, becomes more complicated and adds significant time and cost to the development lifecycle (Figure 2).
Design requirements are crucial input to the concept-selection stage, as all proposed concepts will ultimately be assessed against these. Therefore, establishing specific, measurable and attainable sustainability goals within the device requirements is a key contributor to success.
Jabil Healthcare uses a concept-selection matrix that accommodates a data-driven approach to assess each device against its design requirements. Applying a weight to each requirement and scoring each concept provides a holistic approach to assess the sustainability of a concept in the context of other requirements, such as functionality, manufacturability, usability and cost.
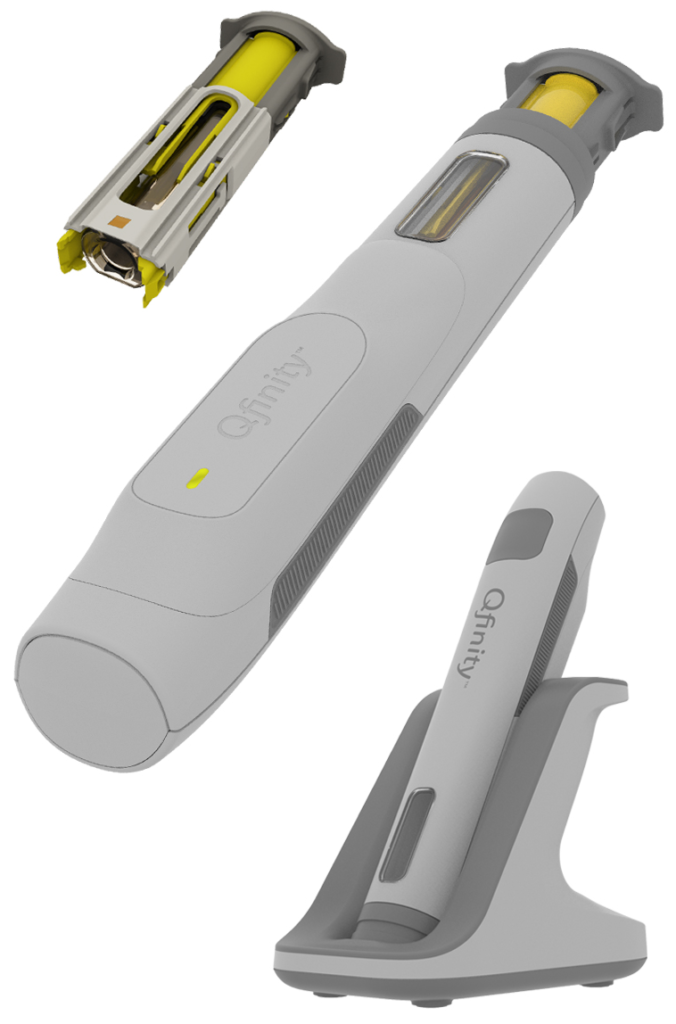
Figure 3: Jabil’s Qfinity re-usable autoinjector employed sustainable design to reduce materials and provides over 100 injections per unit versus most injectors, which are single-use disposable.
The three important sustainability factors to consider during the concept-selection stage include:
1. Modular Design
Modular design is particularly important for the more complex connected or electronic medical devices that are increasing in the market today (Figure 3). It is crucial to consider how elements of the device that have specific medical waste disposal requirements (i.e. drug cartridges) can be separated from the overall device.
2. Component Reduction
A reduction of the component count or the amount of different material types in a device can have a large impact on how readily the device components can be introduced into the circular economy and the cost effectiveness of doing so. Reducing the size and amount of material in a device can have a positive impact on carbon emissions during transport, manufacture and assembly. With increased use of 3D-printed materials in medical devices, additive manufacturing can be assessed at the concept-selection stage to reduce component count and optimise material usage. This can be achieved through the use of lattice structures and organic features only possible in a 3D-printed design. Thus, the mechanical requirements of each component can be met with optimal material efficiency.
3. Device Disassembly
Advancing concepts that optimise the device for disassembly should be a key sustainability requirement assessed at the concept-selection stage. An important factor to consider here is at what point does disassembly of the device to recover the constituent components for the circular economy become less sustainable than shredding the device and sorting the material via mechanical or chemical means. This assessment will have a big impact on the optimal design concept selected and should be determined at the design requirements or concept-selection stage in consultation with subject matter experts in device recycling.
STAGE 2: DETAILED OPTIMISATION
Once a device concept is chosen, the next stage is a detailed optimisation of that design for the chosen manufacturing and assembly methods. For plastic medical devices that are produced at high volumes, a key area for improvement is the injection moulding process for plastic components.
Reducing the overall amount of material in the component by coring out features while maintaining part functionality is an important consideration. For manufacture of the moulded components, optimising runner systems to reduce material waste and selecting resins that have lower processing temperatures can also greatly enhance sustainability. Understanding the disassembly of the device is also key during this stage.
Design for Assembly
A standard approach to design for assembly (DfA) is to develop an assembly process flow and then optimise the part design to meet the assembly equipment, fixtures, feeding systems, vision systems and other interactions at each stage in the process flow. In the past, little consideration has been given to what happens to the assembled device after it is used.
When device sustainability is considered only after the device has entered production, it can bring many challenges. The device manufacturer is then swimming against the tide, attempting to separate out materials from a device that is not designed to be disassembled.
The sustainable approach is to understand the post-use economy for the device and design it so that materials can be easily separated and recovered for the chosen recycling method. This might necessitate a move away from assembly processes that chemically bond the materials together, such as ultrasonic welding or laser welding. These processes also have high energy requirements that can contribute to a larger manufacturing carbon footprint.
Jabil Healthcare recommends the following:
- Avoid the use of lubricants or solvents that can contaminate waste streams and reduce the value of the device as a circular asset.
- Reduce the use of screws or bolts that will make disassembly more time-consuming. If screws are required, ferrous materials are optimal so they can be magnetically separated during recycling.
- Avoid the use of inks or painting of parts that can contaminate whole plastic batches. Consider processes such as in-moulded marking or laser marking as alternatives.
- Consider the use of shape memory resins in device clipping mechanisms. These can be designed in such a way as to secure the device enclosure during use but also facilitate easy disassembly by heating the device post-use.
A “global returns” system is also key here, so that devices can be received back to the manufacturer after use and they can then become a circular asset that can be re-used, recycled or refurbished. Of course, there is a point reached where the time, effort and energy required to disassemble a device become too high and focus should be diverted to optimal design for a device that will be recycled via shredding and separation. In this instance, material selection during the detailed simulation stage will be the higher priority.
STAGE 3: DETAILED SIMULATION
Material Selection
Optimising component material selection is valuable to achieve a sustainable design. But understanding the most sustainable material to progress forward at the early design stage can be difficult. Jabil Healthcare worked with partners to develop a database that compares different material options and helps with the selection of the most sustainable material for each component in the early design stage. This assessment includes:
- Recycling method
- Environmental impact of the material production
- Carbon footprint of the supply chain for the material
- The material supplier’s sustainability credentials
- The predicted outcome for the material post-use (i.e. landfill, waste-to-energy, circular economy).
Figure 4 shows the step-by-step process in action:
- The component requirements are compiled
- A list of materials that meet all component requirements is generated
- Datasheets from these materials are uploaded to the sustainability database
- This information is disseminated to network partners in the circular economy
- The sustainability credentials of material production and material suppliers are assessed
- Feedback from network partners and material suppliers is reviewed and the most sustainable material choice for the component is approved to move forward.
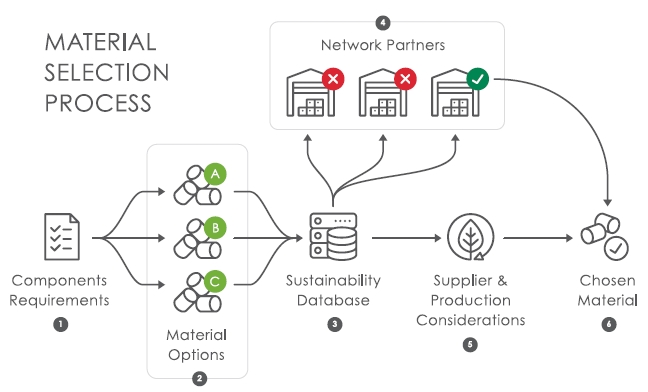
Figure 4: Jabil Healthcare’s material selection process.
For single-use plastic devices, understanding the environmental impact of the resin production is also important. Use of recycled material continues to be challenging due to the risks of contamination and material traceability. Companies such as Borealis (Vienna, Austria) are working on operations in advanced recycling to return plastics back to their basic monomers, which would be suitable for medical device manufacture. But there are economies of scale required that make this challenging in the short term.4
For resins, in particular, the feedstock used is critical. One way of transitioning away from fossil fuel feedstocks is to use a mass-balance approach. The mass-balance approach is a method of linking sustainable feedstocks to end products.5 It enables a shift away from fossil fuel feedstocks to a more sustainable circular economy. This system requires resin manufacturers to gradually use more and more bio-based or circular feedstocks in products. It is a similar process to how “green energy” initiatives work, with some of the electricity in the grid coming from renewable sources and some from fossil fuels. For example, there are now sustainably produced medical-grade materials, almost identical to the existing product but made up of 95–100% biocontent (biogas). These materials have typically less than 50% of the carbon footprint of the original materials produced from fossil fuels.6 This gives the medical device designer the option to select more sustainable materials that meet the same performance criteria.
CONCLUSION
Producing a sustainable medical device is not without its challenges. By tackling this problem at the early design stage, there is maximum flexibility to optimise device sustainability with minimal impact on project timelines and cost. To do this effectively, Jabil Healthcare recommends integrating sustainability into all aspects of the early-stage design process, starting at the concept-selection process, by only progressing the most sustainable concepts. By following a DfA process, where the device is optimised for disassembly and component segregation after use and through a materials selection process that preferentially selects sustainably produced and recyclable materials for each component. By implementing a thoughtful design-for-sustainability process, product developers can ensure that future medical devices not only improve patients’ lives but are also kinder to the environment.
REFERENCES
- Perkins B, “Shifting sands: The rise of consumer sustainability”. Deloitte, 2020.
- “Single-Use Medical Device Reprocessing Market – Growth, Trends, and Forecasts (2019–2024)”. Mordor Intelligence, 2019.
- Haller K, Lee J, Cheung J, “Meet the 2020 consumers driving change”. IBM Research Insights, 2020.
- Tullo A, “Plastic has a problem; is chemical recycling the solution?”. Chemical & Engineering News, 2019, Vol 97(39).
- Veasey R, “Sustainability & Drug Delivery Devices”. ONDrugDelivery, Issue 112 (Sep/Oct 2020), pp 6–9.
- “Strategy on Plastics in a Circular Economy / 2017”. The European Commission, 2017.