To Issue 151
Citation: Beckstoffer D, “Incorporating Motion Design at Early Stages of Wearable Injector Development”. ONdrugDelivery, Issue 151 (Sep 2023), pp 42–45.
Dave Beckstoffer discusses the often overlooked importance of including motion system design considerations from the very earliest stages of wearable injector development, and how doing so can reduce costs, shorten timelines and improve patient outcomes.
“If the motion solution design is not considered from the outset, subsequent design steps can be impacted, or even constrained, which can result in a compromise that could otherwise be avoided, or else require additional reworks.”
Engineering teams developing wearable drug delivery systems have a host of design considerations, so planning the motion solution is commonly not reviewed in the early stages of development. However, motor, gearbox and feedback specifications have far-reaching implications for the overall device design. Involving motion solution development at the outset can lead to a more efficient development programme, as well as a better outcome for the patient.
The motion solution driving a wearable drug delivery system plays a vital role in accurately actuating the injector for effective disease management. This means that, when designing a wearable system, the motion solution must be considered at the outset. Furthermore, motion solution specifications can have a far-reaching impact on the overall wearable injector design.
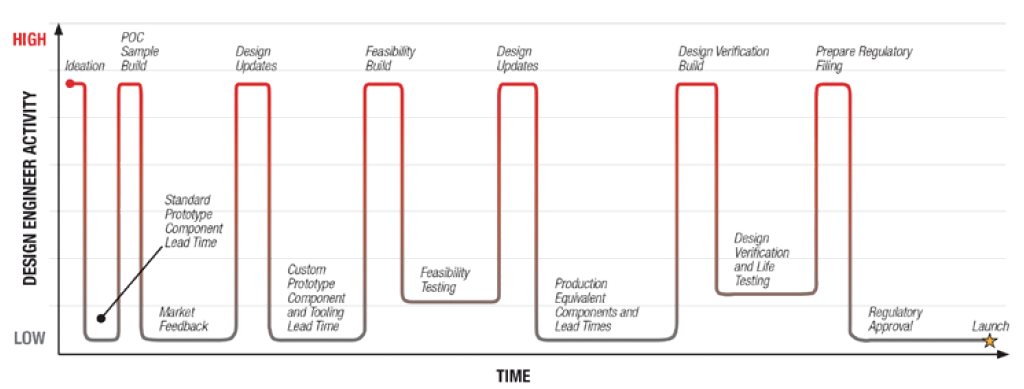
Figure 1: Ideal designer/engineer activity timeline. Involving a motion solutions provider from the initial ideation is key.
Therefore, it’s crucial to involve motion system considerations as soon as possible within project development (Figure 1). This can help deliver an efficient and timely schedule, both for the engineering team and the pharmaceutical company. Ultimately, this approach will also ensure the best experience for the patient by optimising the usability of the drug delivery system itself.
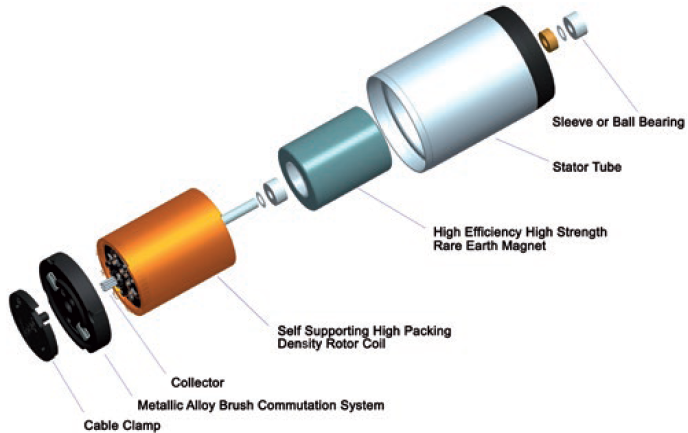
Figure 2: Exploded view of brush DC coreless motor.
Whether a design contractor is creating a wearable device for one-to-one administration of a single drug, or a manufacturer is designing a system that can inject a range of drugs with differing viscosities, optimising the speed of the product development stage is paramount. When executed correctly, it will help ensure that the pharma product and device follow the same timeline, while reducing the costs and resources required by the developer. However, to achieve this, accurate and realistic planning is required from the start to avoid unnecessary design iterations and delays.
To achieve the best project outcome, the design of the motor, gearbox and feedback options should be included from the outset. Though a wearable injector will typically be powered by a DC motor (Figure 2), specifying the full motion solution involves an array of options that have implications for each following project stage (Table 1).
Brushed DC Coreless Technology | ||
Concept Detail | Motor Characteristics | Application Benefits |
Ironless Rotor | Low moment of inertia | High acceleration, linear speed-torque function is ideal for incremental motion |
No hysteresis and eddy current losses | High efficiency, low losses – optimal for battery operation | |
No magnetic saturation | High peak torques – overcome initial friction of delivery | |
Central Stator Magnet | High power per size and weight | Compact form factor of device |
Low starting voltage | Minimised battery size | |
Precious Metal Commutation System | Low friction, little electrical noise | Low losses and wear – extended device life |
Table 1: Benefits of brushed DC coreless technology for wearable injectors.
INCLUDING MOTION DESIGN FROM IDEATION
When the engineering team begins ideation, the motion designer should ideally be involved in the first phase of development. Even though this creative stage typically introduces various project options, the potential approaches for drug delivery are highly dependent on motion system development. This means that, if the motion solution design is not considered from the outset, subsequent design steps can be impacted, or even constrained, which can result in a compromise that could otherwise be avoided, or else require additional reworks.
Looking in more detail at how motion development impacts ideation, a key aspect in the design consideration of a wearable device is the mode of drug delivery. This includes a decision on the preferred mechanism, such as a syringe plunger or a peristaltic pump, combined with an understanding of the ideal delivery scenario and duration.
To optimise the patient experience accordingly, the overarching criteria for wearable injector design includes size, weight and form factor. The motion solution specification, including its requirement for battery capacity, is crucial to meet these fundamental requirements. Additional considerations before and during therapy, including storage conditions, lifespan and patient usage, may also impact the motion solution selection.
From a drug performance and safety perspective, the level of accuracy required in drug delivery must also be determined at the ideation stage. This can combine the timespan and phases of the injection cycle with the force requirements contingent on drug viscosity. These crucial attributes depend exclusively on the motion solution specification.
“It is also fundamental to optimise motion control performance, particularly when high accuracy is important.”
ESTABLISHING A REALISTIC SCHEDULE
Motion solution considerations could be handled post-ideation, but doing so usually comes at a cost. As a result of the impact that motion specification has on both the wearable injection system’s performance and the overall device, considering motion design at a later stage could impose changes at a more critical time in project delivery.
Establishing a realistic project schedule is another reason to include motion solution design during ideation. Considering the extent of design decisions that the choice of motion system has ramifications for, the involvement of a motion designer from the outset, and the experience they bring, will help create a more reliable development pathway. The motion designer’s experience can also be useful for clarifying the number of design iterations realistically required.
CONFIRMING MOTION SPECIFICATION AT THE CONCEPT STAGE
Progressing to the concept stage, the objective of the engineering team is to formalise and clarify the proposal to resolve general challenges. Even though this stage is necessarily broad, and more than one proposal for achieving the objective might still be on the table, the design and timescale can be impacted adversely later if fundamental parameters haven’t yet been confirmed.
For motion solution design, when the concept phase is reached, an off-the-shelf motor, gearbox and encoder solution is typically introduced as the initial testbed. However, if the engineering team isn’t sufficiently concentrated on motion requirements during ideation, an oversized specification is normally used. This is based on the rationale of starting with a system that can drive the injector or pump at concept, based on mathematical calculations and prototype parts, and then scaling it down accordingly later in the process to optimise the design. However, it is key at this stage to accurately determine the torque and speed requirements – the fundamental aspects of motion specification.
Equipped with accurate data across each motion cycle, a designer is in a much stronger position to request further enhancements from the motion supplier to meet the overall objectives, such as reduced weight, more compact dimensions or greater energy efficiency. By confirming motion control performance at this stage, the design can build from a foundation that provides a head start and a smoother way towards achieving wider benefits.
CONFIRMING REQUIRED MOTION PERFORMANCE
The simplest way to determine motion performance requirements for a wearable device is to measure the current in the device as it is running through the different delivery cycles and flow rates. This will give a comprehensive and accurate assessment of the generated torque and duration for each working point. In a syringe drive, for example, there is typically a peak torque requirement as it overcomes friction, followed by torque stabilisation as the drug is delivered. Once the complete drug is delivered, the retraction phase requires a reduced torque level. This motion cycle assessment should be completed for each drug the injector may be required to dispense.
It is also fundamental to optimise motion control performance, particularly when high accuracy is important. The feedback system, and where measurements should be taken, also need to be specified at the concept stage to ensure accuracy.
The feedback point is typically positioned behind the motor – this is nearly always the case with an off-the-shelf motion solution. This means that the feedback device measures the rotational position of the motor as it turns and provides resolution of the rotation generated by the subsequent gearing system. However, with the feedback device located in this pre-motor position, inaccuracies in the position of the lead screw driving the syringe may not be detected. Dependent on priorities, this consideration can inform where the feedback device should be installed, and even whether dual feedback, covering both the motor position and lead screw actuation, might be required.
One advantage of motion development at the concept phase is that these considerations will inform whether an off-the-shelf design can meet project requirements or if a custom solution is needed. Understanding this requirement before moving into the feasibility stage will save time by reducing the amount of design planning required during later design phases, which are typically more complex and less adaptable, resulting in increased effort being required for any reworks.
EARLY MOTION PLANNING CAN REDUCE THE FEASIBILITY TIMESCALE
Feasibility is the longest stage for any project, with the objective of confirming and fixing the design to make it ready for validation and verification. Often within wearable drug delivery system development, the manufacturer or engineering contractor divides motion feasibility into two separate phases. Broadly speaking, the first phase of feasibility deals with confirming the motion performance specification and its required form factor. The second phase typically involves optimising the user experience, including optimisation of the motion solution within the wearable injection device.
However, when motion design has not been sufficiently involved at a prior stage, these two separate phases of feasibility usually proceed sequentially, rather than in parallel. This results in additional time and cost for design iterations, as well as a longer project timescale overall. In this scenario, the delivery device engineering team usually specifies the motion system, confirms it during the first phase of feasibility, and then approaches the motion supplier.
If, however, the motion specification hasn’t been confirmed with a full prior assessment of the motion cycles, the motion developer has the combined task of optimising both the motion performance and design integration at the same time. As this approach is likely to involve changes to the motor specification and the form factor, just as the wearable injection device engineering team expects to progress to device integration, the project has to take a step back and may require a design iteration of the motion system.
Instead, it is possible to run both phases of feasibility, including motion specification and integration optimisation, in parallel. If the motion solution designer is involved early enough, they can optimise the motion performance and fix the footprint. The form factor and actuation requirements of the drive mechanism then typically do not change significantly during feasibility.
This reiterates why it is crucial to confirm motion requirements, including torque, speed and the profile of the relevant cycles, sufficiently early in the project development. This will help avoid the need for fundamental design changes at a later stage that will have to be handled while trying to integrate patient optimisation changes.
PATIENT IMPACT
Fixing the design during feasibility enables the wearable injection system to proceed into the verification and validation stage. With the motion designer involved throughout, the device engineering team can progress to this stage with far greater speed and efficiency.
Ultimately, if the motion system is not optimised for delivery of the specific drugs, patient welfare will be impacted. Either an over-specified system will be used, thereby costing more than it needs to, or else it will be less likely to suit the needs of the patient. Considering the fundamental importance of a motion system to the usability of a wearable drug delivery system, involving a motion designer from the start is the most effective approach.