Citation: Chung L, Fluetsch G, “Developing a Fully Automated Modular Machine Platform for Autoinjector Testing”. ONdrugDelivery, Issue 123 (Aug 2021), pp 10–14.
Lucy Chung and Gilbert Fluetsch discuss the benefits of an automated modular test platform for autoinjectors.
Modularity is not a new concept in manufacturing. From cars and furniture to computers and software, products created using a modular framework are ubiquitous, and the benefits of a modular approach in design and manufacturing are well documented – particularly faster development, lower cost of goods, increased output and more flexible design options. However, in the pharmaceutical industry modularity only began to gain traction in the past 25–35 years in the form of modular bioprocessing production facilities.1 The key driver behind this adoption of modular manufacturing has been the shift from producing a single, blockbuster drug to instead producing a series of targeted therapies, which calls for smaller batches with lower costs and faster development.2,3
“A modular equipment platform uses a common base infrastructure that can be adjusted to process a mix of different products – or several versions of the same product – at speed, on a flexible scale and with consistent quality.”
As more pharmaceutical companies seek device solutions that can meet these new requirements, the impact of this shift is also evident in the drug delivery device industry. Over the past decade, preconfigured or platform products have been increasingly sought after due to their ability to offer faster turnarounds and lower costs with the use of common machinery and toolsets. Yet with rising competition in the space to launch biosimilar drugs, which often require customised designs for brand differentiation and usability requirements, devices are increasingly expected to offer flexibility beyond the confinements of a platform product.
MODULAR EQUIPMENT FOR AUTOINJECTOR DEVELOPMENT
In a 2020 article outlining the application of modular design thinking in autoinjector development, SHL Medical discussed how modularity offers the opportunity to leverage all the advantages of traditional platform device technology (e.g. in speed, cost and pre-set designs) while still allowing for various customisations in the device’s design and development models.4 The result is a flexible device platform that can meet the requirements for industrial design customisation and production scaling. These competitive advantages also apply to the automated equipment strategy for autoinjector assembly and final device testing.
Automated manufacturing refers to the design and application of a system that enables automatic processes in the production stream of device development. Integrated with computer-aided manufacturing (CAM)systems, automated machines offer a more efficient and cost-effective means of mass production. In most cases, these platforms are built for single blockbuster products that use dedicated manufacturing set-ups to lower the overall cost of goods. By contrast, a modular equipment platform uses a common base infrastructure that can be adjusted to process a mix of different products – or several versions of the same product – at speed, on a flexible scale and with consistent quality.
Besides the shift from blockbuster products to personalised treatments, this additional level of flexibility beyond high-volume production is also being driven by the nature of the pharmaceutical and medical device industry. Before a combination product is approved and launched on the market, it goes through numerous phases, including usability studies, clinical trials, pilot market testing and even sample requests from regulatory bodies for feedback and approval, all of which require different production volumes. Furthermore, as the product progresses through the different phases of its life cycle, forecasts and orders might also need to be scaled up or down to reflect changing market demand.
“When a unique test condition is required, such as shaking to simulate the drug product’s actual handling, an additional station can be added and programmed into the test sequence.”
BENEFITS OF A MODULAR AUTOMATED TESTING PLATFORM
SHL Medical’s in-house automation services are led by the automation systems department. The team has over two decades of experience designing, developing and building a wide range of manual, semi-automatic and fully automatic machine systems for autoinjector assembly, final assembly and final device testing.5 The majority of these systems are custom-built for single device projects for use internally or by SHL customers at their local sites. To put this into perspective, SHL has shipped more than 360 sets of assembly and test fixtures and equipment to 40 companies in 16 countries across Europe, Asia and North America.
SHL first developed a highly flexible and fully automatic testing machine (FATM) in 2017 after foreseeing the need to create a universal testing machine featuring flexible mix-and-match testing options for both syringe-based and cartridge-based injection devices. To achieve this, the company applied the modular design concept to its well-established FATM infrastructure, drawing on its years of experience developing automated testing machines for a diverse scope of injection device projects. The result was a universal testing platform featuring interchangeable tools and fixtures for increased device compatibility. The platform also has a modular machine base that can be arranged and expanded for different test stations, as well as an integrated software program that simplifies the customisation of test sequences.
In addition to increased flexibility and versatility for devices and testing items, other key benefits enabled by the modular FATM include:
- Faster turnaround for testing equipment development
- Lower costs through investment in tools and fixtures as opposed to entire lines of machinery
- Increased testing efficiency with automated processes
- More stable testing quality due to fully automatic handling
- The opportunity to scale production up (or down) for product lifecycle management
- The ability to introduce incremental upgrades
- Reduced equipment downtime
- Reduced overall carbon emissions per device by maximising the reuse of machine tool frames.
Before the introduction of the modular FATM, each new testing machine had to be customised for every new device project based on its individual design, test parameters and output requirements (Table 1). With the introduction of a modular machine base, however, semi-automatic testing machines (SATMs) can now be developed as standalone test stations that can work independently or be assembled with other stations to form a customised test sequence.
Type | Manual testing machine (MTM) |
Semi-automatic testing machine (SATM) | Fully automatic testing machine (FATM) |
Image | ![]() |
![]() |
![]() |
Description | Integrated system with interchangeble tools |
Modular SATM station with interchangeble tools |
Modular FATM platform with interchangeble stations |
Key benefits |
|
|
All the same benefits as SATM with the addition of:
|
Table 1: Overview of testing machines.
By supporting the flexibility to mix and match different test stations, the modular FATM platform enables new test sequences to be arranged according to each product’s requirements.
For example, a two-step, syringe-based autoinjector such as SHL Medical’s Molly would require the simulation of two main actions: a pulling motion to remove the cap and a pushing motion to activate the injection. Meanwhile, a cartridge-based autoinjector that requires the user to shake and mix the drug prior to injection would involve a more complex series of test sequences, as illustrated in Figure 1.
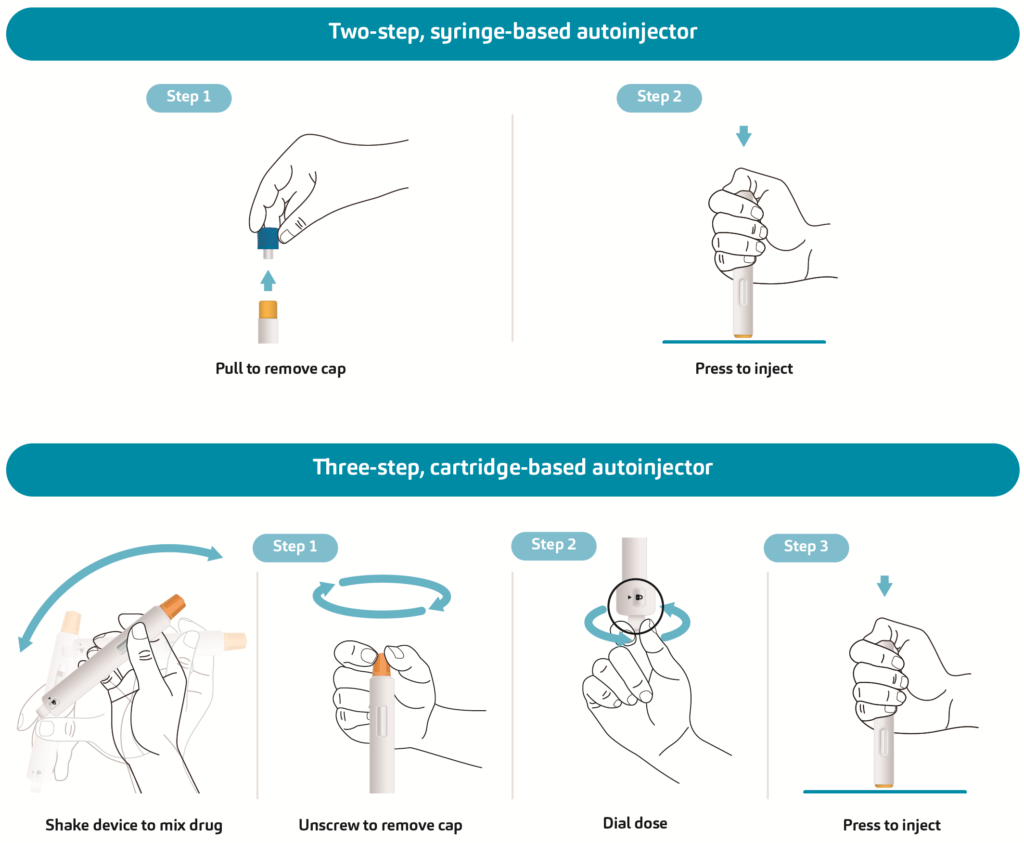
Figure 1: A simplified comparison of the test items for a syringe-based autoinjector and a cartridge-based autoinjector requiring mix before use. Other available test items, such as needle length, injection time, dose accuracy and needle cover override force, are not outlined.
THE LEGO-LIKE APPROACH TO MACHINE MODULARITY
“Autoinjectors do not need to be perfectly positioned in a designated area for the robot arm to be able to initiate the testing process.”
Despite the difference in test sequences, the same test items – such as cap removal force, injection activation force and injection test – could be tested on the same machine base wherein specific tools, such as grippers, holders and nests, can be swapped out for different devices. Furthermore, the software can be easily configured to define the intricacies of the test sequences. When a unique test condition is required, such as shaking to simulate the drug product’s actual handling, an additional station can be added and programmed into the test sequence.
This ability to endlessly combine various elements to create “new” equipment can be best understood through Lego bricks − one of the world’s most recognisable examples of modular design.
Modularity is impossible without some level of standardisation. Much like how Lego bricks can be combined and taken apart, individual machine stations are designed to be mutually compatible so they can be disassembled and reassembled. This standardised design serves as the framework within which flexibility is achieved (Figure 2).
Another key factor facilitating the system’s modularity is the addition of a robot arm. To accommodate the various add-on stations, a tailored control system was designed so that the robot arm can be easily set up to perform motions of various levels of complexity. To this end, SHL challenged its software engineers to extend the robot arm’s capacity beyond conventional pick-and-place functions to include capabilities such as loading and dispatching trays as well as safely removing glass beakers filled with liquid solutions and replacing them with empty containers before continuing the test cycle (Figure 2).
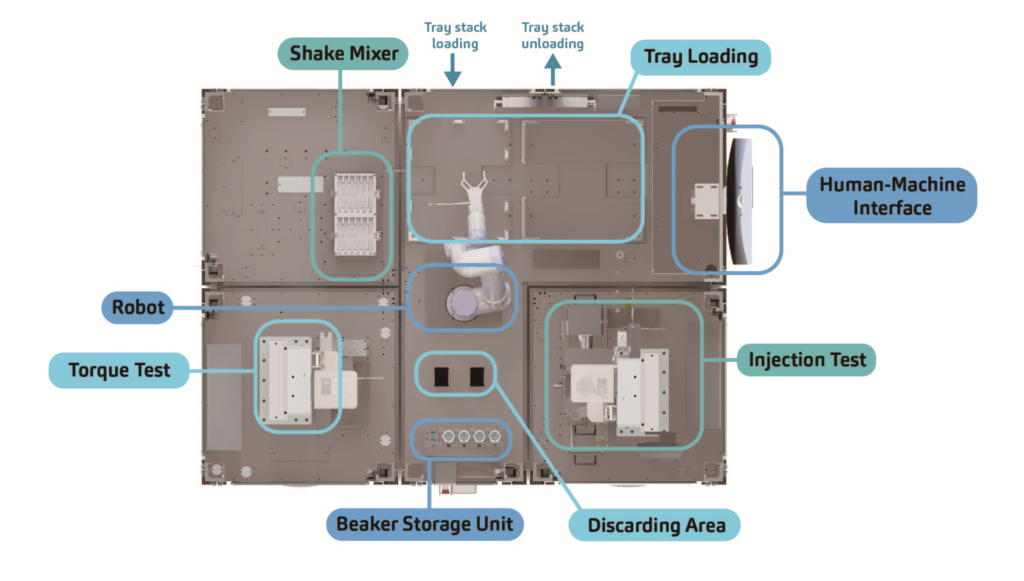
Figure 2: Top-view layout of a modular FATM for a cartridge-based autoinjector. Modular bases consisting of different test functions are assembled similarly to Lego bricks.
The difficulty for the engineers lay not just in characterising complex and intricate motions while avoiding hardware collisions but also in identifying all possible motions and integrating them into a single software system that could allow users to configure a complete test sequence with relative ease on the FATM’s human-machine interface. This user-configurable software system – which addresses a large number of possible use cases, each with their own configurable elements and settings – is what enables the Lego-like equipment stations to function as a fully automated modular autoinjector testing platform.
In a 2020 article, SHL discussed applications of deep learning in automated assembly machines.6 Deep learning has also been incorporated into the FATM’s robotic system to help further increase its flexibility. Specifically, SHL combined a visual guiding inspection system with deep learning capabilities for use at the outset of testing activities, namely the first step of picking up an autoinjector for further processing. A subset of machine learning in artificial intelligence, deep learning can mimic the human brain to detect objects and recognise shapes without the need for explicit data sets. It allows the robot arm to “teach itself” to distinguish the autoinjector’s features and automatically adjust its movements and trajectory in relation to the device’s positioning inside the tray (Figure 3). In comparison, a traditional control system would require the input of extremely specific instructions, such as length, width, colour and precise position, in order for the robot arm to accurately identify the object and move according to the predefined trajectory. In practical terms, this means autoinjectors do not need to be perfectly positioned in a designated area for the robot arm to be able to initiate the testing process.
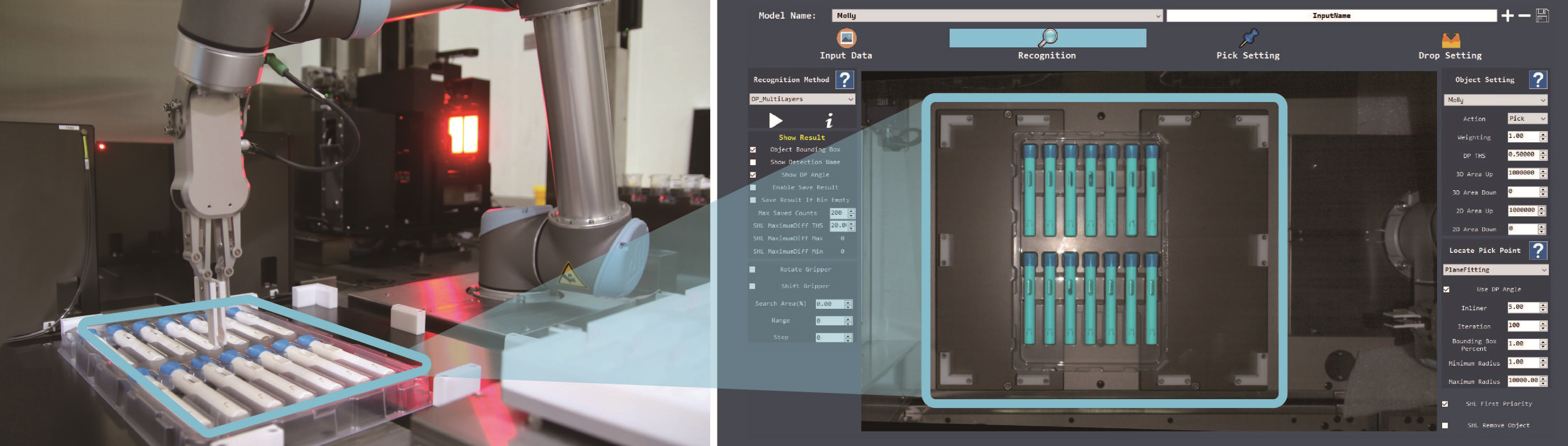
Figure 3: Side-by-side view of the tray and robot arm (left) and a screen capture from the artificial intelligence system (right). Through the integration of deep learning, the robot system can recognise unique device features and automatically adjust its movement in relation to the positioning of the devices inside a tray.
While this may seem a trivial task to assign to artificial intelligence, it in fact encapsulates the myriad benefits of modular FATMs outlined earlier. For example, autoinjectors of different shapes and sizes can be placed in trays that can themselves be of varying dimensions. With the system’s ability to learn and self-adjust to different device and tray parameters, developers no longer need to build separate equipment or fixtures for every device project that comes through their doors. This flexibility is paramount as it significantly enhances FATMs’ compatibility, enabling them to support autoinjectors with various industrial designs.
“By reusing much of the machinery to test different injection devices, emissions from producing and operating individual pieces of machinery are reduced, increasing the overall sustainability of the final product.”
THE FUTURE OF AUTOMATED TESTING
A modular equipment architecture, by definition, uses a common infrastructure that can be adjusted and reused for a variety of products. By reusing much of the machinery to test different injection devices, emissions from producing and operating individual pieces of machinery are reduced, increasing the overall sustainability of the final product.
Even though the syringe and cartridge autoinjectors shown in Figure 1 have vastly different device features and handling steps, they share approximately 60% of the modular equipment units when comparing their respective FATM set-ups. Looking further into the interchangeable parts, internal data also shows that the vast majority of the machine structure is reused, meaning that the effort and raw materials needed to assemble a modular testing machine for an individual product are also significantly lower than those needed to build a new machine from scratch for the same purpose. Of course, these are general observations, and different projects may yield different data.
While further research is needed to elucidate the precise carbon impact of a modular FATM on a product’s lifecycle, SHL will continue to refine its modular approach in both device designs and equipment strategies in order to fully realise the benefits that modularity presents to its customers and the broader community. As part of this commitment, the company has launched an industry-leading initiative aimed at enabling container-free testing for the fully automated modular machine platform. With this forward-looking initiative and others like it, SHL is taking concrete action to enhance its automation services and stay ahead of the demands of the drug delivery industry.
REFERENCES
- Hernandez R, “Modular Manufacturing Platforms for Biologics”. BioPharm International, 2015, Vol 28(5), 2015, pp18-25.
- Riley S, “Modular Manufacturing”. PMMI, Apr 2016.
- Rollings N, Barker C, Vellacott R, “Early Insight: A Flexible, Modular Platform to Disrupt the Blockbuster Manufacturing Model”. ONdrugDelivery, Issue 103 (Dec 2019), pp 48–52.
- Wild L, Fuensalida Pantig GR, “The “Customisable Platform” Paradox”. ONdrugDelivery, Issue 113 (Oct 2020), pp 80–85.
- Fluetsch G, Chung L, “Expanding Automation Capacity for High and Low Volumes”. ONdrugDelivery, Issue 99 (Aug 2019), pp 6–9.
- Gertz F, Fleutsch G, “Applications of Deep Learning in Medical Device Manufacturing”. ONdrugDelivery, Issue 110 (Aug 2020), pp 6–11.