To Issue 168
Citation: Gossmann D, “The Role of Metal Deep-Drawn Parts in Medical Devices for Drug Delivery”. ONdrugDelivery, Issue 168 (Jan 2025), pp 100–102.
Dennis Gossmann discusses the benefits of using deep-drawn metal components in drug delivery devices and how STÜKEN MEDICAL, as an established expert in this field, can be an ideal partner for manufacturing and supplying these parts.
In the field of drug delivery, the choice of materials and manufacturing processes plays a critical role in ensuring device reliability, safety and performance. Deep-drawn metal components, particularly those made from stainless steel and titanium, have become indispensable in this respect due to their exceptional biocompatibility, strength and corrosion resistance. These properties are crucial for components that must withstand contact with bodily fluids, resist mechanical stress and endure sterilisation processes – typical requirements for drug delivery systems such as autoinjectors, inhalers and insulin pumps.
“The deep drawing process is ideal for manufacturing metal components for the medical device industry, as it enables the production of parts with highly precise tolerances and complex geometries.”
The deep drawing process is ideal for manufacturing metal components for the medical device industry, as it enables the production of parts with highly precise tolerances and complex geometries. This precision ensures that critical components such as canisters, housings and drug reservoirs maintain consistent performance, which is essential for the accurate dosing and delivery of medication. Additionally, the seamless design provided by deep drawing eliminates potential contamination points, offering enhanced reliability in devices where any failure could compromise patient safety.
Moreover, the deep drawing process is highly scalable and cost-efficient. Once the tooling is in place, manufacturers can produce large volumes of parts with minimal material waste, making it a practical choice for mass production. This scalability ensures that even intricate parts remain cost effective over time, which is vital in the competitive landscape of the drug delivery market.
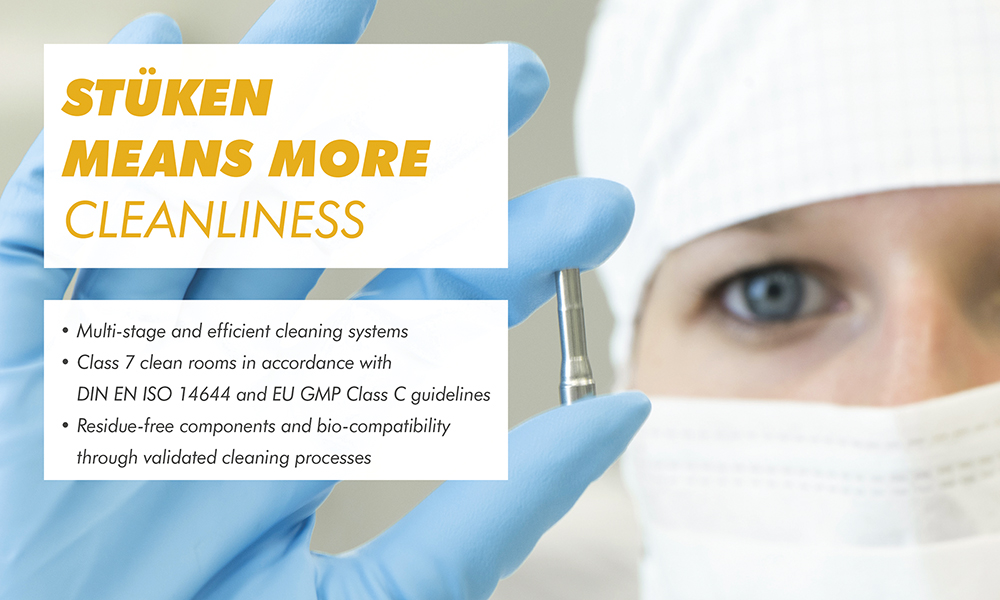
Figure 1: STÜKEN MEDICAL ensures required cleanliness with validated cleaning processes and Class 7 cleanrooms.
“As a leading partner in this field, STÜKEN MEDICAL is renowned not only for its expertise in manufacturing deep-drawn metal components for the medical industry but also for offering a comprehensive range of value-added services.”
As a leading partner in this field, STÜKEN MEDICAL is renowned not only for its expertise in manufacturing deep-drawn metal components for the medical industry but also for offering a comprehensive range of value-added services. These include passivation according to industry standards, ensuring optimal corrosion resistance, as well as plating and laser welding for customised component finishes and functionality. STÜKEN MEDICAL also provides packaging in ISO Class 7 cleanrooms (Figure 1), which is essential for maintaining the cleanliness of parts used in sensitive drug delivery devices.
Additionally, STÜKEN MEDICAL is ISO 13485 certified, affirming its commitment to meeting the highest quality and regulatory standards in medical device manufacturing (Figure 2). The company’s full suite of capabilities – from deep drawing to post-processing and assembly – makes it a one-stop partner for producing not just components but complete, ready to- use solutions tailored to the stringent requirements of drug delivery systems.
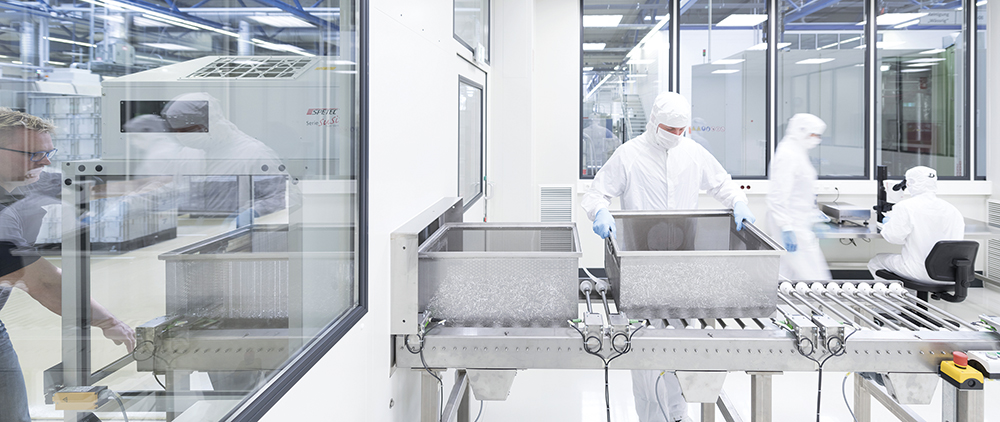
Figure 2: STÜKEN MEDICAL operates Class 7 cleanrooms in accordance with DIN EN ISO 14644 and EU GMP Class C guidelines.
“STÜKEN MEDICAL has a dedicated team ENSURING that the focus is always on the customer’s requirements – for example, with comprehensive customer service and innovative technical support in the development phase.”
STÜKEN MEDICAL’s innovative production techniques and state-of-the art facilities enable the manufacturing of complex, custom-designed components tailored to meet the specific needs of drug delivery systems (Figures 3 & 4). Its commitment to quality, coupled with its capacity for cost-efficient, high-volume production, positions STÜKEN MEDICAL as a trusted partner for medical device manufacturers worldwide. On top of this, STÜKEN MEDICAL has a dedicated team ensuring that the focus is always on the customer’s requirements – for example, with comprehensive customer service and innovative technical support in the development phase.
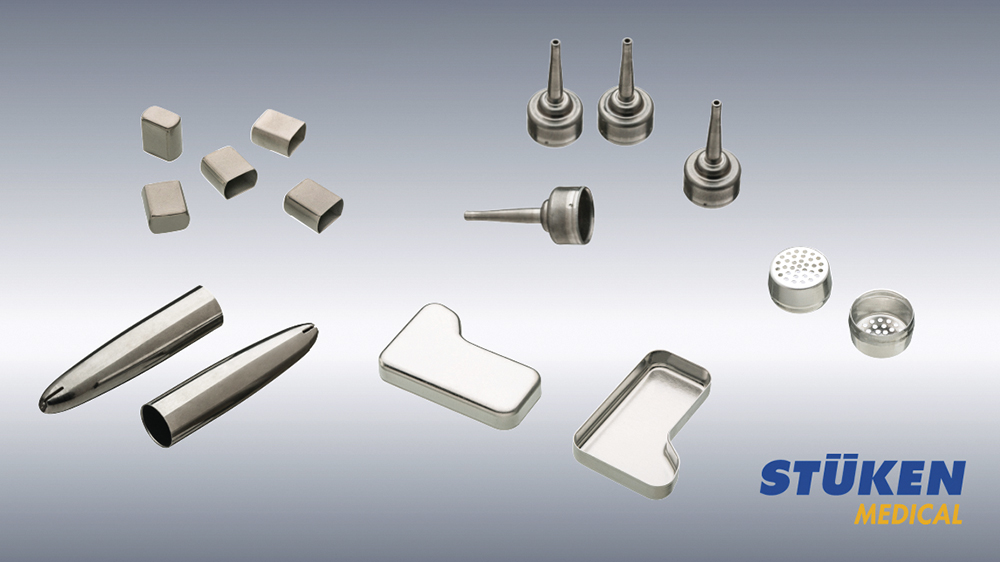
Figure 3: STÜKEN MEDICAL delivers a wide range of product sizes and geometries.
In conclusion, deep-drawn metal components offer unmatched advantages for drug delivery devices. With their superior material properties and the precision offered by the deep-drawing process, these parts ensure device safety and performance. STÜKEN MEDICAL’s expertise, coupled with its wide range of value-added services and ISO 13485 certification, makes it the go-to partner for manufacturers looking to create reliable and effective drug delivery systems.
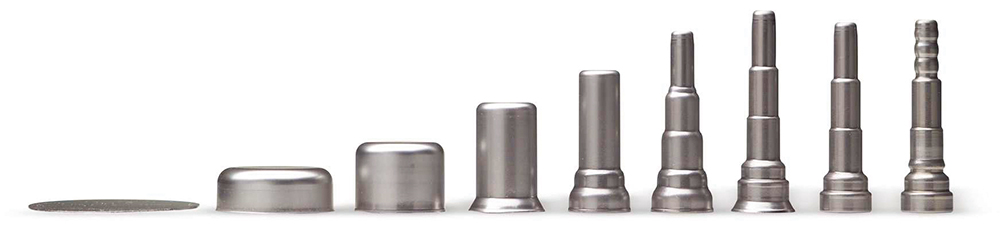
Figure 4: STÜKEN MEDICAL produces deep-drawn components with dimensions <1–92 mm in length.