Citation: Chen C, Chang I, “Automating High-Mix, Low-to-Medium-Volume Autoinjector Assembly”. ONdrugDelivery, Issue 163 (Jul 2024), pp 40–45.
Colby Chen and Ian Chang discuss how the introduction of modularity can close the gap in traditional assembly systems to enable fully automated, high-quality autoinjector assembly in support of low- volume/high-mix manufacturing.
In the modern pharmaceutical landscape, the scope and speed of drug development have grown tremendously, resulting in more products being developed and launched across both large and emerging markets. Pharmaceutical companies continuously strive to expedite market entry and often face the need to scale production within stringent timelines corresponding to the preclinical, clinical and commercial phases, however, the race does not stop there. Depending on the post-launch success of the combination product, among other factors, such as potential expansion into new therapeutic applications and new markets, pharmaceutical companies may need to rapidly adjust production scales and implement additional marketing strategies. These strategies could include introducing the same molecule under a region-specific brand or expanding the product label to ensure sustained market access and profitability.
These factors not only affect pharmaceutical companies but also impact the entire pharmaceutical value chain, including drug, container, device and packaging manufacturers and suppliers. Equipment suppliers, often at the end of the value chain, are being challenged to enhance their equipment’s agility to meet project and manufacturing flexibility requirements while keeping production streamlined without compromising quality and efficiency, particularly for high-mix/low-volume manufacturing.
OVERVIEW OF ASSEMBLY SYSTEMS
“The adoption of automated technologies to assemble medical devices such as autoinjectors and pen injectors is not a new concept.”
The adoption of automated technologies to assemble medical devices such as autoinjectors and pen injectors is not a new concept. SHL Medical’s records show that its first semi-automated, machine-assisted assembly machine was developed as early as 2001 for the assembly of a prefilled pen for the treatment of hepatitis C. A review of the supplier landscape also reveals a plethora of assembly machines and solutions for medical device sub-assembly and final assembly. However, a closer look at current market solutions indicates that low-to-medium volume manufacturing has primarily been limited to machine-assisted manual assembly or semi-automated assembly systems, both of which are highly reliant on operators (Table 1). This limitation stems from the relative speed and lower financial thresholds needed to implement these technologies to meet the fluctuating demands of the pharmaceutical industry. Conversely, while fully automated assembly systems offer enhanced productivity, consistency and efficiency, they have historically been confined to large, complex projects due to their longer development timelines and higher initial costs.
Assembly method | Manual | Semi-automated | Fully automated |
Example Machine |
![]() |
![]() |
![]() |
Output | Low (>2 PPM) |
Mid (<20 PPM) |
High (>60 PPM) |
Pros | • Cost effective for smaller batches • Shorter development lead time • Relatively easy to adapt for multi-device compatibility |
• Compact solution for mid-volume output • Integrated quality controls |
• Used for high-speed, high-volume output • Integrated quality controls • Operator-independent |
Cons | • Operator-dependent • Possible variation from manual processes |
• Operator-dependent • Limited flexibility for multi-device compatibility |
• Higher initial investments • Limited flexibility for multi-device compatibility |
Table 1: Overview of prevalent autoinjector assembly systems showing SHL-built assembly machines as examples.
With low-to-mid-volume manufacturing highly reliant on a company’s ability to recruit sufficient labour at reasonable costs, the traditional trade-off between full automation and operational flexibility presents new challenges for equipment providers. They must now develop fully automated assembly systems that incorporate production scalability, project flexibility and programme adaptability for smaller batch production.
To close this gap, SHL has developed the semi-modular automatic robot track (SMART), a fully automated, modular assembly machine that combines the flexibility of manual assembly processes with the reliability of fully automated processes. Designed for mid-volume production, the SMART can reach an annual capacity of 7.5–10 million devices using at least two to three times less labour compared with manual assembly set-ups. It can also be adapted to assemble various devices, such as the Molly® 1.0 and 2.25 autoinjectors, on the same equipment.
A SMARTER ASSEMBLY MACHINE
Modularity in automation equipment is not a novel concept, and SHL has long been developing its automated testing and assembly equipment with modular infrastructures. For example, SHL’s modular fully automated testing machine, introduced in 2019, was recognised for its innovation as a finalist in the 2022 CPHI Pharma Awards in the Manufacturing, Technology, and Equipment category.1,2
Designed as a fully automated alternative to manual assembly lines, the SMART’s innovation lies in its use of modularity to seamlessly converge physical components and modules with digital controls to enable versatile assembly operations and efficient project changeover. This is of particular importance as autoinjectors can comprise anywhere between one to several dozen components, each with vastly different shapes and dimensions – a feature that has historically hindered the accommodation of greater versatility in fully automated autoinjector assembly machines.
The SMART features movable base frames with fully extendable linear tracks, housing robots on each side to create a modular station. Each station seamlessly integrates with a range of standardised material in- and out-feeding modules, such as tray feeders, bowl feeders, direct in-line spring feeders, and primary container tubs and rondo trays (Figure 1). These modules are designed for faster development, shorter engineering and site/factory acceptance test lead time, as well as quicker response and technical support. To enhance the SMART’s versatility and decrease downtime during project changes, it also features a patent-pending Quick Tool Change interface that allows users to swiftly exchange project fixtures with the flip of a release handle.
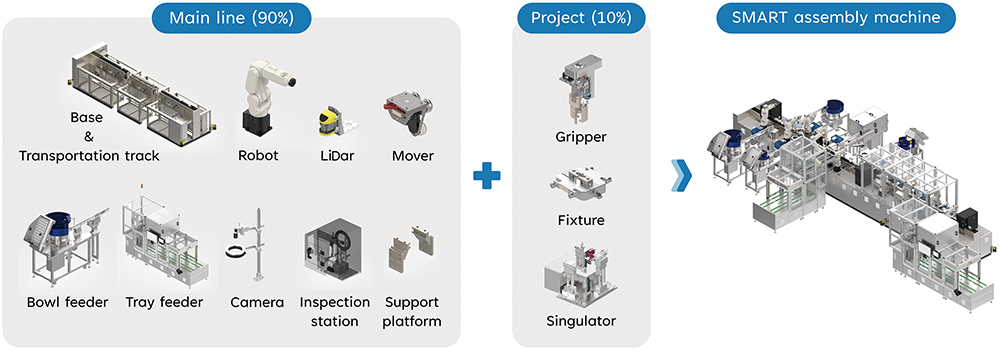
Figure 1: Non-exhaustive key reusable and project-specific modules of a SMART assembly machine.
In addition, the SMART’s modularity also aligns with SHL’s commitment to sustainability. Internal data looking at the quantity of listed parts show that up to 90% of the main machine structure can be reused when switching between different device projects (Figure 1). While the percentage of reusable modules may vary depending on the level of each project’s distinctiveness, reusing much of the machinery to assemble different devices may significantly reduce the environmental impact compared with producing and operating individual machines.
DESIGNS BEYOND MODULARITY
With the goal to maximise the SMART’s modularity, SHL took a step further in rethinking how modularity could enhance machine efficiency. During early development, the company assessed the necessity of each module and explored opportunities for combining functions. For example, modular units are usually designed based on two principles. The first considers the maximum variety of functions or configurations and combines them into a single modular unit. This overarching approach ensures that all the possible outcomes are considered and integrated into the design. Take the Swiss Army knife as an example. It combines multiple tools, such as blades, bottle openers, screwdrivers, even butane lighters, into a single multifunctional unit to cater for diverse needs. While Swiss Army knives come in various models, each in different sizes and tool combinations, the core traits of versatility and functionality remain consistent thanks to its modular base design.
The second principle, in comparison, takes a granular look at each singular function to determine how different configurations can interconnect via a standardised or partially standardised interface. The most common example of this principle is the universal serial bus (USB) port. With a standardised physical interface, a range of electronic modules can seamlessly connect to one another to achieve different functions, such as data transfer, power supply and internet connection.
While seemingly disparate, the two principles are complementary in that, together, they enhance the robustness of the final product. This is because the first overarching principle ensures product versatility, while the second principle of granularity makes it possible to add new features or functions that were not considered at the outset of the design phase. By applying these two key principles, SHL thoroughly analysed and optimised each SMART module, both individually and collectively, resulting in innovative strategies that improved overall machine performance.
“An example of innovative thinking beyond modularity lies in the SMART’s component transportation mechanism.”
ROBUST TRANSPORTATION
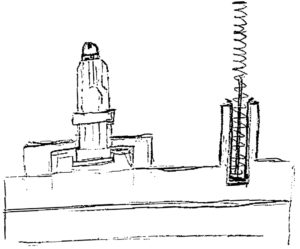
Figure 2: Hand drawing of the original RSA fixtures design, which placed two fixtures on a single base.
An example of innovative thinking beyond modularity lies in the SMART’s component transportation mechanism. During the assembly process for the rear sub-assembly (RSA), components are loaded onto a set of two fixtures (Figure 2) and transferred to different stations to complete the assembly sequence. Due to their features, some of these components require an additional module to guide or clamp them into position and ensure correct alignment prior to assembly. To eliminate the need for an extra guiding/holding unit, the clamping mechanism was integrated directly into the moving shuttles. This enabled SHL to optimise the overall assembly time, which improved both machine cost and efficiency.
With the decision to integrate the functions, the challenge then arose of how to effectively activate the clamping without compromising the SMART’s transportation. The first step was to separate the two fixtures into shuttle pairs for better weight distribution between each mover. The next step was to activate the clamping movement, allowing the clamps on one shuttle to be triggered by the physical movement of the other. Initial iterations explored a spring-based mechanism, but rigorous proof of principle and failure mode and effects analysis activities led the company to develop an innovative solution: a combination of computer-controlled and mechanically actuated movement. In practical terms, as seen in Figure 3, the two shuttles are connected via a linkage component. When Shuttle B moves towards or away from Shuttle A, it triggers the clamps to release or clamp, respectively. The movements are fully controlled by the computerised system to ensure optimal control and reliability of every movement.
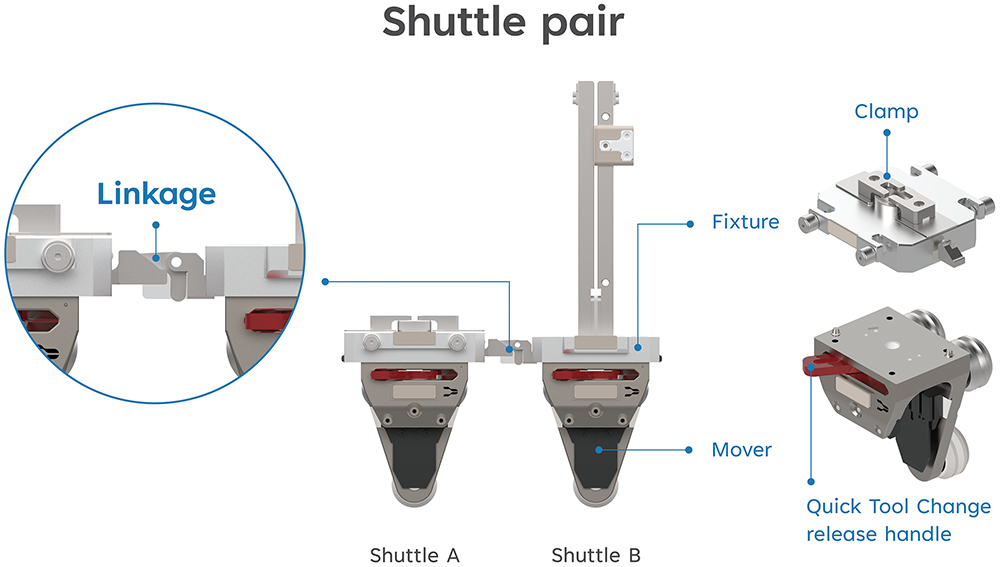
Figure 3: SMART shuttles with autoinjector RSA fixtures. The fixtures are separated into two shuttles with an inter-connected Linkage.
With the shuttle pairs connected, the third and final step was to ensure that they could move flexibly along the vertical circular track by automatically separating when they travel into the curve. While moving through the beginning of the curve, the first mover naturally tilts, creating a height deviation that results in the automatic separation of the two shuttles. The linkage connects again when the shuttles move horizontally side by side. The patent application for this innovative shuttle-based carriage guide rail system has been published in Europe, the US and Japan.
FLEXIBLE ROBOTS
The SMART’s maximisation of modularity is also demonstrated in its use of robot systems. Instead of the more prevalent three-axis, three-orientation pick-and-place units, six-axis robots are employed for both feeding and assembly activities. These robots stand out for their remarkable precision, flexibility and ability to adapt to diverse production requirements. Like the shuttles, the robots are affixed with grippers that can be easily changed for different projects. As articulated robots, they have multiple joints that allow for a wider reach, an advantage that was leveraged in combination with the use of safety light detection and ranging (LiDAR). By removing physical enclosures around the robots, more space is created for the robots to stretch out, allowing them to carry out additional tasks, such as removing rejected parts in a more efficient manner. This not only results in better use of space compared with traditional feeding and unloading pick-and-place units, the reduction of physical enclosures also results in easier access for troubleshooting as well as less material use.
“Having developed more than 1,400 sub-assembly and final assembly machines for various autoinjectors and pen injectors over the years, SHL understands the importance of speed and reliability when developing assembly systems for medical devices.”
MODULAR CONTROLS
Having developed more than 1,400 sub-assembly, final assembly and final device testing machines for various autoinjectors and pen injectors over the years, SHL understands the importance of speed and reliability when developing assembly systems for medical devices, regardless of the level of automation. The modularity of SMART also extends to its software and data control system. In brief, control systems comprise a mix of electrical, mechanical and computer engineering aspects. Serving as the link between the physical hardware and the digital software, control systems define how a machine part or module reaches the desired state and functions as intended.
Leveraging its extensive experience and wealth of assembly data, SHL has developed not just modular machine platforms, but also a modularised control system for all its latest sub-assembly and final assembly machines. Known as the SHL Control Library, the modular control system is a standardised, company-specific software development process based on the Packaging Machine Language (PackML) framework established by the Organization for Machine Automation and Control. As a robust standard that enables easier transfer and retrieval of consistent machine data, PackML makes machines more serviceable while facilitating greater reapplication of the software between different machines. It allows engineers to efficiently develop stable, project-specific programs that, at the same time, enhance usability for the end users.3
SHL’s Control Library encompasses a full spectrum of control modules covering the most common autoinjector sub-assembly and final assembly processes. The library consists of three main categories: modules, tools and human machine interface (HMI):
- Modules consist of commands for the physical modules related to the assembly machine, including robot arms, motors and inspection instruments
- Tools involves all non-physical execution components, such as data processing and file handling
- HMI consists of all functions used by end users to enable the rapid development of user-friendly software interfaces for different assembly projects.
With the modularised Control Library, a new SMART project can be developed and installed in relatively shorter timelines. For example, as illustrated in Figure 4, the main assembly processes (A–D) for autoinjectors are derived from the SHL Control Library. In practice, this means that when receiving the user requirement specifications for a new device project, the company can promptly assess the relevant assembly processes and develop the framework by integrating the pre-developed and validated functionalities from the library, deploying them into different machine systems. While there will still be project-specific processes that need independent defining, such as the exact robot positioning, this modular approach facilitates faster development not just for implementing new device projects on the same SMART machine but also for migrating an existing device project from a SMART assembly machine to a higher-volume, fully automated assembly machine platform, for example.
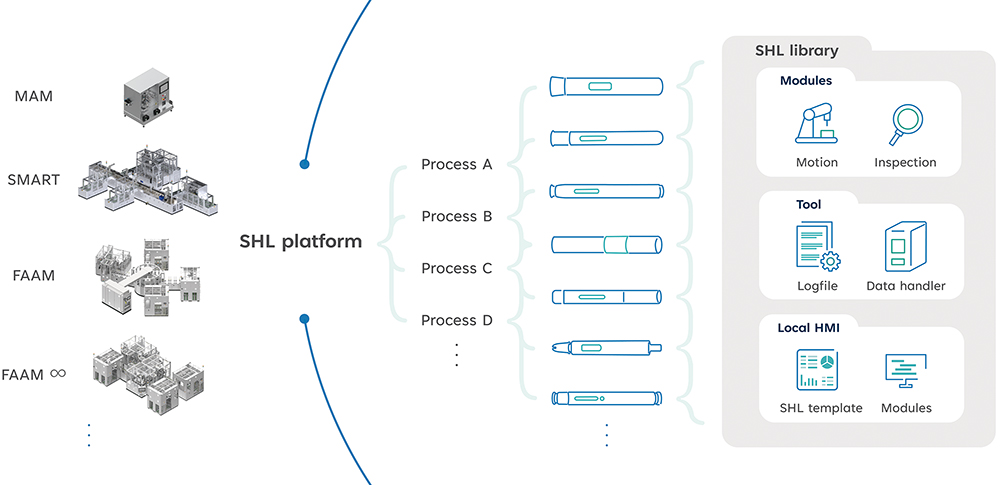
Figure 4: SHL Medical’s modularised Control Library facilitates faster development of new assembly projects across all of SHL’s device projects and assembly machine platforms.
“While consistent production quality is essential in any manufacturing process, it becomes particularly critical for self-injection devices as the final products are used by patients without direct supervision from healthcare professionals.”
INTEGRATED QUALITY
Another important benefit from using automation technologies for medical device assembly is the opportunity to integrate in-line quality measures to ensure the quality and repeatability of each manufactured product. While consistent production quality is essential in any manufacturing process, it becomes especially critical for self-injection devices as the final products are used by patients without direct supervision from healthcare professionals. SHL boasts extensive and comprehensive experience in applying in-line inspection modules, such as probes, laser sensors and vision systems, to its assembly machines – ranging from basic visual feature recognition for low-volume manual assembly machines to high-precision assembly quality inspections for larger, fully automated assembly machines with higher cycles. Whether it is to ensure the components are produced to specification or to help verify that the sub-assemblies are accurately assembled, in-line quality measures play a significant role in ensuring final product reliability, increasing yield, cutting downtime and improving process control.
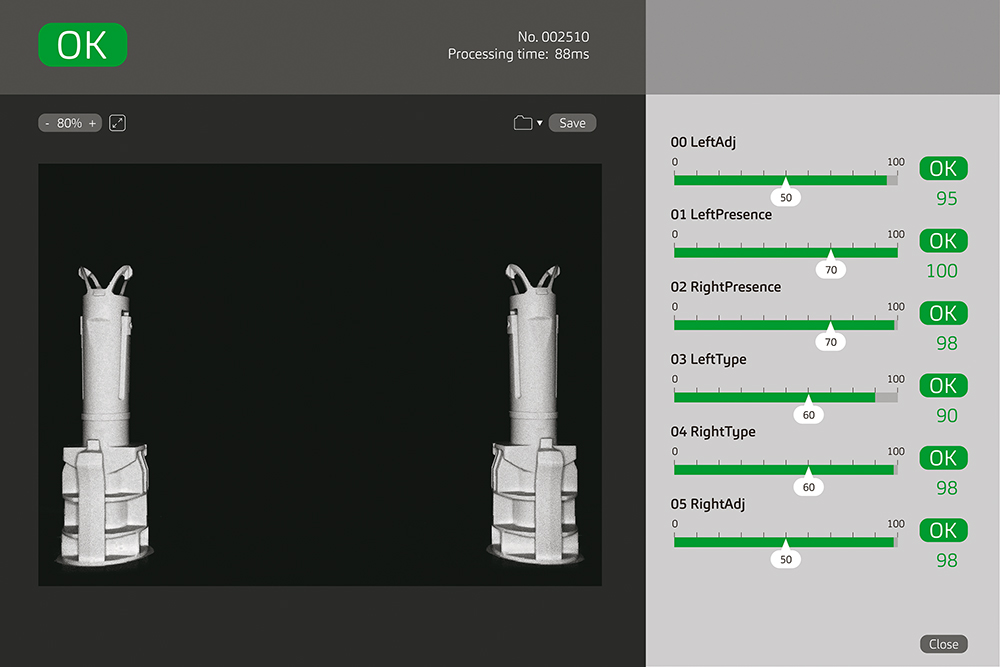
Figure 5: Image from a vision system. Once the pre-set parameters are met, the vision system clears the components for assembly.
As a fully automated assembly machine, the SMART is compatible with a selection of quality modules capable of performing various quality control measures, covering 100% of the components and sub-assemblies. For example, the SMART’s vision systems can be configured to execute a wide range of high-precision detection, measurement, monitoring and inspection activities for real-time control of the assembly process. Figure 5 illustrates the versatility of the integrated recognition system, including measurement of parameters such as deviation, exposure and binarisation threshold. Compared with manual inspections, these systems provide more consistent and accurate results at significantly higher speeds. They quickly adapt to changes and requirements for different products, demonstrating strong adaptability and flexibility. Automated vision systems also collect comprehensive statistical and image data, which can be used for tracking, analysis and continuous improvement using technologies such as artificial intelligence (AI) and deep learning.4
CONCLUSION
“Leveraging its inherent versatility enabled by a modular infrastructure, the SMART introduced full automation without altering the device design.”
In 2020, the SMART was selected for a newly approved molecule for atopic disorders – a combination product that leveraged SHL’s Molly 2.25 autoinjector platform. With the drug’s recent launch, production flexibility – as well as uncompromised quality – was crucial to the project. Leveraging its inherent versatility enabled by a modular infrastructure, the SMART introduced full automation without altering the device design. In addition, it seamlessly executed various quality control measures covering 100% of components and sub-assemblies.
The success of the SMART platform signifies SHL’s commitment to addressing the varying needs of its customers and their patients, as well as society in general. Engineered with flexibility, quality and efficiency at its core, the SMART revolutionises high-mix/low-volume manufacturing by empowering pharmaceutical and medtech companies to leverage the benefits of full automation for their low-to-medium-volume projects. Looking ahead, SHL will continue advancing its modular equipment technologies to further support its customers in their missions to bring life-changing treatments to patients worldwide.
REFERENCES
- Chung L, Fluetsch G, “Modularizing Assembly and Testing Equipment for Auto and Pen Injectors”. Presentation, PDA Universe of Pre-Filled Syringes and Injection Devices Conference, Gothenburg, Sweden, 2019.
- “SHL Medical shortlisted for the CPHI Pharma Awards 2022”. Press Release, SHL Medical, Oct 6, 2022.
- “What is PackML?”. Web Page, OMAC, accessed Jun 2024.
- Gertz F, Fluetsch G, “Applications of Deep Learning in Medical Device Manufacturing“. ONdrugDelivery, Issue 110 (August 2020), pp 6–11.